Warehouse Materials Handling Basics
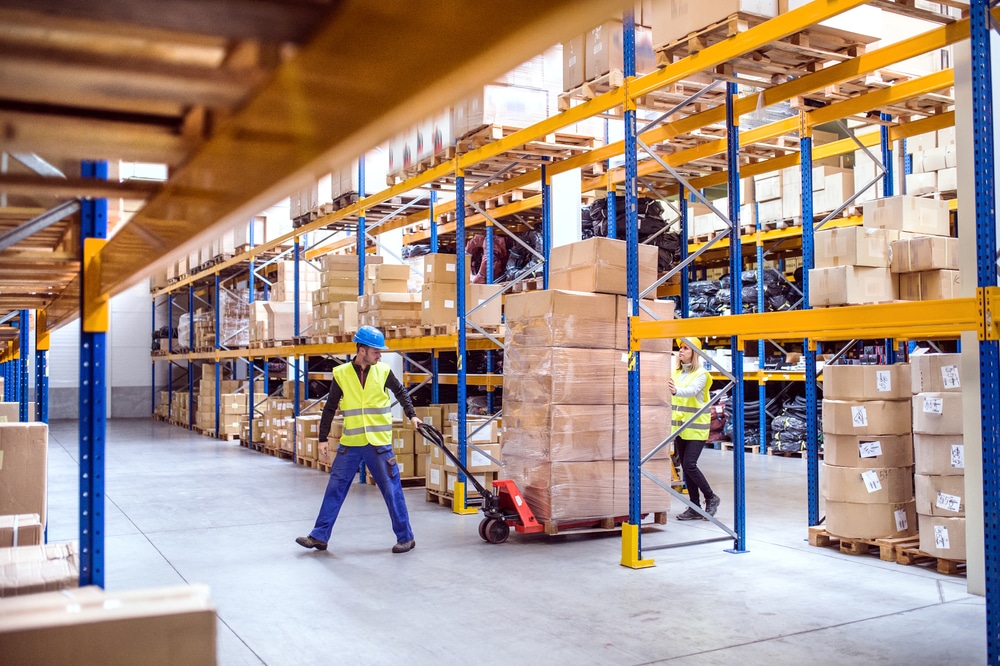
When it comes to the field of warehouse operations, few workflow aspects are more critical than material handling.
As the manager or proprietor of a warehouse or industrial facility, one of your most important warehouse objectives should be improving the efficiency of your material handling system.
This is more than just worker safety and protecting goods and raw materials from harm. Employing efficient logistics in your material handling processes can help you save money, produce a larger volume of products, and create a healthier warehouse environment overall.
And with the compound annual growth rate for the material handling industry rising exponentially, it’s more important now than ever before to seriously consider implementing these solutions.
Read on below to learn how the warehouse material handling process works and how to improve it for maximum safety and efficiency. If you need to train your workers, we have a full safety training for warehouse employees as well.
Material Handling Defined
Material handling refers to the processes by which goods, raw materials, and products in various stages of development are moved throughout the warehouse facility and the distribution processes that allow them to be transported to customers and retail centers.
Material handling operations pose unique challenges, including managing employee safety, timely delivery, and product quality protection. These procedures are often associated with specially designed warehouse material handling equipment intended to make the processes go smoother.
Material handling is usually divided into two types: manual and automated.
Manual material handling involves human employees physically moving goods and raw materials through their efforts, sometimes with simple tools like hand trucks.
Automated material handling refers to using advanced technology to perform material handling tasks without the aid of human workers.
Of course, OSHA also has a Standard around Materials Handling that you should also read up on.
