Common Material Handling Hazards and How to Avoid Them
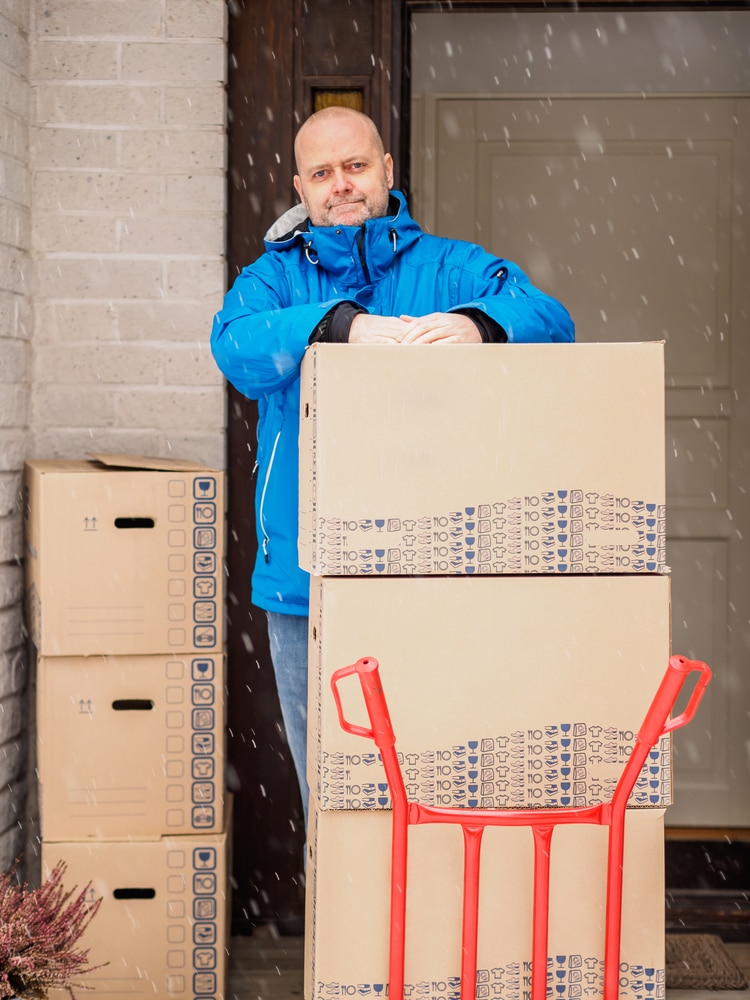
Many types of potentially hazardous materials and equipment are used on various job sites, including labs, loading docks, and warehouses. Ensuring workplace safety while handling them is imperative.
Accidents involving material handling, heavy machinery, and other equipment don’t have to be common occurrences. Most workplace injuries can be avoided when the proper precautions are taken. Understanding how to minimize any potential risk when handling materials is the first step.
Through rigorous training and application, the workplace can be a safe space. Safety is always the priority, and workers should be encouraged to speak with supervisors when they have questions about procedures. We offer a full training course on materials handling safety that can help your overall safety program as well.
What Are the Risks of Poor Material Handling?
Most material handling injuries stem from moving materials manually without the correct technique, tools, or other means of protection.
Some materials may be flammable or toxic, and direct contact can cause injury to workers. The use of mechanical equipment and personal protective equipment can minimize risks and protect workers from harm.
Another common type of safety concern when handling material involves using heavy machinery. These machines require properly trained operators to work them to keep other employees safe. Should a worker operate a machine they are not trained on, they’ll be putting their own life and their coworkers’ lives at risk.
