Machine Guard Maintenance and Inspection
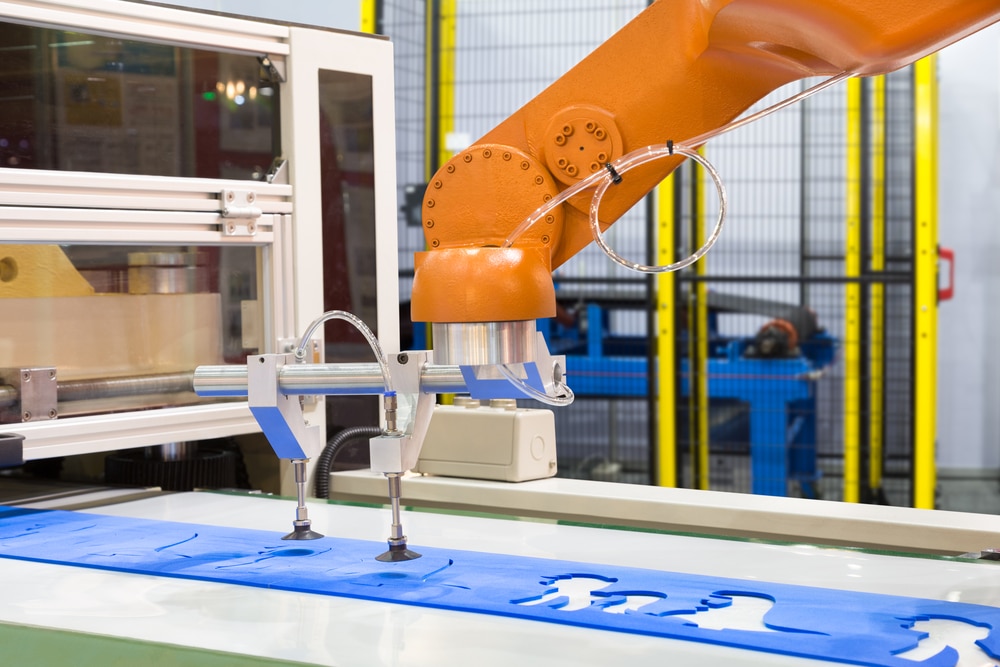
Moving machinery poses many dangers to any operator or maintenance worker using the machine in question.
Turning connecting rods can fracture an arm; saw blades can sever fingers. Many other injuries can result, including burns and blindness from flying debris.` That’s why proper maintenance and inspection of your machine guards is important. Maintaining maintenance records and inspection schedules can help ensure your operation runs smoothly.
We do offer full machine guard training for your employees as well.
What Are the Responsibilities of Machine Guarding?
Anywhere that a hazard exists, guards are necessary to protect workers. These guards prevent contact between any part of the operators’ bodies and any moving components of the machine.
Quite apart from the potential for workplace incidents to maim or kill affected employees, OSHA takes infringements of safeguarding regulations extremely seriously, levying severe fines in such cases.