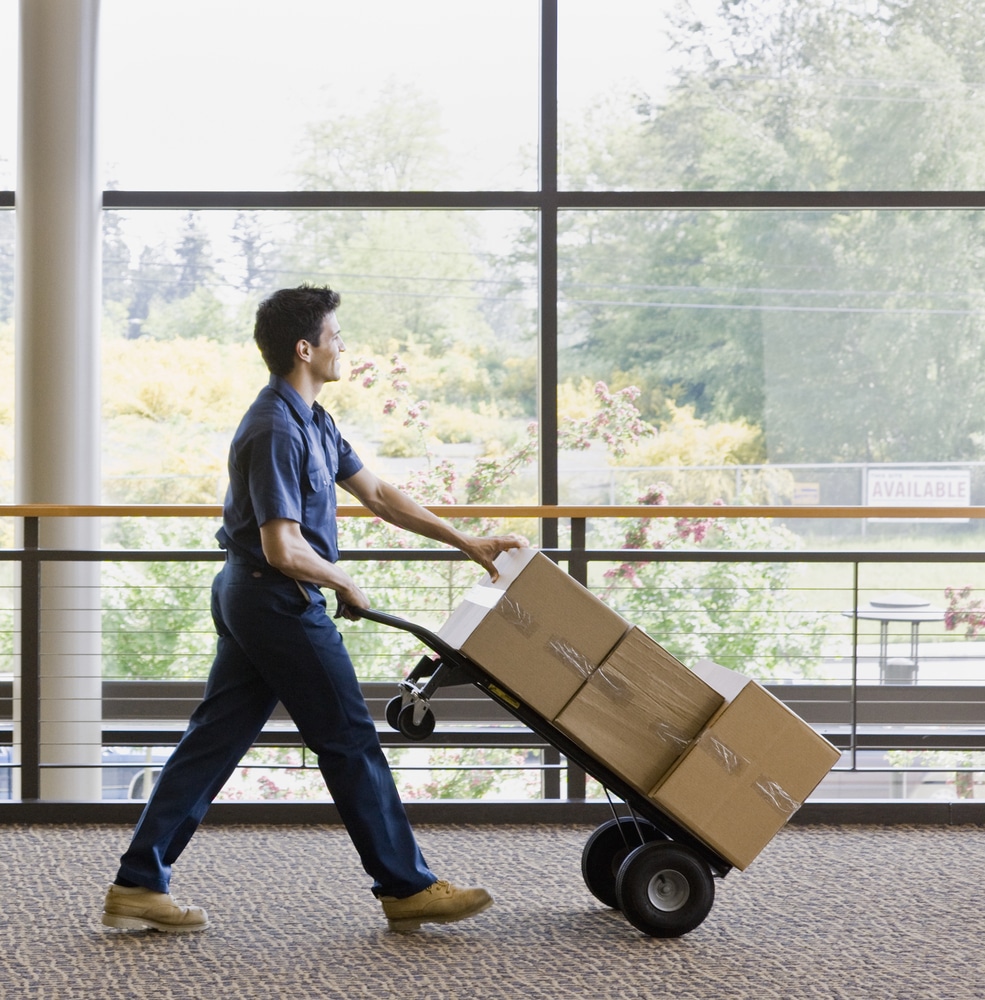
Material Handling Equipment
Material handling processes in industrial settings typically necessitate using a wide range of warehouse handling equipment. Since warehouses are filled with dangers, you should always train your employees on proper materials handling and safety best practices.
This material handling equipment includes manually operated tools, such as hand trucks, and automated systems that handle the protection, storage, and control of goods without significant human intervention.
Learn more about the different forms of material handling equipment below.
Manual Material Handling Equipment
These material handling tools are intended to be operated by human workers to facilitate the movement, protection, storage, and inventory management of goods within the warehouse. Workers use pallet jacks, or pallet trucks, to move inventory around the facility.
Industrial trucks are used to transport larger loads and longer distances than pallet jacks can handle. Workers typically use hand carts for lighter loads than are reasonable for either pallet or industrial trucks.
Automated Material Handling Equipment
An automated system uses computer-controlled technology to handle material tasks without human intervention. The most elaborately engineered systems use autonomous mobile robots and automated guided vehicles, while more modest operations use production lines consisting of conveyor systems.
A conveyor system is more of a semi-automated solution, requiring some human labor. However, full automation is available for almost everything your products need, including movement, protection, storage, and more.
For instance, automated storage and retrieval systems are commonly used in many plants. These storage systems unload materials safely and stow them away carefully without being controlled by a human worker.
What Are the 3 Basic Stages of Materials Handling?
What is the material handling process?
Most material handling processes can be broken down into three main stages of activity.
From the time the unit load of a product is defined to the time that product is distributed to the consumer, both human workers and pieces of automated equipment must work to meticulously uphold the standards set by the manufacturing plant manager to facilitate safe material movement and safeguard the protection, storage, and control of goods to be sold in the order described below.
Defining Unit Loads
Clearly defined unit loads are the key to efficient handling and inventory management. A unit load is a parcel of materials that can be transported as one indivisible unit.
It is important that the size matches the size of your equipment and storage receptacles to maximize efficiency, so you’ll want to set this parameter early in your decision-making process. Don’t forget to consider your inventory management objective when determining this figure.
Internal Handling
Unit loads are then moved through the facility according to their needs using the various tools available in a particular warehouse.
This is the stage where best practices are most important when items are subject to the most handling. Whether the warehouse relies on automation or the physical strength of its workers, the integrity of each item must be protected.
