Arc Flash Hazard Analysis – [Updated for 2023]
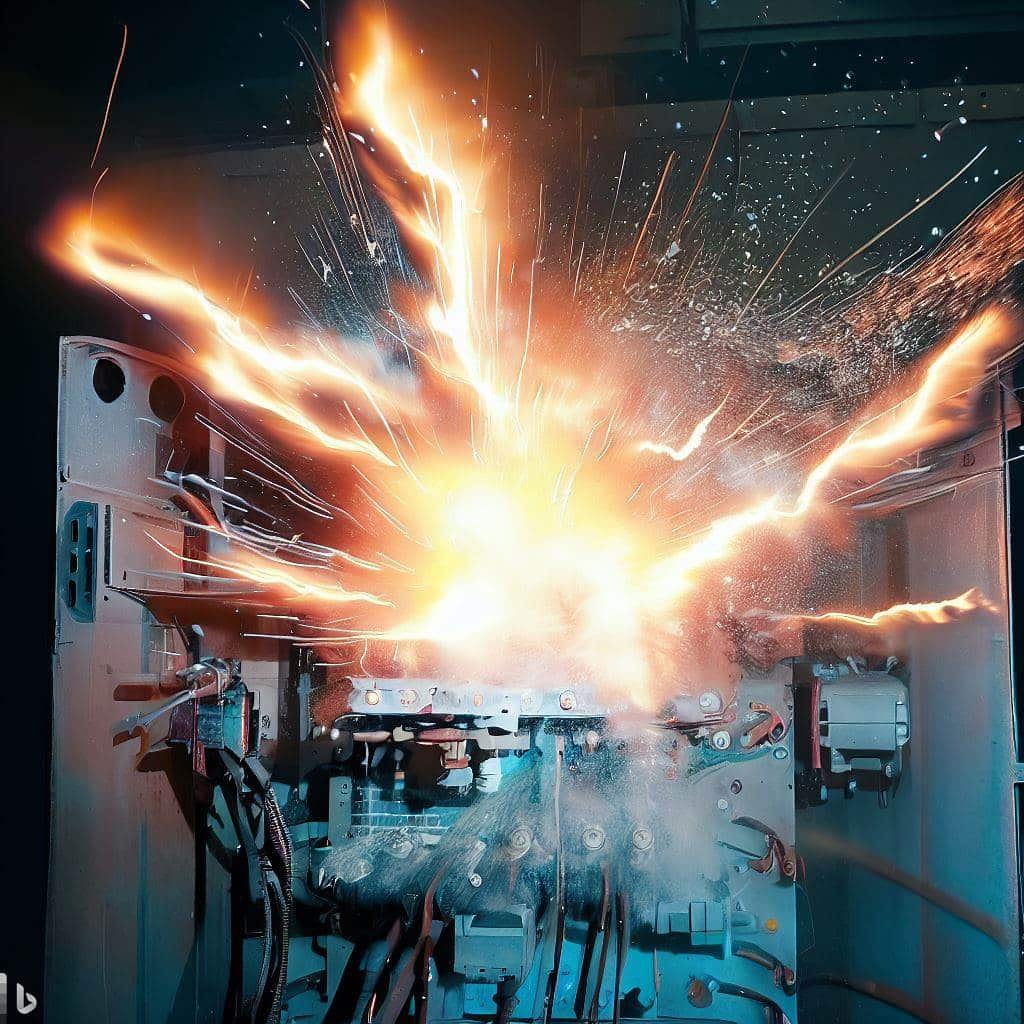
Arc flashes are among the most dangerous workplace hazards of all. It’s estimated that there are around 30,000 of these incidents per year, thousands of which result in severe burns and hundreds of which result in death.
It’s imperative to analyze arc flash hazards to protect your workers routinely. Likewise, proper training materials must be in place so that workers understand the dangers associated with these hazards.
This guide will outline the rationale behind arc flash hazard analysis and detail who should perform it and when it should be performed.