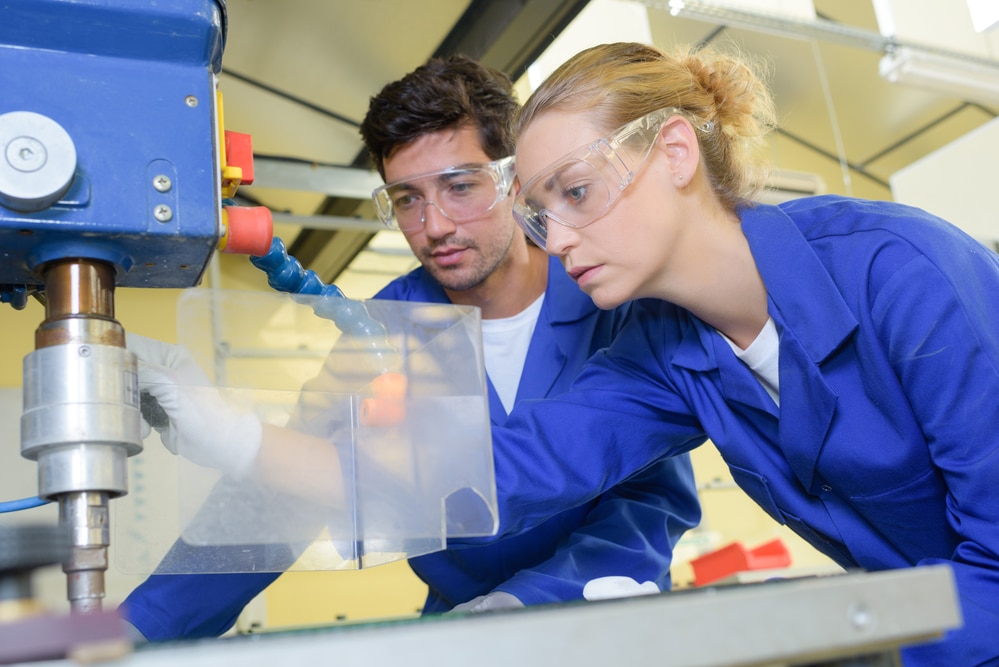
The Importance of Regular Maintenance of Machine Guards
Protecting workers requires a proactive approach to safeguards. Regular inspection identifies potential points of failure in machine guards while guard maintenance extends their lifespan.
Failed or failing safety devices do not provide adequate isolation from such hazards and must be repaired or replaced. They lead operators to believe that they are protected when they are not.
Repair procedures contribute significantly to workplace safety and prevent severe injuries stemming from accidental contact with moving parts.
While it may be tempting to cut costs by repairing and replacing only when an accident occurs, this is a false economy.
Who Should Be Responsible for Inspection and Maintenance?
Inspection is something that everyone should do, but it should not be everyone’s responsibility. Drill it into your machine operators so that they can inspect the machine and its guards before using it for their own safety.
The designated safety officer for the facility is responsible for conducting daily inspections of all machines and their guards and overseeing the safe maintenance of these components.
Maintenance must only be performed by appropriately trained and experienced machine guard maintenance personnel.
It may be tempting to do a maintenance job quickly, but correct procedures must be followed to isolate the machine from its power source first and then reinstall all guards before restoring power.
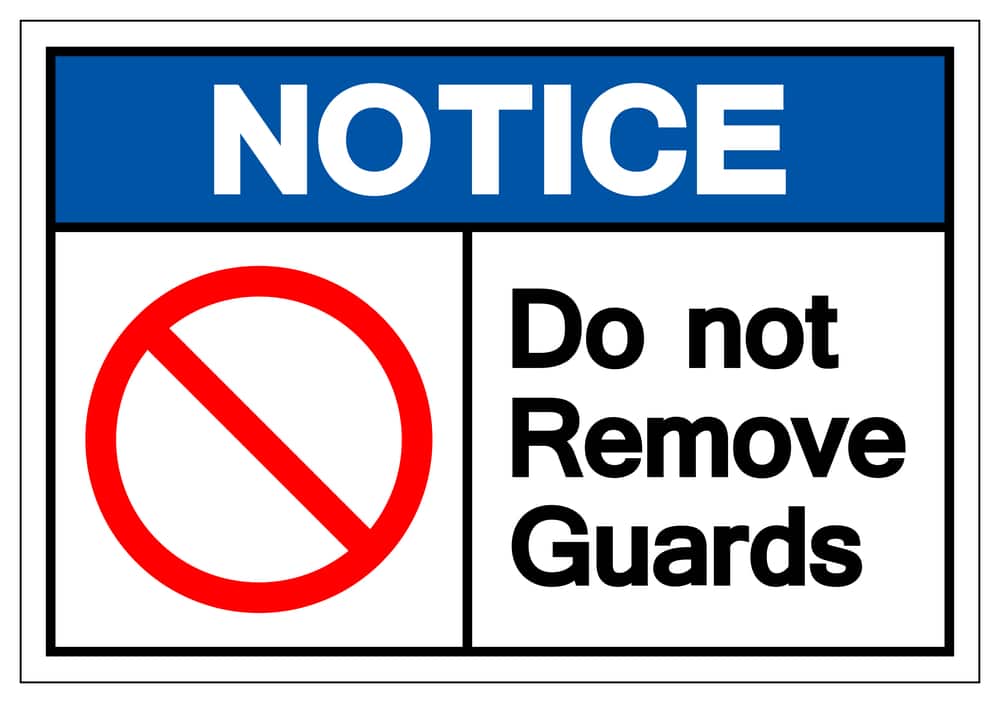
What Are the OSHA Requirements for Machine Guarding?