Distribution
Finally, warehouses must ensure that the products they’ve worked so hard to create and process are moved safely to their destinations so they can reach their future consumers.
They must be loaded securely onto trucks and other transport vehicles to be taken to retail stores or distribution centers, where shoppers can purchase or transport them to further destinations.
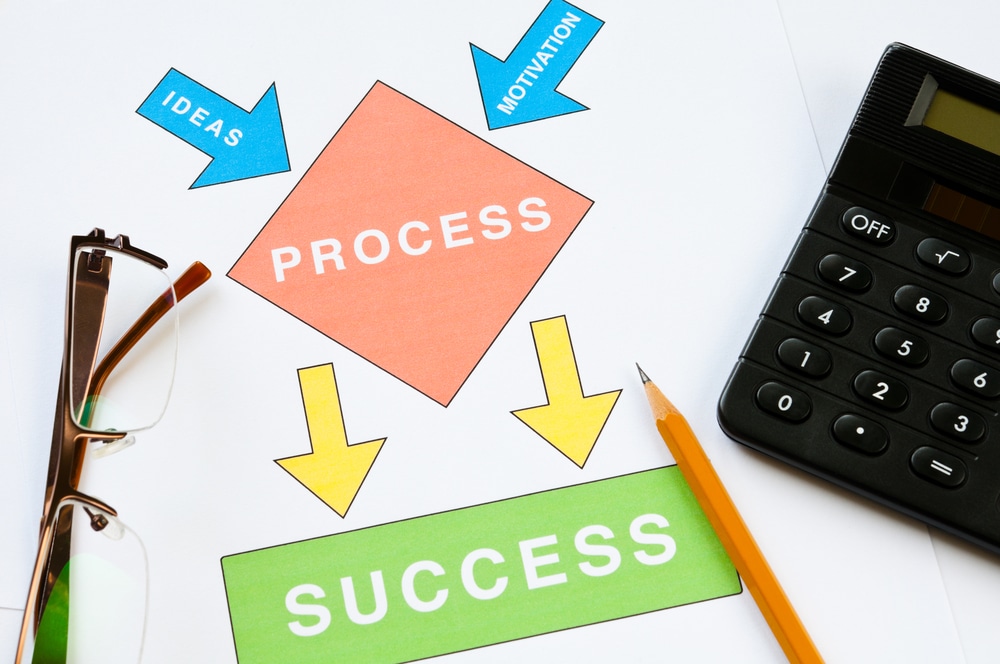
Designing an Effective Material Handling Process
When it comes to safely handling materials and avoiding production holdups to keep the supply chain running smoothly, it is imperative to employ a well-designed material-handling system in your warehouse.
There are many factors to consider to design efficient material handling systems, but the development process is rather simple. Follow the guidelines and material handling methods below for optimal results.
Assess the Existing Material Handling Equipment
First, perform a thorough analysis of the situation as it is. Identify any pieces of machinery that are obsolete or inefficient, and take note of them for future reference.
Look for practices causing workflow to slow down or pathways requiring workers to transport goods further than necessary.
Select and Implement More Suitable Material Handling Equipment
Now that you’ve identified any problem areas, it’s time to devise a solution.
If your existing machinery wasn’t moving enough product, consider upgrading your base model to a larger machine that controls bulk materials.
Rearrange your floor plan to shorten the distance your goods need to travel and improve the general workflow.
Enforce More Efficient Logistics
Be sure to educate everyone in the warehouse on the proper safety measures and protocols they should be following so that everything runs smoothly.
Put new standards in place to improve the efficiency of organization, storage, and workflow. Consider automating certain processes to free up employees to handle other tasks.