We’ll cover how the analysis should be conducted and establish best practices for a short circuit coordination study in line with IEEE (Institute of Electrical and Electronics Engineers) guidelines. We’ll also review the NFPA 70E guidelines from the National Fire Protection Association and show how they can be implemented to minimize workplace hazards. We also have employee training on arc flashes if you want to go through a more formal training program with your team.
What is an Arc Flash?
Arc flashes occur when a conductive item like a wire connects with an earthed electrical system. The result is an explosion that can result in serious injury or death.
When the connection is made, it can produce heat at around 35,000 F. This is hot enough to vaporize metal and dispel plasma throughout the nearby environment. The force produced by the flash is also powerful enough to throw heavy objects across the room at extremely high speeds, so PPE has to be highly specialized.
What’s the difference between an arc flash and an arc blast? The “flash” is the initial outpouring of light and heat from the electrical connection. This includes high volumes of ultraviolet light and temperatures hotter than the sun’s surface. Teaching your employees how to perform basic first aid following an arc flash accident is critical to the overall well-being of the injured employee.
The “blast” is what often follows the flash. It’s a supersonic wave that spreads outwards, shattering nearby objects and propelling them at high speeds. As they often occur in conjunction, delivering hazard training to workers on both incidents at once is common. However, they refer to different parts of the reaction.
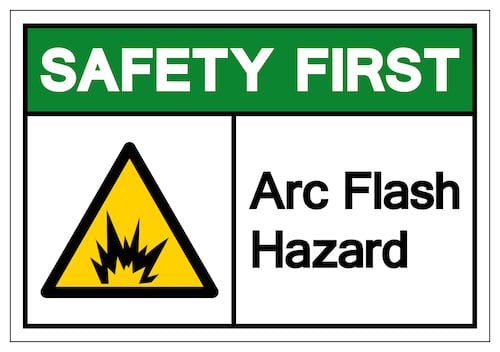
The most common types of injury associated with these accidents are:
- External burns. The incredibly high temperatures associated with the arc flash can burn and even melt skin. The energy expelled by the electrical explosion can also superheat and melt personal items, especially those made of metal, fusing them to the skin and causing terrible injuries.
- Internal burns. The heat is so intense that it can burn through the skin and cause direct burns to internal organs. The nose, throat, and lungs are especially vulnerable to burns.
- Eye injuries (including blindness). These explosions emit a huge volume of ultraviolet light. This is enough to cause blindness and even to melt the eyeballs. Significant vision impairment is a frequent consequence of exposure.
- Lung damage. The plasma and vaporized metal expelled during the explosion can enter the lungs and cause massive internal injuries.
- Hearing loss. When an arc blast occurs alongside a flash, the supersonic explosion is deafening to those nearby and can cause permanent hearing loss or significant hearing impairment.
- Impact injuries. Large items can be thrown across the room by the explosion and cause impact injuries to bystanders. For this reason, traditional electrical personal protective equipment (PPE) is considered insufficient to protect anyone working within the arc flash boundary.
- Cuts & lost limbs. Molten shards of metal can easily cut through most PPE. Large shards of metal can cause significant injuries and even sever limbs.
- Death. Around 400 people die due to arc flash hazards in the US every year, with around 2,000 injuries significant enough to require hospitalization.
While these workplace incidents are relatively rare, they’re so damaging that they’re a central part of electrical safety training for all responsible employers and electrical professionals. Knowing how to respond to an arc flash incident is critical for your staff and for your company.
Key takeaway: Analysis is essential to prevent serious injuries to workers.
What are Arc Flash Hazards?
An arc flash hazard is any possible cause of arc flash energy being released. Contact with live electrical areas is perhaps the riskiest but damaged circuit parts can also present a significant hazard.
There’s also a common misconception that high-voltage appliances are more dangerous than low-voltage. Low-voltage appliances may actually pose a more significant risk – the severity of the incident is more often determined by:
- The flow of current
- How the arc is confined
- The gaps between connective electrical parts
- Conductors’ chemical makeup
- The distance between the flash and the affected workers
What causes this type of release of incident energy? The most frequent causes of arc flashes are:
- Faulty electrical equipment. Malfunctioning electrical equipment can easily lead to metal parts coming into contact with a grounded system. This can trigger an arc flash.
