7+ Arc Flash Safety Tips – [Quick and Easy for 2023]
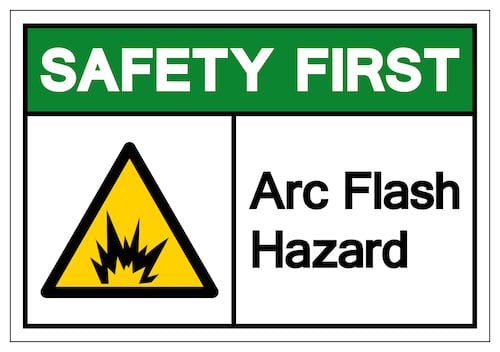
Any job that involves working on electrical equipment must prioritize educating employees on arc flash safety. Due to their explosive power and extremely high temperatures, arc flashes pose a serious risk to employee safety. All workers should be aware of the following arc flash safety tips to ensure the workplace remains as protected as possible from the threat of an explosion. These tips are also a great complement to our full-length arc flash safety training program.
What is Arc Flash?
An arc flash incident happens when an electrical current travels outside its intended path, from one conductor to another or into the ground. The resulting electrical explosion emits blinding light and extreme heat, which can cause serious injury. Any electrical worker unlucky enough to be caught in the arc blast may suffer severe burns, electric shock, or even death.
The initial blast isn’t the only part of an arc flash incident that can cause injury. Flying shrapnel, hot gases, molten metal, and loose debris can cause catastrophic damage to employees and the facility.
Arc flash safety training is necessary to ensure employee safety and lessen the risk of an arc flash. The National Fire Protection Association outlines protective measures to prevent arc flashes in its guidelines on electrical safety, the NFPA 70e. Though not mandated by federal law, this code is endorsed by OSHA as a definitive guide to reducing the risk of an arc blast.
The severity of an arc flash depends on several factors, including the confinement around the electrical arc, the condition of the electrical system, and the amount of current running through the electric arc. An arc flash is just one of many types of electrical hazards found in the workplace.
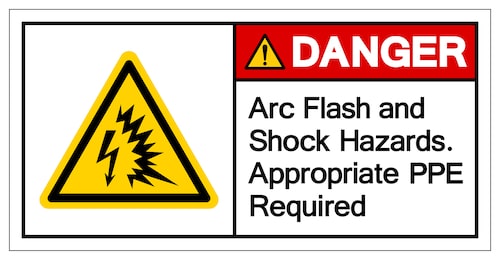
Potential Arc Flash Hazards
Employee error and improper risk assessment are two of the leading causes of arc flash in the workplace. Lowering the chances of an e-hazard should be your first priority if you own or manage a workplace where electrical equipment is used or serviced.
Here are a few of the most common hazards that can lead to an arc flash incident.
1. Faulty Electrical Equipment
Electrical equipment failure is one of the primary causes of arc flash. Poor maintenance of energized equipment puts electrical workers at risk and increases the likelihood of an arc flash incident. A qualified person should perform an arc flash risk assessment as part of your workplace’s routine inspections.
Damaged or malfunctioning circuit breakers can also constitute an arc flash hazard. Ensure all breakers are serviced regularly to lower the risk of faulty wires starting a fire or to create an arc flash.
2. Using Non-Insulated Tools
Dropped tools that are not insulated instantly become an arc flash hazard when they make contact with energized electrical equipment. Workers who drop tools into live equipment are at a greater risk for arc flash injuries because they are usually well within the flash protection boundary. In these cases, even wearing personal protective equipment (PPE) may not mitigate the shock hazard.
Never allow non-insulated tools to be used on electric equipment, even if the machine has been de-energized. Ensure all employees know which tools are acceptable to use, and keep non-insulated tools in a separate location away from the live equipment.
3. Working on Live High Voltage Equipment
Working on live equipment is virtually never worth the risk. Most work permits issued for electrical maintenance stipulate that all equipment must be de-energized before the work can proceed.
De-energizing equipment before conducting maintenance plays a vital role in lowering the risk of arc flash. This often includes isolating electrical currents by locking out the circuit breaker. Lockout tagout procedures should be a key facet of safety training for all workers.
In the very rare circumstance that live equipment must be worked on, take every possible precaution, including wearing full protective gear and ushering every non-essential employee away from the area.
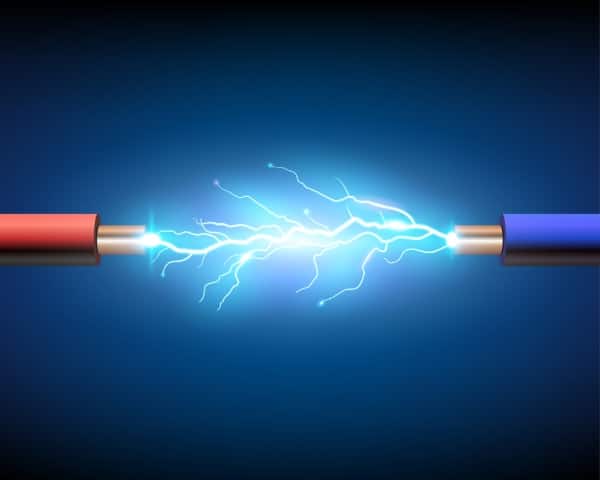
4. Insufficient Safety Training
Improperly following safety procedures can easily lead to arc flash hazards. Arc flash hazards are often caused by employee error. New and untrained employees are the most likely to make mistakes, so it’s vital to ensure new hires are trained as swiftly and thoroughly as possible before allowing them to service equipment.
