Types of Safety Sensors for Machine Guarding
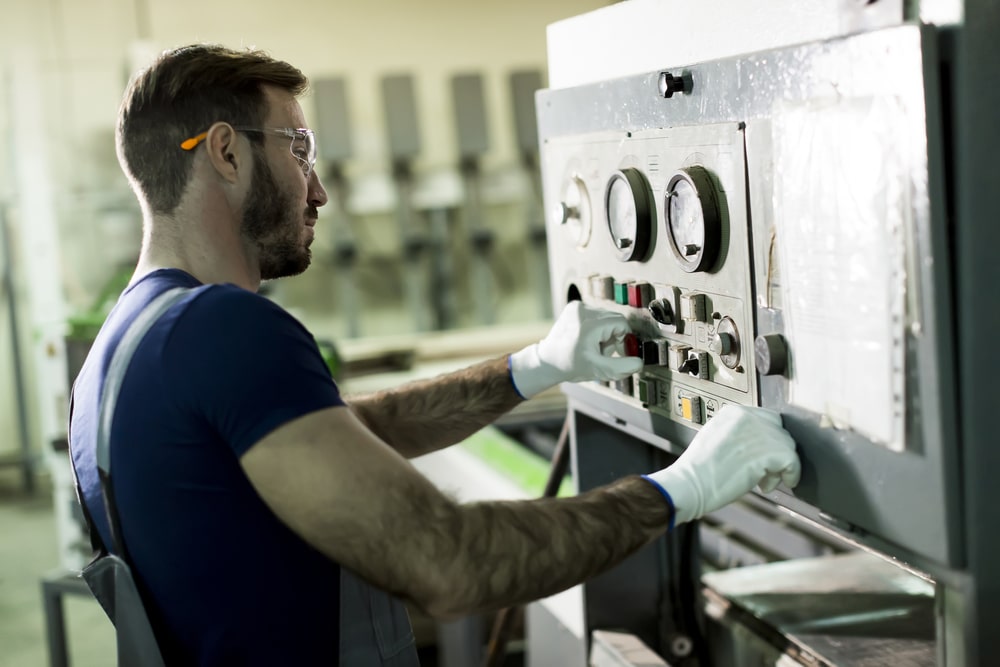
Personnel protection is important, even for automated processing. Industrial machines can have numerous safety applications added to help them meet machine safety guidelines. However, knowing what sensors can be used for each machine and how they function is essential.
Below, you will learn how to choose the right equipment to keep employees safe and what applications are available according to the machine and individualized machine safety rules. We have also developed a video-based training on machine guards that can help educate your employees about this important OSHA topic.
The Importance of Machine Guarding Sensors
Machine guards are the physical barriers between the operator and the point of operation to keep everyone in the area safe. Machine sensors are a type of guard that detects objects entering or exiting the safeguarded space to prevent injury.
In addition to sensors, safety switches can be added to specific machines. Safety switches can also be installed on the door of some machinery. In this case, the sensor sends signals to the machine door when it opens and closes. The sensor will prevent the machine from being in motion when someone is in the safeguarded area.
One of the most common safety switches is the RFID switch. Some RFID switches have a non-contact interlock design, while others are magnetically actuated with customizable designs for monitoring movable guards. You must put your machine guards on a maintenance and inspection schedule to ensure they are working properly, don’t become damaged, and serve their intended purpose without fail.
All applications serve unique purposes and prevent unwanted contact between employees and dangerous machinery. Without safety sensors, the risk of preventable injury in the workplace is higher. Of course, OSHA requires machine guarding if the tool or machine calls for it.
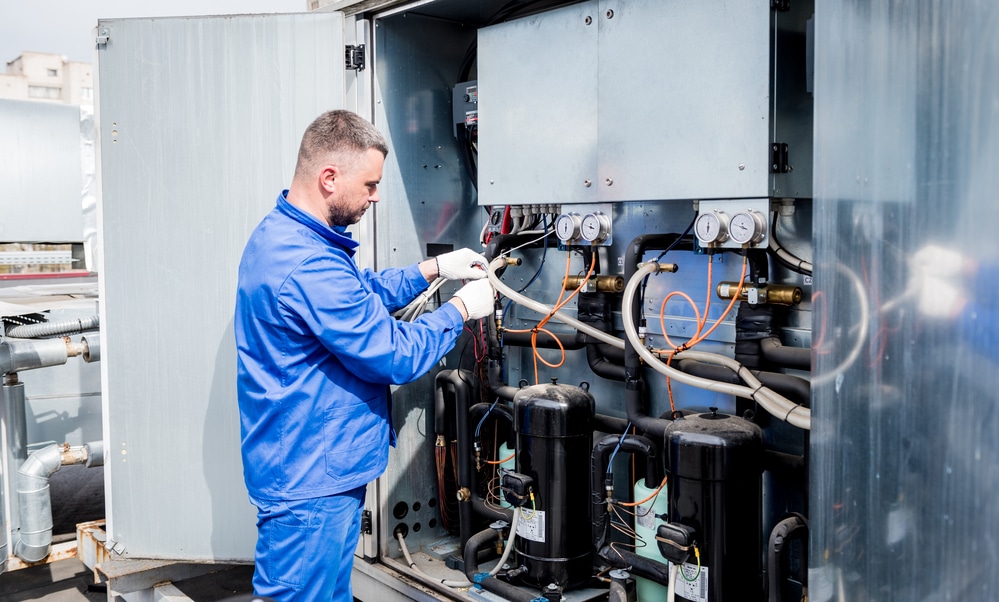
Guard Requirements
Guards must meet the minimum requirements to be reliable and efficient. These requirements include:
- Preventing contact: Hands, arms, legs, and other body parts should be safe from making contact with moving parts.