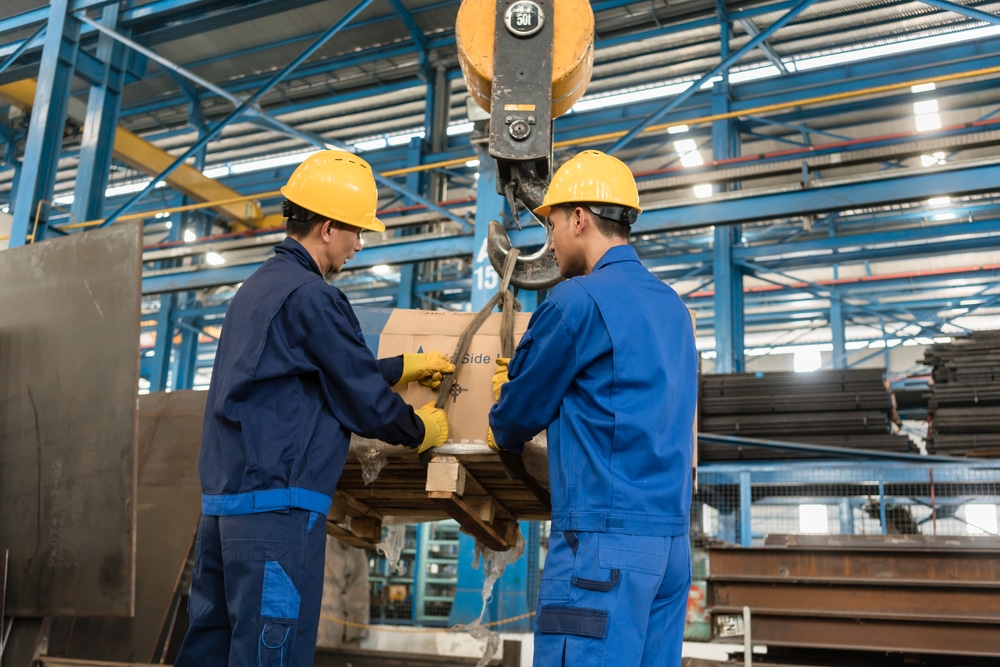
What Are Some of the Most Common Material Handling Hazards?
According to data gathered by the National Safety Council, up to a quarter of all permanently disabling injuries in the workplace are due to poor materials handling.
Materials handling injuries range from simple cuts and scrapes to back injuries, paralysis, and fatalities. Employees must exercise caution when loading equipment like cranes and forklifts, when using power tools, and when handling potentially hazardous materials.
The demands of daily operations do not negate the responsibility to follow the systems in place to protect workers. This includes training in both manual material handling and mechanical material handling processes. An employee who steps up to operate machinery or attempt material handling without protective equipment or training risks injuring themselves or others.
Another material handling hazard occurs when employees don’t use the proper Personal Protective Equipment (PPE) while doing their jobs. Moving materials to and fro creates a lot of room for injury, including nails in wood pallets, getting your foot crushed by a pallet jack wheel, having items fall from a hand dolly, etc. That’s why training your materials handling employees to use the proper PPE while working is so important.
Here are some common factors that can affect material handling.