Only qualified people should be allowed to work on de-energized equipment or stand within arc flash incident energy and protection boundaries. All others should remain at a safe distance at all times.
Tips for Preventing Arc Flash
The best defense against arc flashes is to take as many precautions as possible to prevent them from occurring in the first place. Additionally, proper work permits must be obtained before electrical equipment is used or serviced.
Here are several tips to follow to reduce the risk of ark flash.
1. Don’t Allow Electrical Work on Energized Equipment
Employees working on equipment in an energized state are needlessly risking their lives. Ensure all shutdown protocols are followed, and all relevant circuit breakers are locked and tagged before allowing work on the equipment to proceed.
2. Wear Personal Protective Equipment (PPE)
Personal protective equipment can help shield employees from the worst of an arc blast. Wearing proper PPE while servicing dangerous equipment also helps employees stay alert and aware of their surroundings. Protective equipment for electrical workers may include safety glasses, rubber gloves, face shields, heavy boots, and arc-resistant clothing.
3. Mandate Arc Flash Training for Electrical Workers
Arc flash safety training saves lives by ensuring employees know what to do to prevent dangerous situations, as well as how to respond should an arc flash occur. Untrained employees are at the greatest risk of causing an incident, so new hires should be monitored until they completely understand the proper safety precautions and procedures.
Further training may be necessary as new procedures are developed and added to the National Electrical Code (NEC). Incentivize employees to take electrical safety seriously by providing rewards for completing additional training.
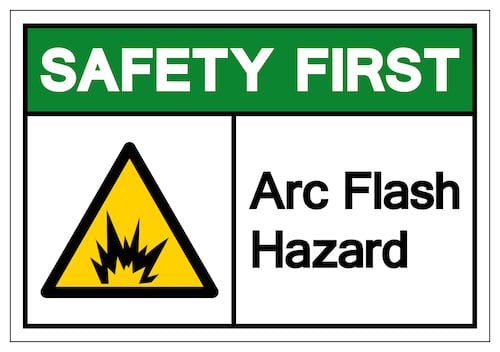
4. Stay Behind Protection Boundaries
National guidelines outline four zones that determine how much danger a worker will face during an arc flash.
The restricted approach boundary borders the zone immediately surrounding the piece of equipment. Workers should avoid approaching this boundary any time there’s a live current. Being present within this line when a blast occurs will surely result in death.
The next boundary is called the limited approach. Within this space, employees run the risk of shock, third-degree burns, and other life-threatening injuries.
The arc flash boundary encircles the zone at the outer limits of the potential blast radius. Employees within this line may experience second-degree burns, but their injuries are less likely to result in death.
All employees should endeavor to remain outside the arc flash boundary of any given piece of equipment. Knowing where these boundaries are is an essential aspect of safety awareness.
5. Use Insulated Tools
Mistakes happen, and even the most seasoned worker sometimes drops tools on the ground. To lessen the risk of a dangerous incident, all tools used around electrical machinery should be insulated. Proper tools for electricians usually incorporate two types of insulation that meet industry standards and leave the least possible amount of metal exposed.
6. Contain or Reduce Incident Energy
A well-designed workplace should incorporate safety precautions that guard against arc flashes. For example, emergency shut-off procedures should be in place to make it easier for employees to cut off power to the arc as quickly as possible. Electrical equipment should be equipped with its own breaker box as an added failsafe against calamity.
7. Conduct Regular Risk Assessments
Regularly inspecting and maintaining electrical machinery will dramatically reduce the risk of a dangerous incident. The NFPA 70e suggests conducting a risk assessment on every piece of equipment in the workplace that operates at 50 volts or higher. You also need to make sure your facility has an arc flash incident response plan as well.
Throughout their inspection, the designated employee should pay special attention to circuit breakers, power cords, and any machines that have a history of poor performance or that have needed maintenance in the past. No detail is too small when evaluating the safety of electrical machinery in the workplace.
8. Use Labels
Any potentially hazardous machinery should be labeled to prevent untrained employees from making costly mistakes. Utilize restricted access labels to clarify that certain zones are off-limits to anyone who hasn’t been properly instructed in electrical safety.
Signs should also be applied to faulty or broken machinery. Encourage employees to shut off and label any equipment that seems to be malfunctioning.
What to Do if an Arc Flash Occurs
An arc flash event can cause devastating injuries. The first course of action in the event of an arc flash should be to take cover outside the protective boundary. If the blast’s electricity can be shut off safely, do so immediately.
If a victim is inside the protective boundary during the incident, avoid touching them. Shut off the power and call for emergency assistance right away. If the power cannot be shut off, try to remove the person from danger using non-conductive materials.
An arc flash incident will maintain itself as long as its power source remains intact. Please keep your eyes averted from the blast to reduce the risk of blindness, and encourage employees near the explosion to cover their ears or wear earplugs until the incident has been resolved.
Prioritize Electrical Safety in the Workplace With These Arc Flash Safety Tips
Arc flashes are relatively rare, but their devastating power means that every precaution should be followed to avoid an incident. No one should be exempt from following proper safety precautions in a workplace that incorporates energized machinery, whether they’re the newest employee or the vice president of the company.
Electrical workers should have a firm grasp of these arc flash safety tips before being authorized to conduct maintenance on electrical machinery. As long as these arc flash safety tips and good safe work practices are followed, workers should be kept safe from the worst incidents.