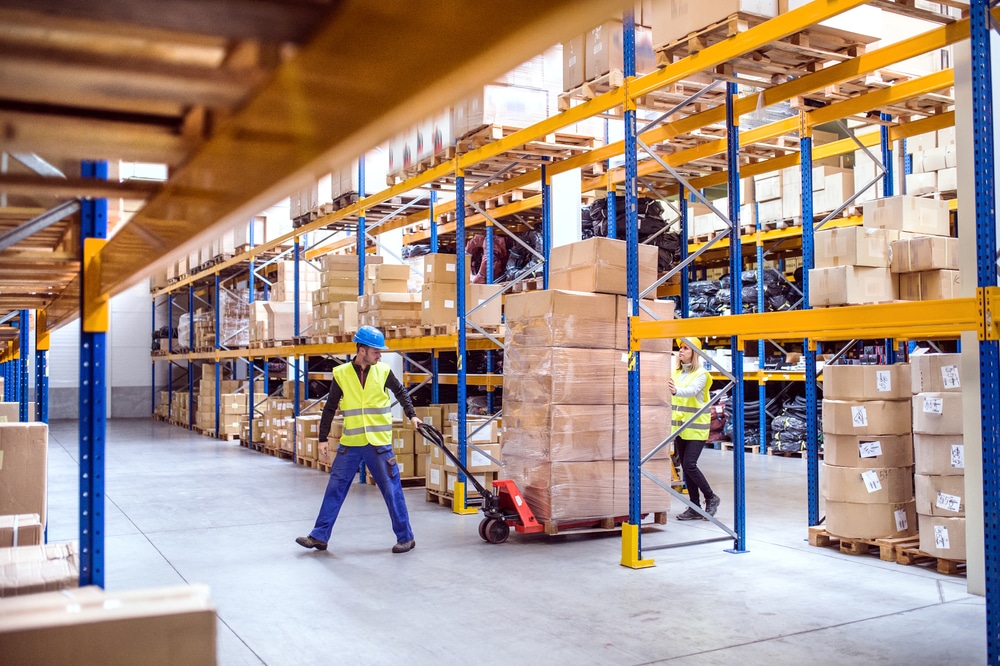
5 Important Factors to Consider When Developing Material Handling Systems
To meet your unique material handling needs and achieve your specific goals on the production floor, you’ll need to consider many different aspects.
Developing an efficient system for safe material handling requires a holistic approach, so remember to devote your attention equally to every facet of production.
1. Efficiency
When maximizing efficiency in your material handling processes, always keep it simple. Eliminate unnecessary movements, replace obsolete material handling equipment immediately, and use your floor space wisely.
Consider your warehouse layout very carefully. Place the different pieces of material handling equipment in a way that makes them readily accessible to employees.
Design pathways so workers can transport materials by traveling only the shortest possible distance. Don’t make the mistake of neglecting overhead space when planning your warehouse layout.
2. Holistic Approach
Remember to consider the entire system instead of getting bogged down in the details of one or two aspects.
Evaluate your old system first to decide what practices work and what needs to be changed, and determine if you’ll need to upgrade or swap out any of your existing handling equipment.
Discuss changes with members from every department to isolate problems you may not have noticed on your own. Consider the needs of every associate and every stage in your product’s life cycle to better identify necessary changes.
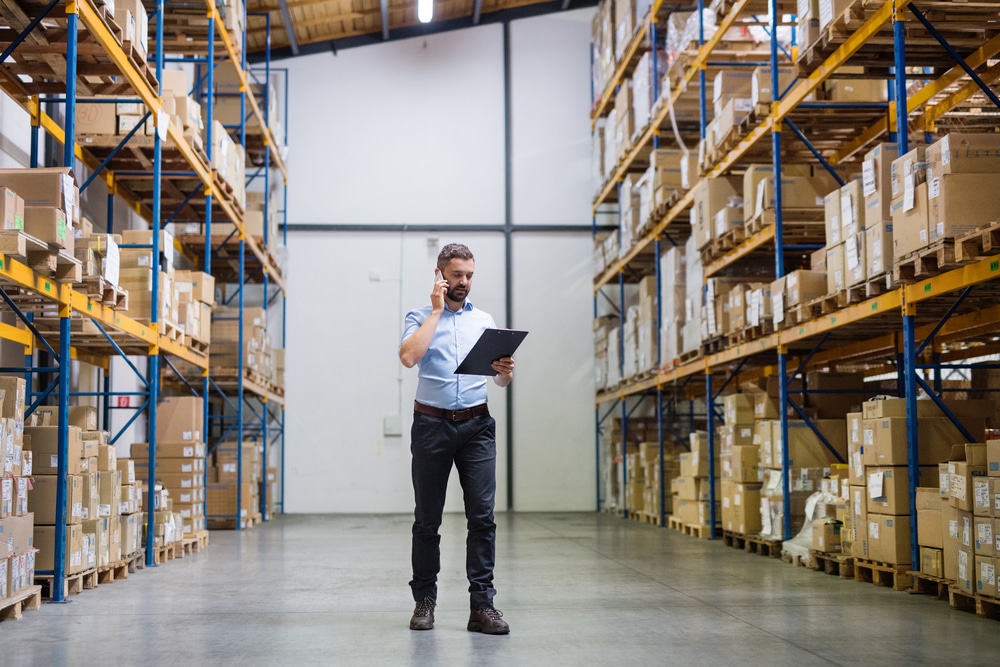
Worker Friendliness
Keeping your employees safe and productive should always be your number one goal, especially when developing your system for material handling.