- Secure: Operators should not be able to access or tamper with non-adjustable guards easily. The guard should also be firmly fixed to the machine and durable enough to withstand everyday usage.
- Does not create new hazards: The guard should not create a new hazard in the workspace that can cause injury to users and other nearby workers.
- Does not create interference. Guards that make it difficult for users to complete their jobs comfortably and in a timely manner must not be used.
What Are Machine Safety Sensors?
Machine safety sensors are designed to protect personnel from injury caused by hazardous machine motion. All signals from safety sensors are safely monitored to ensure these complex systems are working efficiently.
The applications create a safe stop to work for machines and plants in dangerous and challenging environments. Whether it is food and beverage packaging, electronic assembly, fiber and textiles, or another environment involving industrial machinery, machine safety is necessary.
Types of Machine Safety Sensors
Different machine safety products are used for different machinery types to protect operators and other nearby workers properly. All of the sensors serve a different purpose and come with different features.
Individual solutions for machine safety are determined by OSHA and workplace guidelines. Switches, sensors, and other devices improve machine safety.
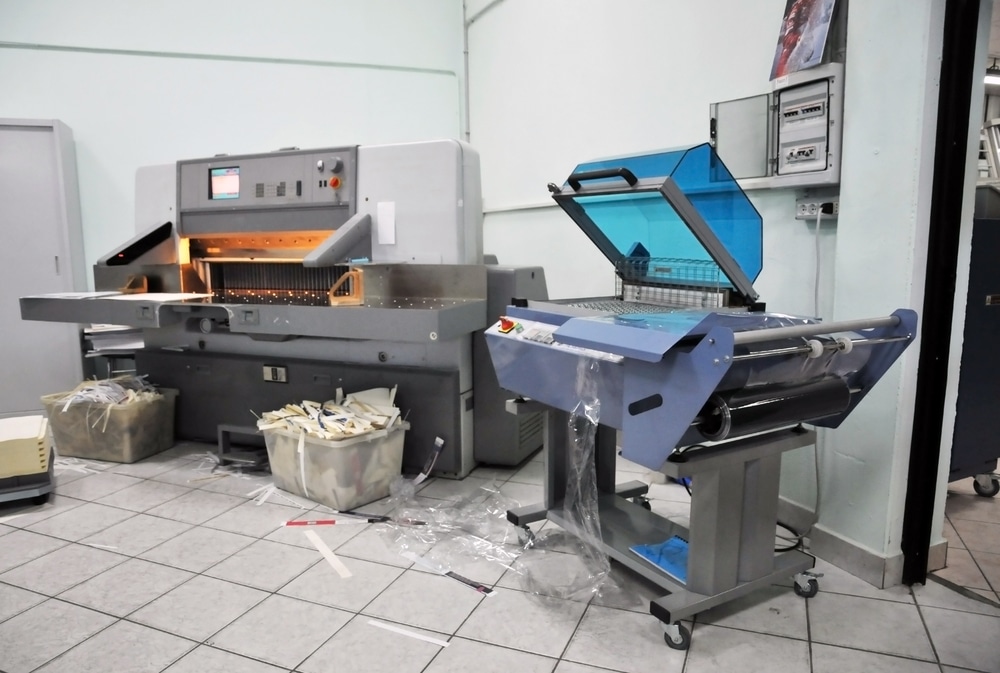
Photoelectric Sensors
Photoelectric sensors distinguish objects and changes in surface conditions through optical properties. These machine safety sensors are common in industrial manufacturing fields, including food and beverage, medical, material packaging and handling, and more.
These sensors come in various options depending on the tasks they are needed for. They can be used with or without a reflector. They can also be self-contained or long-range. This device also has different housing and mounting options to meet individual demands.