OSHA requirements for machine guarding come from the general principle that workers must be protected against injury caused by machine moving parts to more specific regulations regarding safeguards against particular machine hazards created by machine operation.
Specific standards exist for general industry, construction, maritime, and agriculture.
A machine must have at least one appropriate guard against any function or part that creates hazards for the operator or bystanders. This is often a point of operation guard, but other times, safeguards work by stopping revolving barrels or drums from turning while operators access them.
Revolving components such as fans also pose a hazard and require a protective cowling. Heavy machinery may move about during operation and thus pose a threat; it must be anchored.
Operators should never use a machine without proper safeguarding.
OSHA Requirements and Best Practices for Guard Design
OSHA also requires that a guard not operate in such a way as to create a new hazard. An unfinished surface, jagged edge, or shear point is unacceptable on a machine guard. The edges of the guards should be bent over to eliminate sharp edges.
Guards can be installed after a machine has been built, but it’s better to integrate safety features into the design from the beginning.
Locating oil reservoirs far from any moving machine parts, with a line leading to where the oil is needed, ensures safe lubrication.
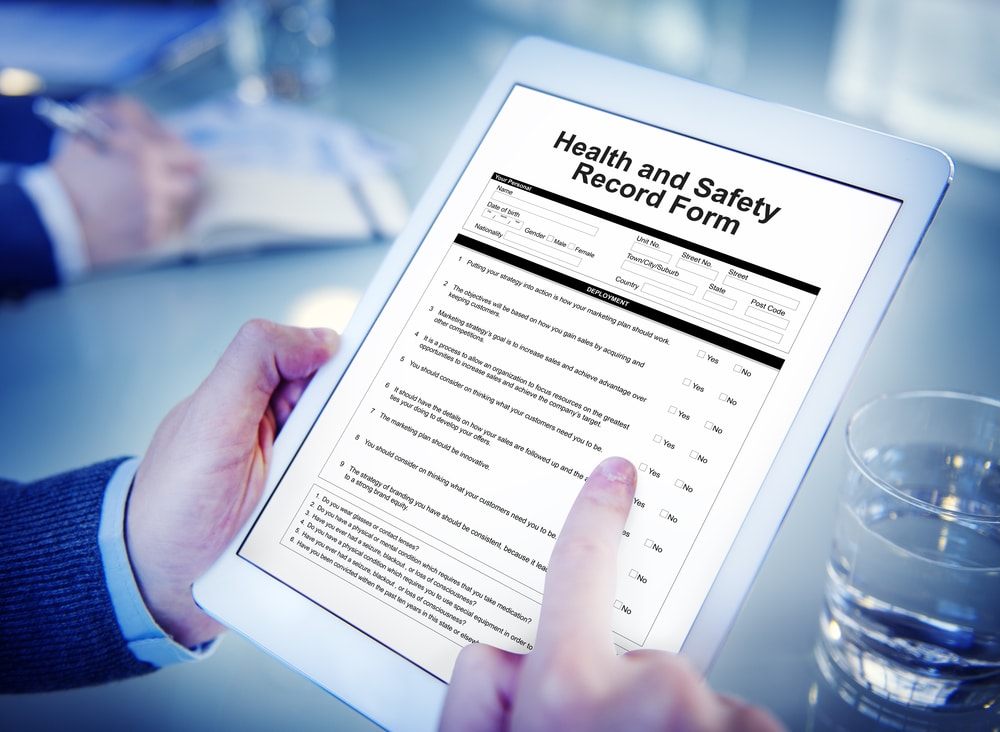
How Do You Inspect Machine Guards?
Personnel inspecting guards should always use a checklist.