- Dropped or mishandled items. Workers must be provided with full occupational safety training on the risks of dropping or fumbling equipment near live circuits. Even a small movement toward live equipment can cause a hazard.
- Contact with uninsulated items. All equipment used to work on these systems must be properly insulated. This mitigates the risk of flashes.
- Using the wrong instruments. Workers must always be provided with proper instruments for the job. Substituted or outdated equipment increases the risk of an incident.
- Working on live electrical systems. Power lines and other live systems are among the most dangerous environments for electrical workers. These must be subject to regular arc flash analysis (including before any maintenance work) to protect workers.
- Lack of labeling. Arc flash labels should be used to identify any potential risk areas. This is one of the easiest steps facility and workplace owners can take to ensure staff isn’t exposed to dangerous environments.
- Exposed live parts. If a job requires working temporarily with exposed live elements, an arc flash analysis must be conducted to determine the boundary and correct PPE for workers.
- Poorly trained staff. Anyone working near an arc flash hazard must have proper electrical safety training. Anyone working directly with such hazards should have received safety training as well as professional-level electrical training. Staff should always be able to request updated training if they feel unsure of the causes or risks associated with arc flash hazards.
Key takeaway: Analysis is a central component of developing proper safety protocols (e.g., adequate labeling) to ensure workers understand and treat hazards with respect.
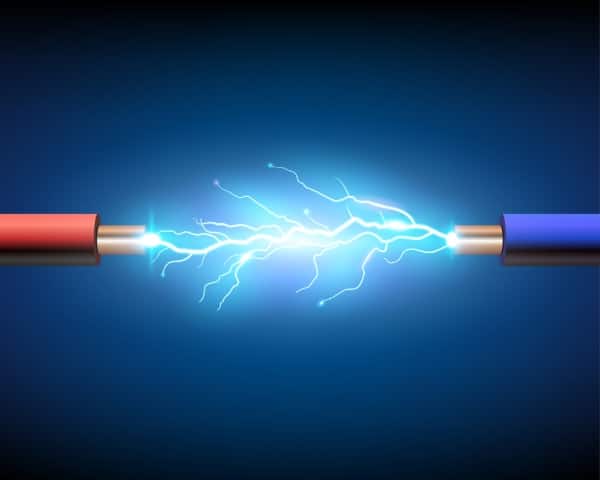
What is an Arc Flash Hazard Analysis?
This type of analysis is a study performed on short circuits within an electrical distribution system. It calculates the potential risks associated with each hazard and provides an overview for workers and supervisors to understand risks.
Its goal is to ensure that anyone working directly next to an arc hazard is properly protected. This often requires much more extensive PPE than typical electrical work – several layers are often suggested to mitigate the risk of burns and cuts from flying debris.
It’s also designed to protect those operating nearby. A boundary is calculated to establish where anyone not working directly in the hazardous area will be “safe” in the event of a flash.
Remember that the flash boundary is different from the blast boundary. Separate analyses will help workers understand the risks associated with a blast.
Key takeaway: Analyses are used to calculate which measures will need to be in place to protect workers and understand the potential severity of a flash incident.
How Do You Perform an Arc Flash Risk Assessment?
An arc flash risk assessment is also known as a short circuit coordination study. It involves:
- Analyzing potential hazards
- Understanding current risks
- Understanding which type of protective device is being used (and/or should be used) to minimize risk
- Determining how close workers can safely get to the hazard
- Determining incident energy – this is typically conducted using specialized software
- Creating the arc flash boundary – this is the distance at which workers and equipment may be considered “safe” from the flash
Note that the boundary is a calculation based on the energy released by the flash. An arc blast releases sound energy and can propel objects across a room, which may pose a safety risk even if workers are considered safe from the incident energy directly.