Safety Light Curtains
The safety light curtain has been around for more than 50 years, but it still functions relatively the same. Upgraded special features and mandatory national standards are why the light curtain is one of the most common machine safety applications.
Safety light curtains compromise a sender and a receiver. The sender sends infrared light beams to the receiver, which allows motion to occur once contact has been made. Any beam interruptions cause the sensors to generate a stop signal to stop hazardous motion.
Perimeter light curtains have a range to detect the whole body. Many other devices detect only a finger or a hand rather than the entire body. Still, the drawback of perimeter light curtains is that they cannot be used for point-of-operation safeguarding.
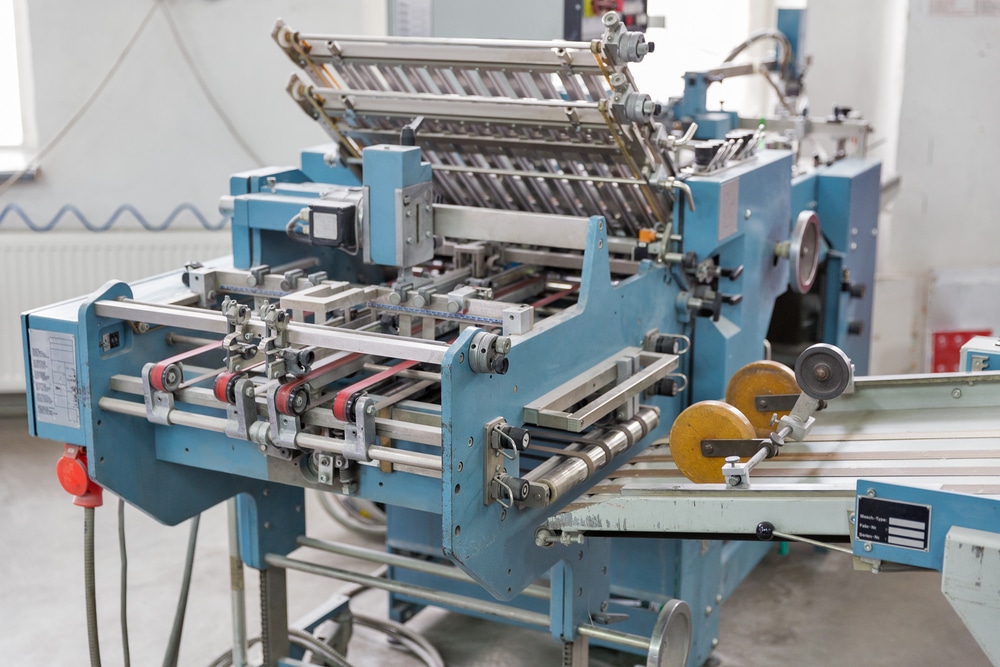
Safety Laser Scanners
A laser scanner uses an optical scanner for 2-D scanning using infrared laser beams. They emit short light pulses to determine the distance between objects, such as parts of the body and other objects within their range that can make contact. The scanner can be configured for multiple positions and zones to reduce injury risks.
Vision Systems
Vision systems are used for press break safeguarding and use vision-based optoelectronic technology. Camera sensors provide multiple safeguarding sensors without compromising operator safety.
A camera-based system and self-diagnostic tools characterize these systems. It’s designed to report when adjustments are needed and where the proper alignment is. Vision systems are reliable and easy to access.
Safety Control Units
Safety control units have a modular design with up to eight units that can connect to a single unit. This equipment offers functions including start/restart, muting, override, interlock, and emergency stop buttons.
It can control thru-beam sensors or a connection device for safety light curtains, switches, and other machine safety applications. Remember that industrial machines can have multiple safety devices attached for optimum security.