All safeguards must meet basic OSHA requirements, such as the lubrication point being situated at a safe distance from any moving machine part, guards preventing contact between any part of the operator’s body and the machinery, and preventing objects from falling into the machine.
The checklist should further cover protection at the point of operation, power transmission, and other moving parts, protection against other hazards such as noise and electricity, and the availability of appropriate personal protective equipment.
All inspection checklists should include a section evaluating the protection and proper training of the maintenance crew.
Machine Guards Are Usually Located at the Point of Operation
The most common way that any worker in a facility will come close to moving components is at the place of interacting with the machine as an operator. Consequently, guards are typically located here.
However, other parts of the machine may also present hazardous mechanical motions, and additional measures are also necessary. Awareness barriers do not constitute physical barriers between personnel and machinery, but they alert workers that they are entering a potential danger area.
A distance of seven feet or more between walkways, platforms, and other areas where employees move about and rotate parts is considered protection by isolation.
The various types of safeguards where workers operate machinery can be divided into multiple classes, each requiring specific maintenance procedures.
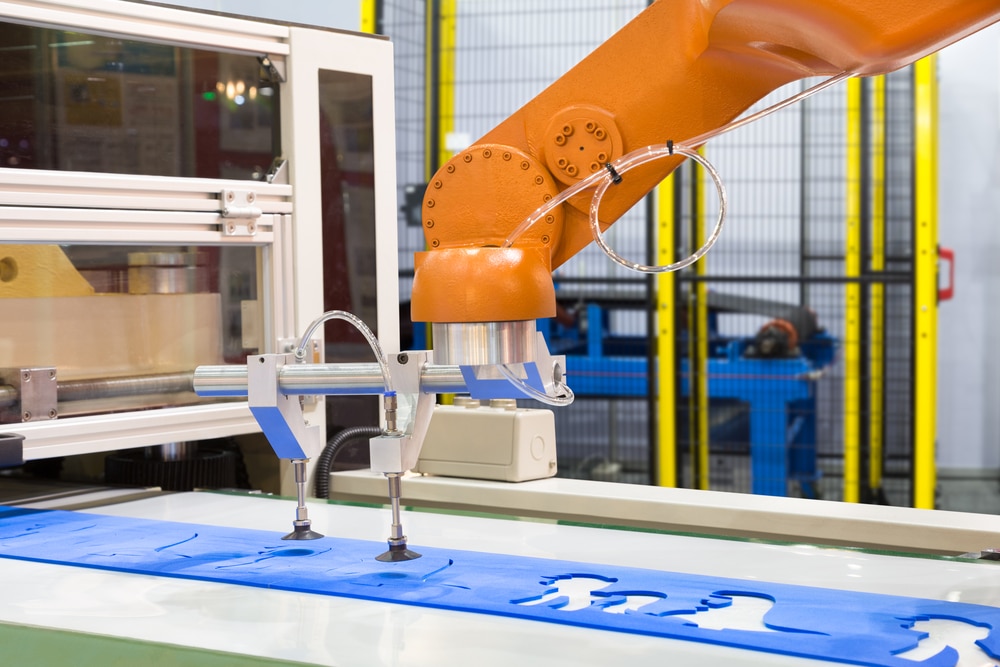
What Are 5 Types of Machine Safeguards?
Machine safeguards protect workers in different ways.
Awareness Barriers
An awareness barrier does not prevent access to a dangerous area. Nevertheless, it helps to protect operators by alerting them to the fact that they are entering a hazardous area. However, continual exposure to such a warning can make workers jaded about the alert.
This type of guard must always be backed up by one of the others listed below.
Sensors
These potentially stop a machine’s operation when a sensor indicates that a body part is in the way of the machine’s function. Machine guard sensors are a special type of guard, and there is much information on this specialized safety feature.
Fixed Guards
Fixed guards are part of the machine during normal operation. They act as barriers between operators’ bodies and moving parts. They also prevent falling objects from entering the machinery and potentially becoming dangerous projectiles.
These fixed guards should only be removed by trained and authorized maintenance personnel when access to the machine is required or if the guard itself needs to be repaired or replaced. They must be made of durable material.
