Understanding OSHA’s Machine Guarding Standards
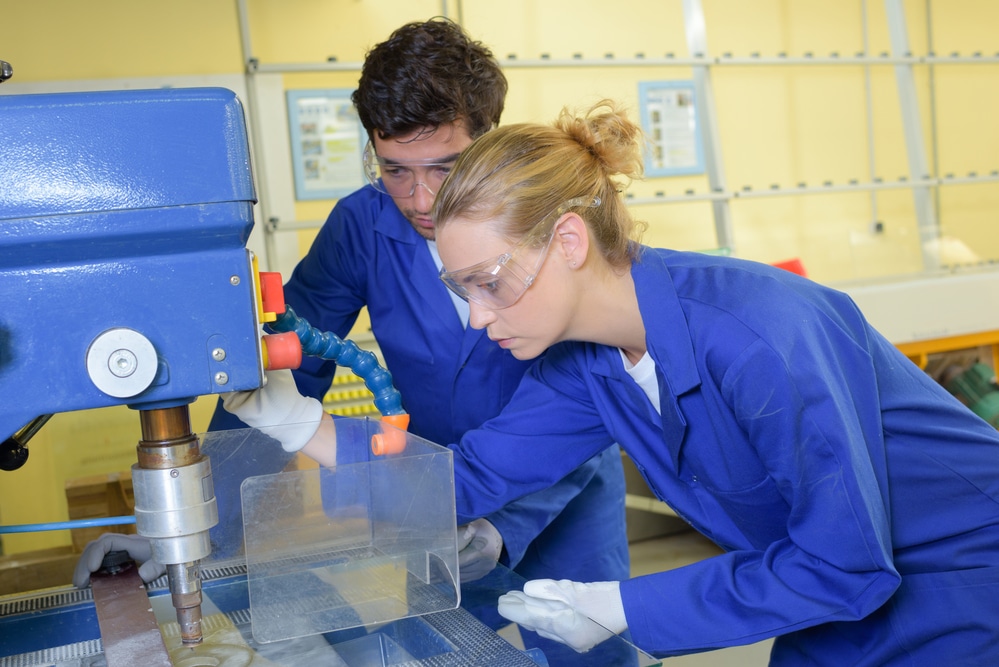
Compliance with the Occupational Safety and Health Administration (OSHA) mechanical machine guarding standards can be confusing, as the regulations are generic but have specific applications.
Knowing the right place to use machine guards will help meet regulations, keep employees from harm, and save companies from paying hefty fines for unsafe working conditions.
Through the use of training and precautions, machine guarding requirements can be met to avoid injury in the workplace. Before that can be done, a few things must be understood about the types of protections in place for worker safety. If you want a course to teach your employees all about machine guarding we have that available too.
What Are the Standards for Machine Safeguarding?
OSHA machine guarding standards are regulations to ensure that equipment like power presses, milling machines, and machines for forming rolls do not harm employees during the operating cycle. The standards involve using one or more methods to protect workers in a danger zone from rotating parts or hazardous mechanical motions.
These regulations mandate that guards be put in place to protect employees. They should be affixed to the machine when possible, and all devices must conform to appropriate standards during the operation cycle. Also, machine safety sensors can be affixed to machines to prevent injuries.
OSHA compliance covers a variety of scenarios, but what does this mean for specific machinery?
Guards are to be designed and constructed so that they cannot be tampered with while the machine is running. Dangerous equipment must be guarded against at all times when workers are using it. These safety precautions can save lives and spare companies from getting slammed with hefty fines and investigations.
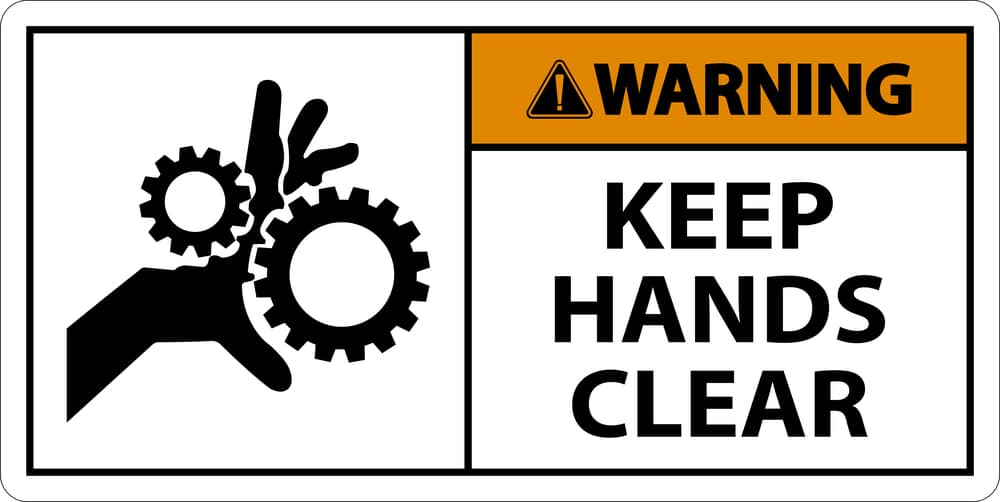
What Are the 3 Basic Areas That Need Machine Guarding?