We cover the best practices for a short circuit study below. First, it’s vital to understand a) who can carry out the procedure and b) what tools will be needed to perform it.
Who performs the analysis?
The workplace or facility owner is responsible for performing the analysis once every 5 years. Analyses should also be conducted more frequently if new hazards are introduced or identified.
A trained, licensed electrical engineer should conduct the analysis. The inspector should be thoroughly familiar with the NFPA 70E regulation and IEEE 1584 (the guide for these calculations).
The inspector must also have a strong background in short-circuit studies and how a power system operates. This typically involves experience and education beyond an electrical engineer’s “standard” qualifications, so facility owners should carefully choose a competent professional.
What tools are needed?
Besides access to the workspace and hazard sites, the engineer will need software tools for calculating heat energy density in the immediate vicinity and establishing the boundary. Specialized software programs such as SKM Power Tools are used for these electrical safety calculations, as numerous calculations are often required, and manual calculation leaves an unacceptable risk of human error.
Key takeaway: there can be no room for error in the analysis. It must be performed by an expert with access to all information surrounding the hazards and appropriate software for calculating energy density.
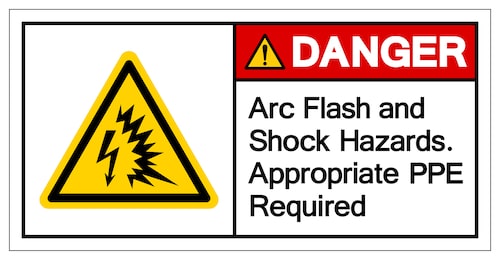
Conducting a Short Circuit Coordination Study: Best Practices
The following steps describe how a qualified person performs an arc flash hazard analysis.
- Data Collection. This step involves system modeling based on whatever information about the arc flash hazard exists, along with potentially refining any previous arc flash study. The IEEE provides forms for this type of data collection to help the engineer build one-line diagrams that summarize current risks.
- Determine Modes of Operation. This involves understanding all types of short-circuit currents that pose a risk. As environmental factors such as the type of protective device being used are more significant than the highest available fault current, voltage alone should not be used as a metric to understand worst-case scenarios for each fault.
- Establish Bolted Fault Current Risks. Bolted faults are especially high-risk, as there is nothing impeding the fault. These should be given priority as they can be responsible for incredibly high incident energy levels in the event of an accident.
- Establish Arc Fault Current Risks. Arc faults are often afforded fewer protective measures than bolted faults but can still produce devastating consequences. Even though the current is much lower in these cases due to impedance, all risks should be measured and understood.
- Establish Characteristics of Protective Devices. Each protective device should be applied according to the associated risk. This may depend on the arc’s intensity and duration. Engineers should consult IEEE 1584 depending on the protective device and the hazard.
- Take Note of System Voltages. The equipment’s bus gaps and arc energies should be recorded. IEEE 1584 includes a table for equipment with voltages as high as 15kV to help engineers understand bus gaps.
- Establish Working Distance. The distance that any worker will likely need to be from the equipment should be understood to measure the risk to the individual. This concerns active workers rather than those standing outside arc flash boundaries – the personal protective equipment a worker will need depends on this calculation.
- Use Software to Determine Incident Energy. It’s typically recommended that engineers measure the incident energy levels of all electrical equipment using specialized software. The calculations are often complex and variable, and while IEEE 1584 provides several generic calculations, electrical safety should be as precise as possible.
- Establish Flash Protection Boundaries. 1.2 calories/cm square is given as the “safe” distance where the arc flash boundary can be drawn. This energy intensity may result in second-degree burns to anyone not wearing adequate personal protective equipment, but those protected by PPE are likely to be safe from the worst injuries associated with flashes. Once again, the energy dispersal calculations in the arc flash study should be software-assisted for accurate results.
Key takeaway: Facility owners must engage a licensed professional who is familiar with NFPA 70E and IEEE 1584 – and who understands this procedure inside-out. Full diligence and understanding of these complex electrical hazards is the best way to ensure workers’ safety.