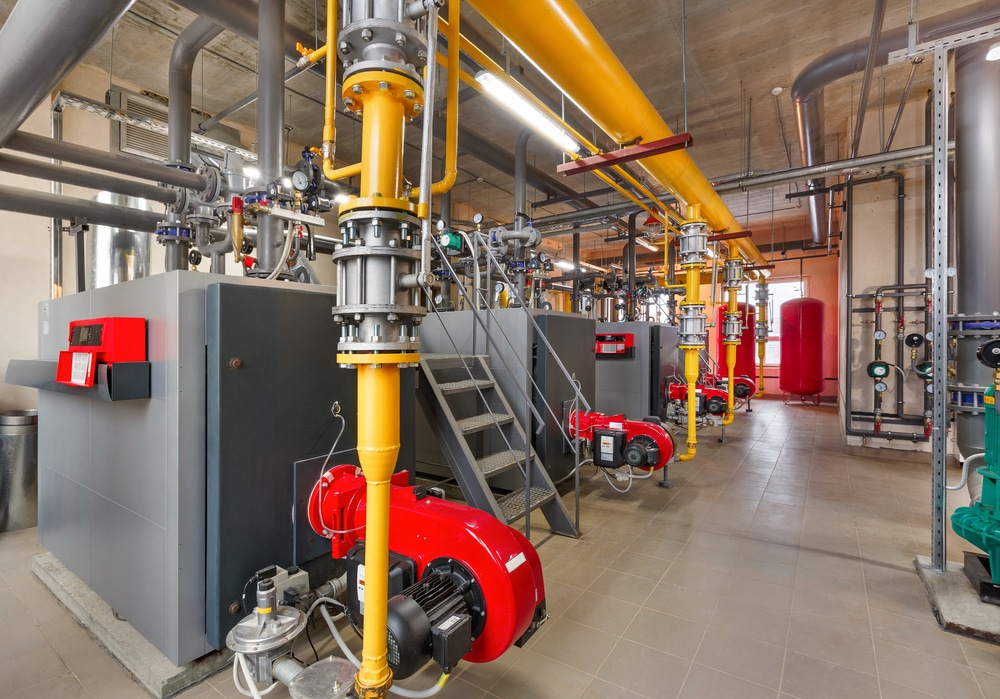
FAQs
What Are Four Machine Safeguard Devices?
Safeguarding devices are attachments or controls that prevent employees from accessing hazardous machine areas. The four device types are:
- Fixed
- Adjustable
- Interlocked
- Self-adjusting
What Are the OSHA Requirements for Machine Guarding?
According to OSHA, one or more methods of machine guarding are to be provided to protect operators and other employees in the machine area from hazards created by the point of operation. Guards should be affixed where possible and secured elsewhere if attachment is not possible.
What Are the Three Basic Areas That Need Machine Guarding?
All machines have three fundamental areas: the operating controls, the point of operation, and the power transmission device. Despite all machines having the same basic components, their safeguarding needs vary according to operator involvement and physical characteristics.
What Are the Different Types of Safety Sensors?
The different types of safety sensors include:
- Photoelectric sensors
- Presence-sensing devices
- Thru-beam sensors
- Diffuse mode sensors
- Distance sensors
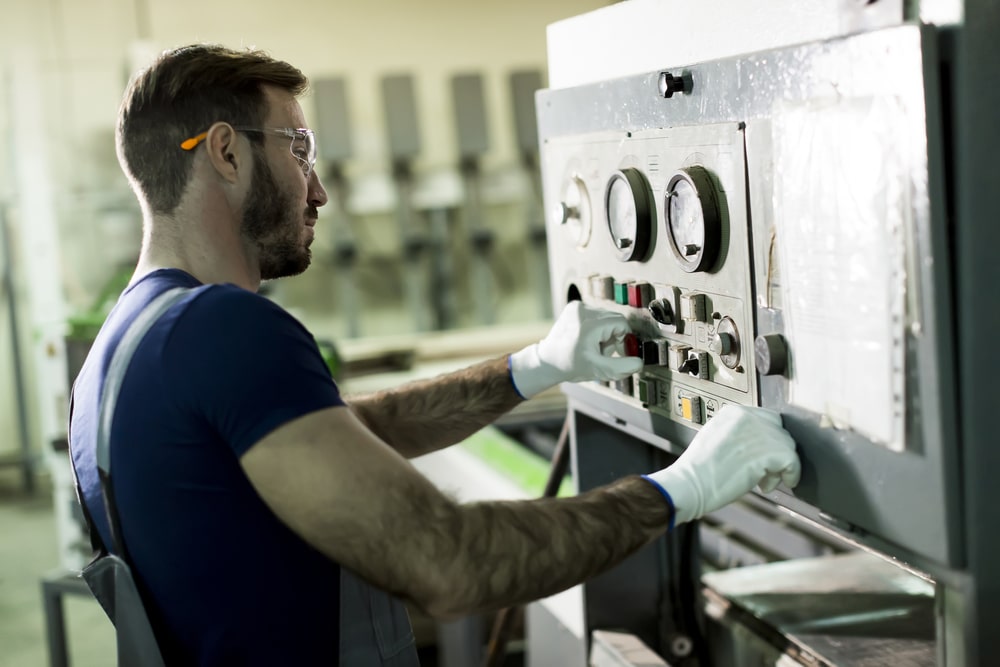
Conclusion
Selecting the appropriate machine safety sensors requires identifying and quantifying machine risk. Some risks cannot be eliminated through design, so all workers must use safety devices to prevent hazards such as crushing, cutting, clamping, snatching, puncturing, or shocking.
Safety-related functions depend on different industries and the industrial machines used for particular tasks. With that in mind, you can find the perfect solution to mitigate risk on the job site and prevent injuries.