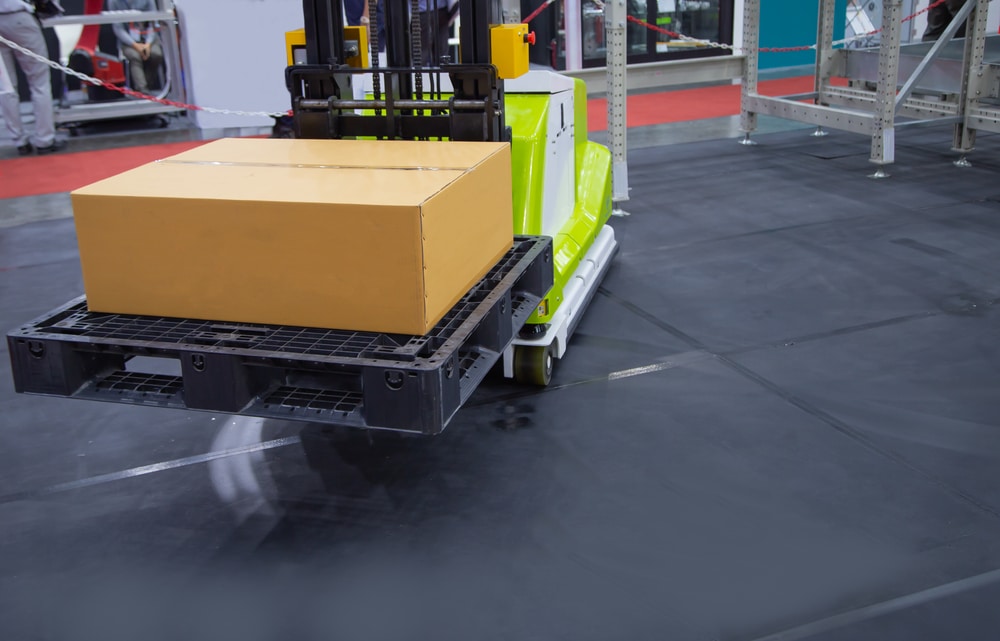
Environment
Poor lighting and tight spaces can cause injury when moving materials like pallets and boxes. When pathways are obstructed, tasks become difficult if not impossible, without intervention.
Not only does this waste time, it puts workers at risk. If a path is obstructed or visibility is impaired, do not attempt to cross it.
Other environmental hazards in the workplace involve the failure of structural elements, such as brakes, controls, and other mechanical handling systems. While these are in place to prevent injury, their failure can result in danger.
Heavy Loads
Falling loads are dangerous, causing workers to sustain critical injuries. Mechanical material handling equipment, such as cranes, can lead to devastating injuries if the load is too heavy or unbalanced. The load can tip and fall over, tumbling down and crushing workers below.
The contents of the load, if packed in boxes, may spill out as well. If those materials are hazardous or toxic, additional harm can come to employees on the job.
A load may also come down if the equipment fails or is not properly rigged and restrained. Proper anchoring prevents the equipment from giving way under the weight of the load on the pallets. Incorrectly cutting ties can also cause helpful tools to fail and allow materials to topple over.
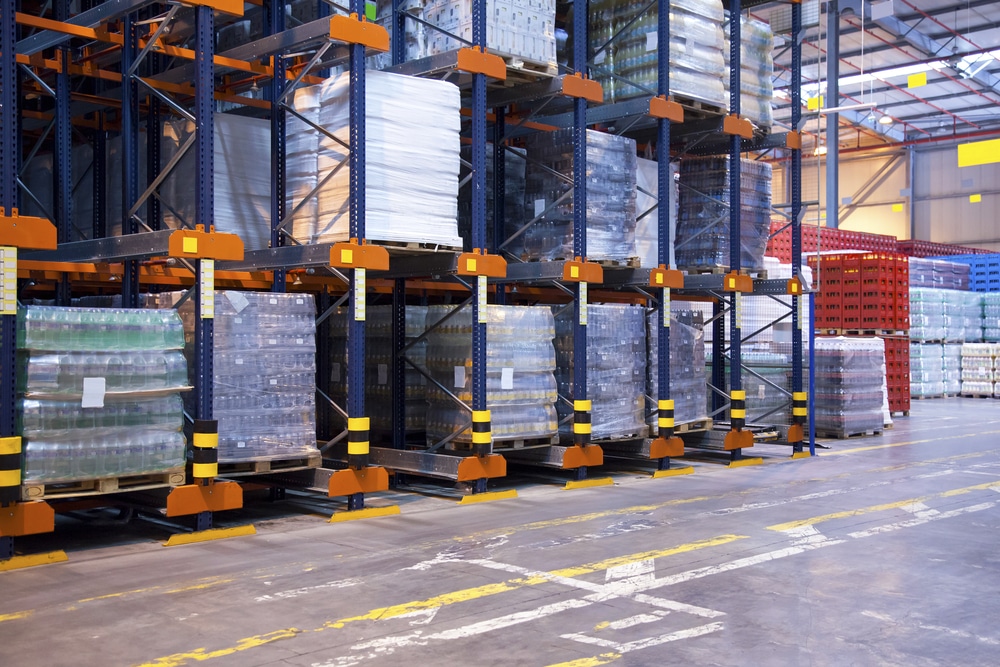
Failure Of Lifting Equipment
Lifting equipment is meant to assist workers, but without proper training, it can quickly become a hindrance and a hazard for material handling procedures. Such equipment – like a pallet jack or forklift – requires specific training so that the controls are used properly.