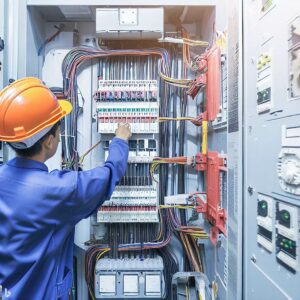
About NFPA 70E & IEEE 1584
NFPA 70E is an industry standard for electrical safety. Produced by the National Fire Protection Association at the request of OSHA. It’s used as the safety standard for many types of electrical work. This includes arc flash hazard studies.
Along with IEEE 1584, it’s established the gold standard for safe electrical practices in arc fault management for many years. IEEE 1584-2002 was a vital resource for electrical engineers conducting these studies – however, it’s recently been superseded by IEEE 1584-2018. All hazard studies should be conducted using the most up-to-date version.
How Often is an Arc Flash Hazard Analysis Required?
According to NFPA 70E, an arc flash analysis must occur once every five years. However, introducing new electrical equipment or identifying new hazards should necessitate an update to the current study.
There’s never a “wrong” time to update an analysis. Workplace and facility owners should be mindful that any new electrical system may require updated calculations re: boundaries and potential hazards.
For training, OSHA regulations state that individuals working with electrical systems must receive updated arc flash training at least once per three-year period. However, given these hazards’ seriousness, annual training is often recommended.
Key takeaway: the responsibility lies with the workplace owner to arrange a study once every five years. They should also be mindful to update the study if new hazards are introduced.
What is a Flash Hazard Analysis Used to Determine?
Anything from live powerlines to exposed electrical conductors presents a flash risk. The study isn’t focused on establishing whether there is a risk – that’s a given. Rather, the study focuses on establishing a safe boundary for nearby workers, installing devices to mitigate the flash’s worst effects, and determining which PPE a worker will need to offer the best possible protection in a worst-case scenario.
Worst-case incidents are when the flash is incredibly powerful and vaporizing temperatures are reached. Very few PPE systems can offer adequate protection to someone in the immediate vicinity when an event like this occurs. Multiple layers add additional protection and are often recommended.
However, almost any PPE will struggle to withstand a powerful arc flash or blast. Perhaps the more important purpose of these studies is to implement protective devices within electrical systems to prevent workers from being directly exposed to the flash.
The best method, as always, is prevention – measures can be implemented to minimize the risk of connections. However, other devices may seek to absorb the worst of the flash and even melt as a type of sacrificial protection for the exposed workers. Exploring which devices are used to mitigate flashes is a key study component.
Key takeaway: arc-rated PPE is mandatory for workers. However, every containment measure should be put in place to minimize the chance of a hazard development and to contain it where possible, as PPE will be limited in a worst-case scenario.
Workplace Procedures to Minimize Arc Flash Risk
Here are three quick rules to ensure minimal risk in your workplace.
- Ensure all staff members are properly trained. Regular re-training helps staff remain aware of the dangers of arc hazards. Staff working directly with electrical equipment should be offered re-training whenever requested.
- Put up signs. Adequate signage is essential to reduce the risk of untrained workers trying to fix what they perceive as a “minor electrical issue” that could actually cause a devastating reaction.
- Keep studies up-to-date. Contact a licensed electrical engineer to update the arc flash study whenever new risks are introduced to your workplace.
Summary
Protecting your employees against an arc flash incident is more than just “required,” These hazards are the most lethal and explosive electrical incidents of all. They have the ability to change the lives of your workers and their families with the potential of death.
Arc flash hazard analysis is a complex, in-depth study necessary to protect workers from devastating consequences. If your workplace is due a study update or your electrical training is outdated, it’s time to fix that.
FAQs:
The first step is to identify the hazards. The severity of the risk is then assessed. Finally, protective measures (both PPE and protective devices) are recommended.
Once every five years or whenever new environmental risks are introduced.
The workplace or facility owner must contact a qualified engineer or electrician to perform a study.