A cracked guard is in imminent danger of failing, and one dented by heavy impacts will also have developed weak points.
Some transparent plastic guards turn yellow with age; however, as the plastic in question is PET-G, this is not a safety concern.
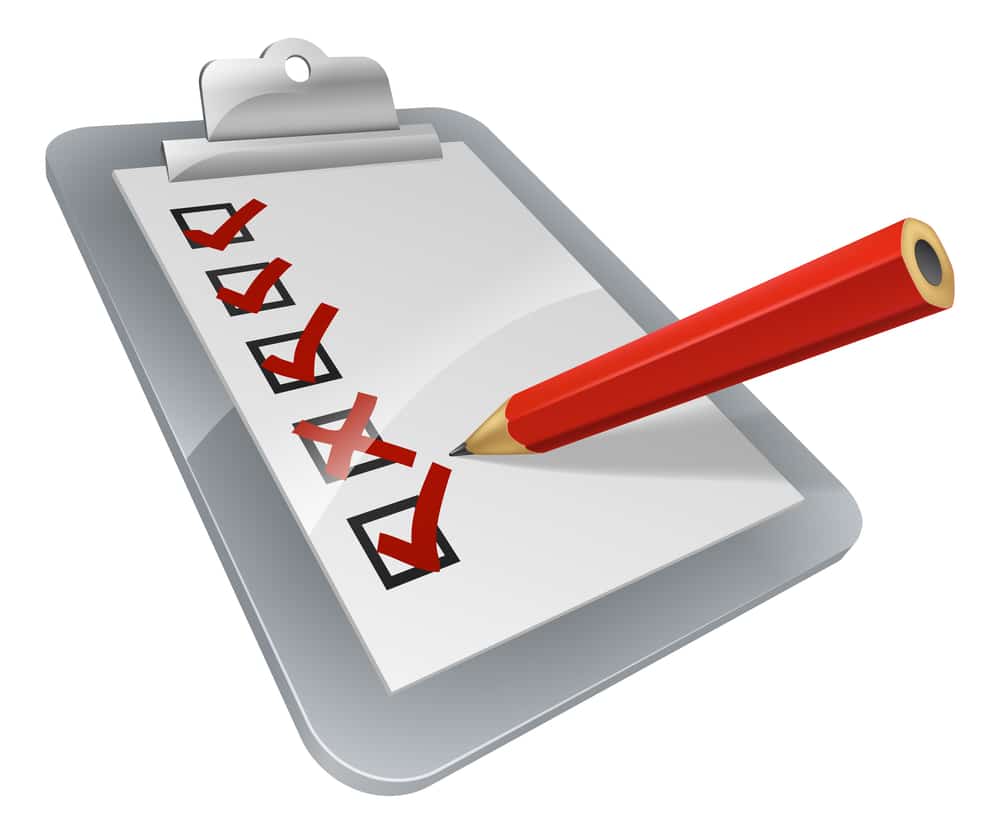
Adjustable Guards
Adjustable guards allow the machine operator to feed in items of varying sizes for operations such as cutting by careful adjustment of the guard’s position.
Self-Adjusting Guards
Self-adjusting guards are a subcategory of adjustable guards, with the advantage of returning to a closed position once the work stock has been processed.
Interlocked Guards
Interlocked guards are a broad category, comprising any means of cutting power to the machine when a physical guard is opened or removed. Hazardous motions are eliminated because they can no longer transmit energy.
Machine controls requiring the operator to use both hands can be considered a type of interlocked guard.
The Role of Personal Protective Equipment in Machine Guarding
Even if a safety device offers the operator and other workers complete protection from any hazards posed by operating the machine, employers should still provide personal protective equipment as backup protection.
Workers must not wear loose-fitting clothing that could catch in machinery.
Maintenance and Inspection of Machine Guards: Wrapping Up
Far from hindrances to workplace productivity, appropriate safeguards enhance efficiency by preventing harm to skilled employees. Guards should be installed at any place where machines could create hazards.
Daily inspection of guards, proper training in the use of machines, and regular guard maintenance all help to keep workers safe and productive.