If lifting equipment fails, it can result in injury. This could manifest as back pain from improper manual lifting technique, or – if the failure causes the crane or forklift to buckle – falling materials could hurt nearby workers and cause lasting injury.
Other material handling equipment like dollies, hand trucks, and cradle dollies all present their own dangers if not used properly. The key here is to train your employees on whatever equipment your facility is using. Also, every time you introduce a new type of material handling tool, your staff is immediately trained on its safe use BEFORE they start using it.
Motion-Related Incidents
Material handling in motion is a hazard as well. Objects in motion can strike any tools or material in the way, causing spillage or toppling.
Another safety concern with motion-related incidents is the possibility of hands, feet, or bodies getting crushed, caught, or pinched by machinery. This can lead to serious or fatal harm in the workplace.
These incidents occur more frequently when workers are rushing and moving at a fast pace without proper organization. When the pacing is unbalanced, pallets and boxes can pile up. This process can escalate and lead employees to work in an unsafe manner in an attempt to stay on target.
While working fast may seem like a good idea at the time, it often opens the door for trouble and danger.
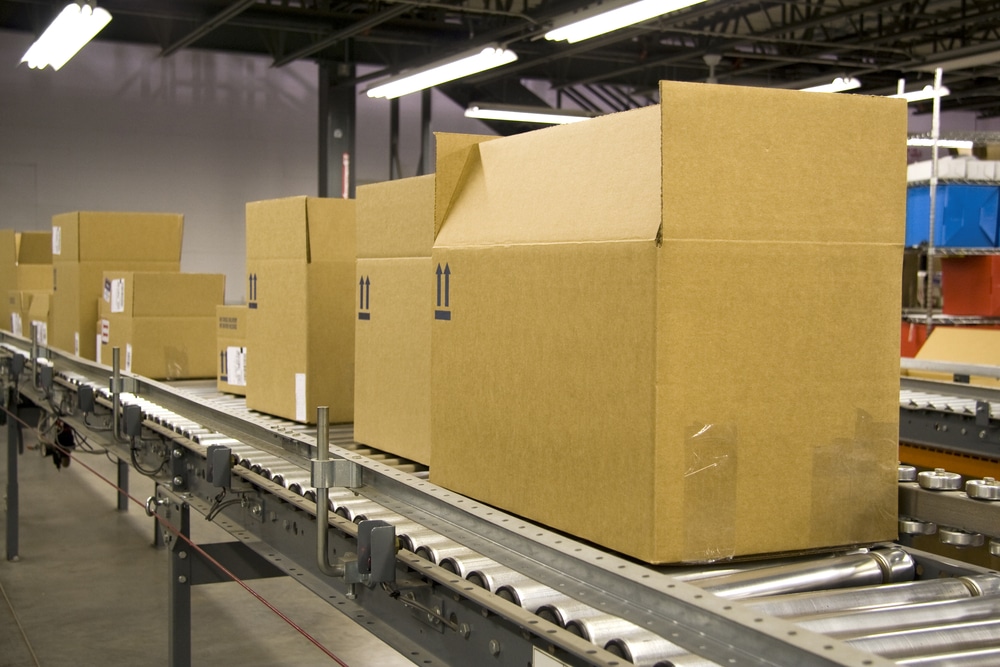
Why Materials Handling Equipment Is Important
When dealing with mechanical material handling and racking systems, safety is key. From lifting to loading, the choices of one worker affect the rest of the staff, and unsafe choices can be catastrophic.