Ensure that all of your practices and techniques are made standard so your operations have internal consistency that adheres to worker expectations.
Additionally, consider making changes that prioritize ergonomics. Choose the right material handling equipment for your workers’ needs, and ensure their safety is never compromised by working with unsafe or ineffective tools.
3. Attention to Detail
Make sure you plan thoroughly to establish standards for every aspect of the system. For instance, do your best to choose a unit load that makes sense for your material handling equipment and storage systems.
Do not exceed the space that your pallet racks will allow for, and do not underuse the space that you are allotted. Consider these details carefully before you move ahead with the planning process.
Details also means keeping the job site clean. There are best practices for warehouse housekeeping and cleanliness and you should follow those.
4. Equipment
Determine if your operation is better off prioritizing manual handling or if you’d be better served by a computer-controlled system composed primarily of automated material handling equipment.
Consider innovative space utilization techniques, such as installing bucket elevators or using bulk material handling equipment to maximize storage density.
Robotic delivery systems can be very useful in the right environment, but they’re unnecessary for all manufacturing plants. Consider if your operation would be better suited to middle-of-the-road semi-automated solutions before investing in this costly technology.
5. Environmental Impact
Large companies producing mass amounts of goods have a responsibility to the planet and the rest of society to ensure that their operations are as environmentally conscious as possible. Implement ecological best practices in your warehouse and enforce them regularly.
Store materials in a way that cuts back on unnecessary waste from single-use plastics. Hire an environmental impact consultant to help identify wasteful practices that could easily be adjusted.
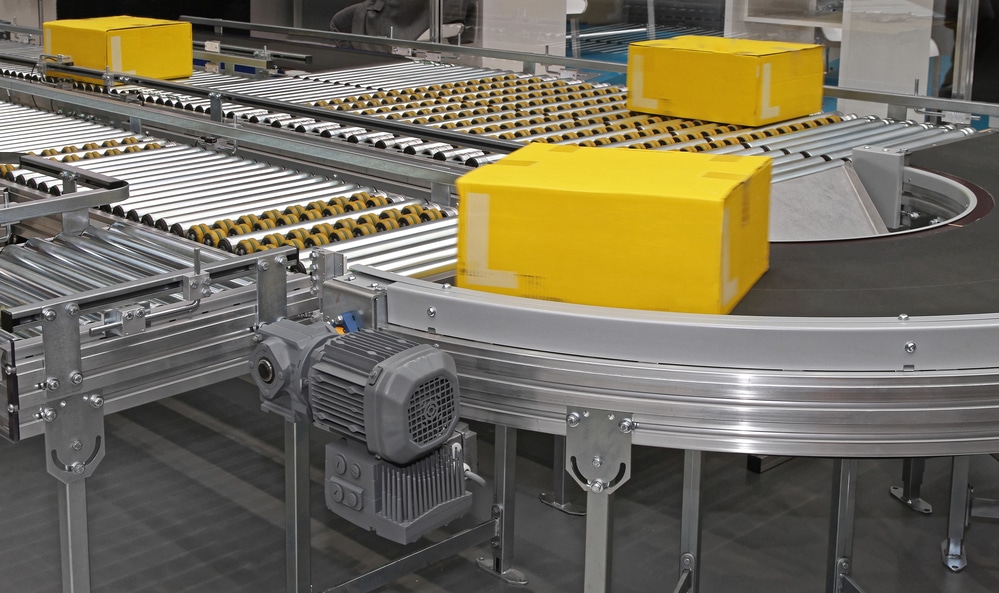
Advances in Material Handling Technology
Thanks to the rapidly developing world of industrial technologies, more and more cutting-edge solutions to warehouse management problems are happening daily.
It’s becoming steadily more commonplace for warehouses to be fully machine operated and controlled by a highly advanced computer system that maximizes efficiency in ways humans can only dream of. If your operation can afford the expense, it’s an investment worth considering.
Why Prioritize Operational Efficiency in Material Handling?
Making this aspect of your warehouse operations a top priority is a huge step toward increasing your profits. Inefficient systems lose unbelievable amounts of money.
By eliminating downtime and increasing production volume through basic machinery upgrades and layout rearranging, you’ll increase your revenue in ways you never imagined.
Proper Material Handling Systems Are Important
Ensuring that your warehouse material handling processes are optimized for peak efficiency and security is non-negotiable for any employer in supply chain management or the industrial sector.
An efficient warehouse management system is the key to improving worker safety and saving money on unnecessary processing costs or maintaining obsolete storage and handling equipment.
Employ some warehouse material handling tips in your workplace today and see how quickly you start reaping the benefits.