OSHA standards for Machine Guarding (1910.212) highlight three areas essential to every piece of equipment that could be dangerous. Not all machines will need the same type of guards, but many will need a risk assessment to gauge the need for precautions.
These areas for concern are the point of operation, the mechanical power transmission apparatus, and the operating controls. While each area may not have the same hazards, knowing each one is important to ensure that guarding methods are effective.
Occupational safety requires proper training and awareness. Barriers can be used to create a safer workplace, especially with the points of operation and the controls.
1. The Point of Operation
The point of operation is where the work – like crushing or shearing materials – is performed. The point of operation also exposes workers to the most harm, as crushing devices and feed mechanisms can be danger zones without proper protections in place.
Employee exposure to machine operation can lead to crushing injuries, lacerations, and permanent disability in workers. Farmstead equipment, power saws, guillotine cutters, and revolving drums all present various hazards.
OSHA regulations condemn inadequately guarded machines for acting as an accident hazard in the workplace.
All areas where such dangerous machines are used must employ barrier guards or a guard enclosure to keep employees from sustaining injury on the job. These barriers can be interlocked guards that prevent barrel drums from revolving while the physical barriers are in place.
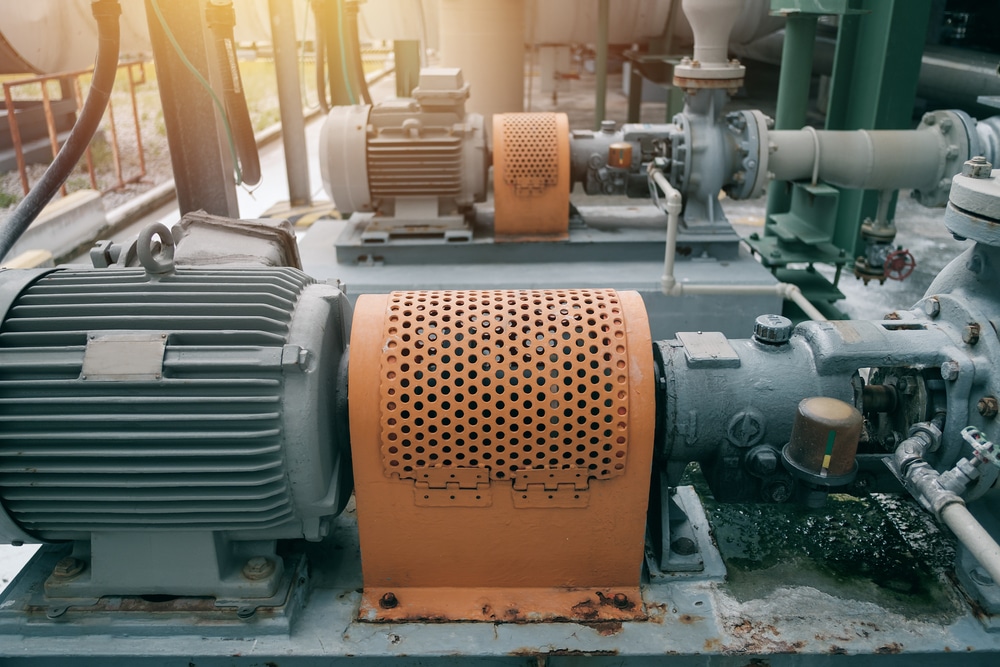
2. The Mechanical Power Transmission Apparatus
The power transmission apparatus supplies power to the machinery. Physical guards should be in place to ensure that the machine is not able to be turned on when not in use.
For example, guards can be attached to fixed machinery or a specific machine part to prevent them from being removed or tampered with. The machine area is a hazard zone when not properly secured.
OSHA violations can lead to serious injuries or even death. Complete protection for workers must be employed at every step in the process to comply with OSHA regulations.
3. The Operating Controls
The safety controls for operating machinery should be easily accessible in case of an emergency. To remain OSHA compliant, controls for safety must be enabled to ensure workers are not injured or worse while operating machinery on the job.
Machine operators must be trained extensively to protect other workers. Operation guarding strives to keep conveyor belts, rotating parts, and other machine parts from catching employees off-guard and causing harm.
Two-hand tripping devices are an example of machine guards used to make it safer for workers to operate a full revolution clutch power press.