Injuries can result from improper material handling, leading to falls, spills, and other damage. Hazardous material, like toxic or flammable substances, can come into contact with the skin and lead to lasting consequences.
Many accidents involving material handling can be avoided through proper precautions.
What Is the OSHA Standard on Material Handling & Storing?
OSHA has a specific Standard for materials handling, and that is 1910.176. The Occupational Safety and Health Administration enforces specific guidelines to help prevent injury and encourage workplace safety. By adhering to protocol and following regulations, workers can go about their day in safety without fear of danger.
To avoid material handling injuries while lifting, follow the designated procedure and go slow. Never rush, and always consult manuals when unsure of the protocol.
Ensure that only licensed staff operates machinery and that machines are not over-encumbered. Do not exceed weight limits, and make sure to anchor machinery that could tip to avoid damage properly.
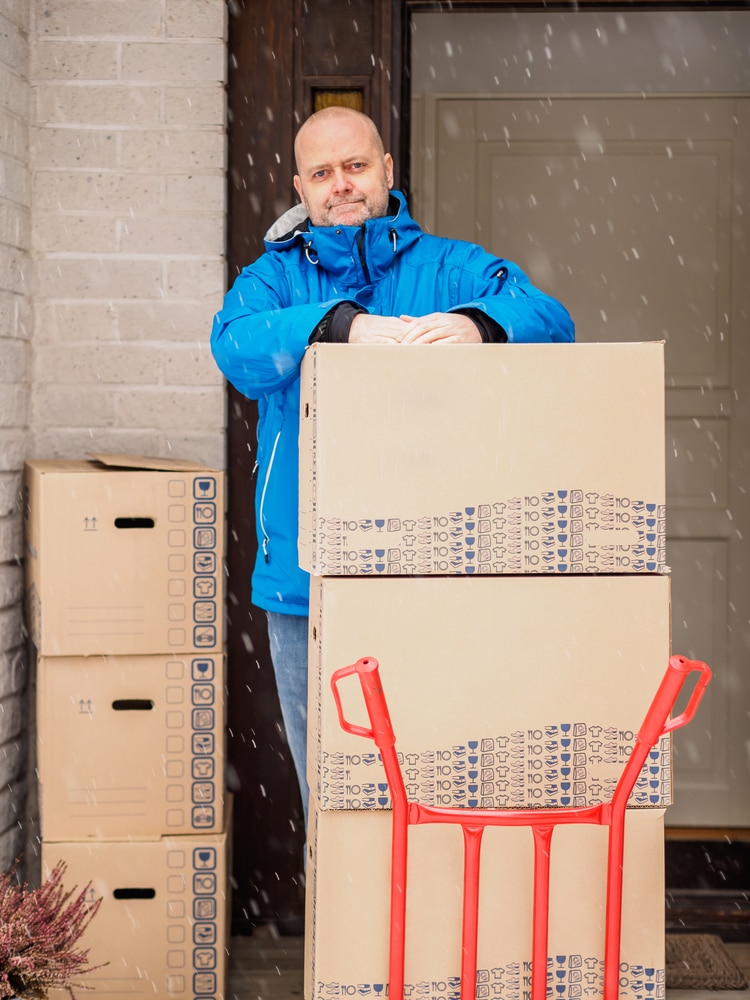
Final Thoughts
Material handling safety requires the active participation of every employee on site. Only through cooperation and understanding can a workplace thrive, ensuring that every person has a safe environment to work in. Hopefully, you have learned something about materials handling hazards in this write-up.
Occupational health and safety must always be a priority. Each individual’s contributions move the workplace closer to minimizing danger while on the clock.