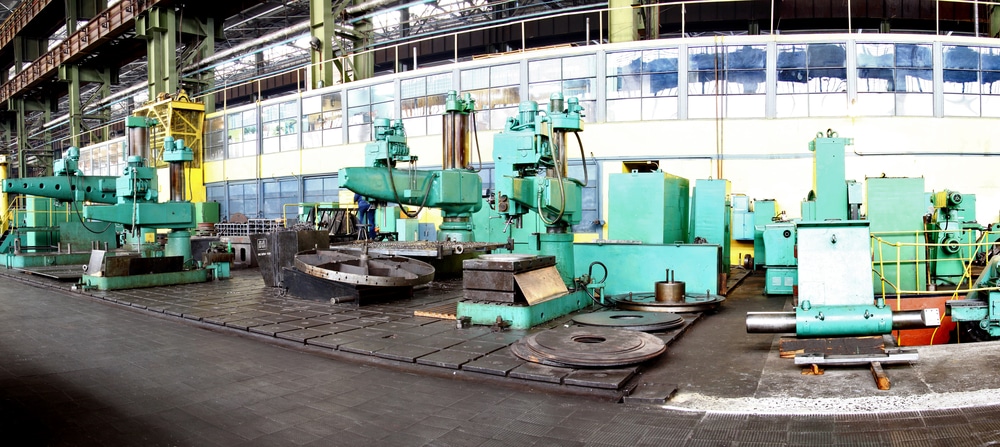
What Is the Purpose of Machine Guarding?
Machine guarding is designed to protect employees from a danger zone when mechanical equipment is involved. For workplace safety, this means knowing what type of guards need to be used and how one or more methods should be employed to lower the risk of severe or permanent injury.
All guarding device applications must prevent contact with the machine when workers are in the vicinity and must be secured in place so they can’t be tampered with. There are several different types of machine guards, and you should ensure your employees are educated in all of them that your facility uses.
Additionally, the guarding device cannot create new hazards or interfere with the machine’s operating cycle. The machinery must still be able to be lubricated properly as well while the guard is in place.
OSHA requires workplaces to employ barrier guards and electronic safety devices for heavy equipment, such as farm field equipment, to reduce the risk of harm to workers. The American National Standards Institute also has guidelines for how to handle machine guarding so as not to injure workers.
Why Do Machine Guarding Violations Happen?
Machine guarding violations happen for several reasons, such as user error. An employee may cut corners or not be properly trained, resulting in their injury or the injury of other employees.
Another reason is that employers may not take the necessary steps to put barriers in a fixed location, creating a hazard in the occupational workplace.
The hazards of machine operation – ingoing nip points, rotating parts, and dangers at the point of operation, for instance – create many opportunities for injuries in the workplace. Violations can be deadly and result in hefty fines and imprisonment.
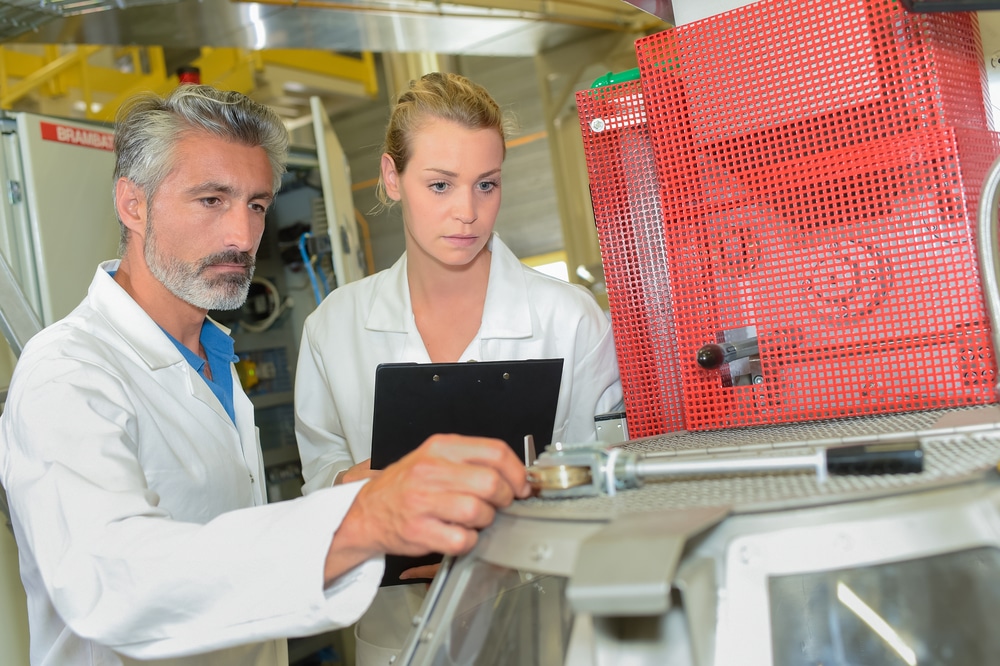
What Happens When Machine Guarding Violations Happen?
When the workplace is not up to OSHA standards, employees get hurt much more, from small abrasions to life-threatening injuries and disabilities.
Machine operation ingoing nip points, rotating parts, and the point of operation are all risky places for employees when not protected properly. Those held liable for the injuries or fatalities face fines of up to $10,000 and potential jail time for the violation.
What Are the Employer’s Responsibilities With Machine Guards?
The employer is responsible for ensuring that machine guards are provided by the manufacturer or otherwise. OSHA requires that guards are available, present, and properly installed to keep dangers like flying chips from hitting employees while they work.
Guards and other miscellaneous aids are the responsibility of the employer to provide. These aids also require point inspections to ensure that all can operate easily.
OSHA regulations are in place to protect workers, and while they may be difficult to follow to the letter, it is worth the effort to avoid potentially life-threatening injury.
Does OSHA Require Personal Protective Equipment?
OSHA requires PPE – like goggles, gloves, hard hats, and more – to keep employees safe. Basically, whatever PPE is appropriate for the specific situation should be provided to the employee.
When it comes to machine guarding methods, using visors, hard hats, and aprons when appropriate standards apply can save workers from dangerous situations.
Are There Exceptions for Machine Guarding for Specific Processes?
Machine guarding can vary depending on the circumstances, whether using the manufacturer’s provided guards or user-built guards. For instance, using a power saw to cut wood presents a hazard for flying chips, but metal has different risks involved.
It’s always best to check OSHA guidelines or speak with a supervisor for the best (and safest) plan of action. Any shear point can be a risk, but a quick search can determine what OSHA regulations call for and how they can be applied to the workplace.
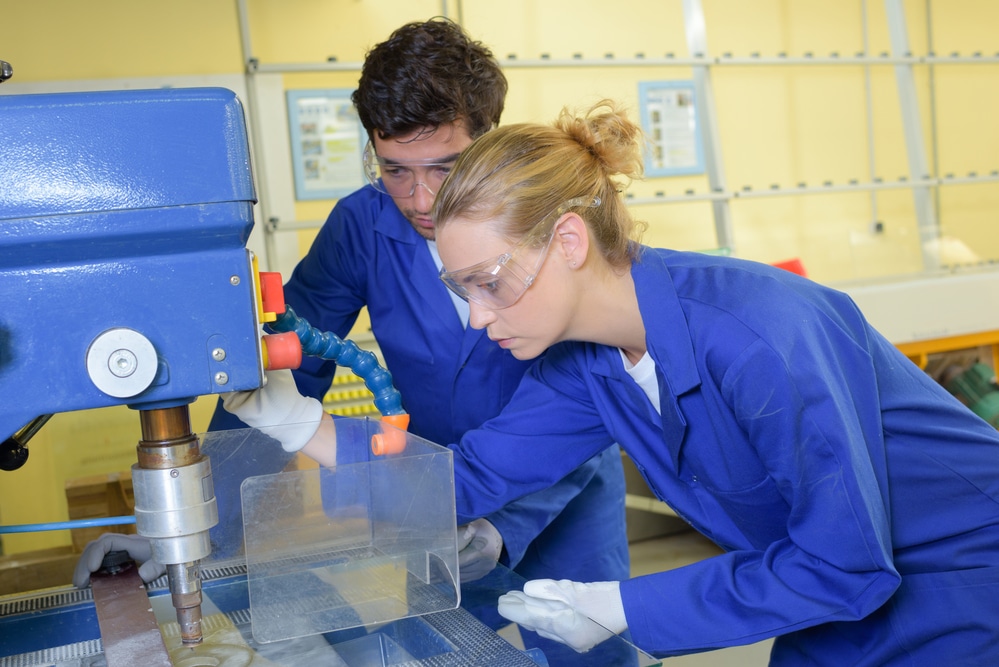
Guidelines for Moving Machinery
When the machinery itself moves – through conveyor belts, rotating pieces, or other potential nip points – the best course of action is to establish fixed barriers to prevent contact between machine and worker. These must be durable barriers that cannot be tampered with easily and include measures for motion detectors that stop the machine.
While OSHA requires these guards to be in place, simply having them does not guarantee compliance. To maximize worker safety and meet compliance standards, barriers must be effective and efficient rather than simply present.
Final Thoughts on OSHA Machine Guarding Standards
Acting in compliance with OSHA guidelines is crucial for the safety of workers across the board.
There are many ways that machines can cause harm when not handled properly. Understanding what machine guarding prevents and how it can be implemented protects employees from injury and the company from fines and penalties.
OSHA machine guard standards are in place to protect workers from harm in their daily tasks. Following these guidelines will create a safer and more productive workplace for all.