Why Energy Isolation Is a Pillar of Industrial Safety

Energy isolation is a fundamental component of workplace safety in industrial facilities and any work area where equipment servicing occurs during normal operations.
Developing and following a rigid energy isolation process protects the safety of all employees and safeguards any equipment in the work zone.
Keep reading to learn all about the importance of energy isolation and how to implement these essential procedures in your workplace.
We also have a LOTO training video if you want to train your staff on lockout tagout requirements.
Why Is Energy Isolation Important?
The purpose of energy isolation and lockout tagout procedures is to ensure any hazardous energy sources are isolated and under control before employees start a service or maintenance job on any machinery in the workplace.
Electrical equipment must be de-energized and equipped with lockout devices to protect workers’ health and safety. Isolating residual or stored energy also lessens the chances of overloading electrical circuits, releasing uncontrolled energy into the workplace, and damaging machines and equipment.
Finally, energy isolation helps conserve energy and protect any sensitive components or parts from surge-related overheating. Keeping your employee LOTO training up to date is an OSHA requirement and a safety issue for your employees.
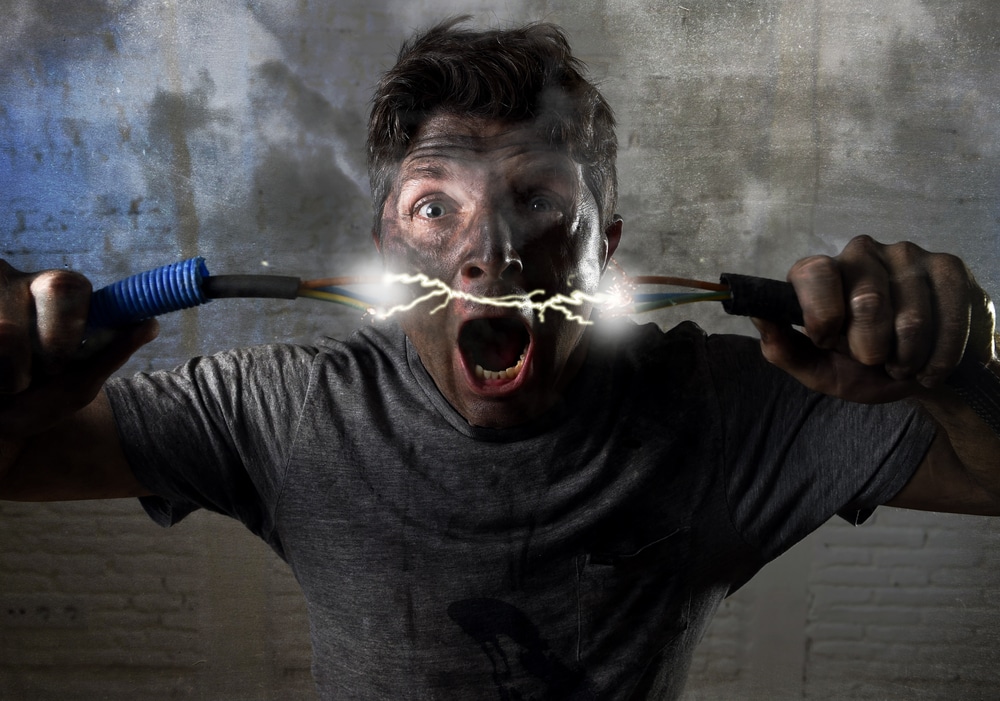
5 Lock Out/Tag Out Steps for Isolating Potentially Hazardous Energy
Authorized personnel must follow a strict energy isolation procedure before working on electrical equipment. Any residual or stored energy within the equipment can cause grievous bodily harm if not restrained by locks and/or a physical barrier.
No unauthorized employee should be in the vicinity of any equipment that is currently being serviced – especially if that equipment is still connected to its energy source.
Here are five steps that outline a general process for isolating equipment from its energy sources.
1. Identify All Sources of Residual or Stored Energy
The qualified employee in charge of the isolation process must identify all hazardous energy sources before proceeding. Each energy source has its own method of being isolated. Training must encompass all the ways to control each type of power source within the work area.
Potential sources of power include:
- Electrical
- Mechanical
- Chemical
- Kinetic
- Hydraulic
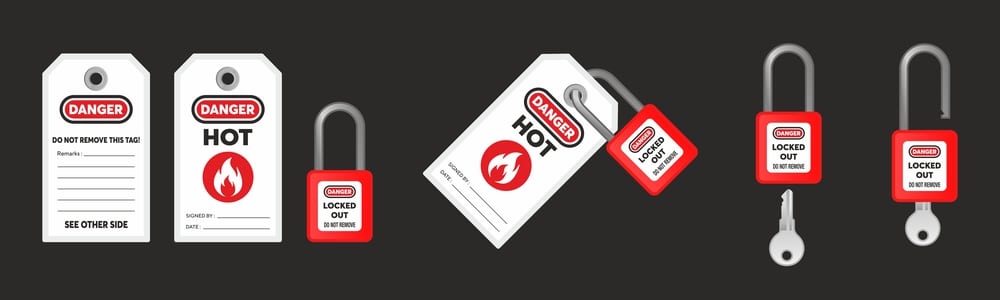
2. Power Down the Machinery
Every piece of equipment about to be maintained, serviced, or relocated must be powered down before being disconnected from its power source.
The person in charge of the lockdown and servicing should inform all nearby employees of the work that’s about to commence.
Any affected employee in the work zone should withdraw to a designated safe distance from the equipment before the isolation procedure begins.
3. Isolate the Equipment From Its Energy Sources
Next, the equipment must be isolated from any energy source that powers it. Common shutdown methods include shutting off the breaker, closing a valve, or unplugging the machine.
Isolation devices prevent the release or transmission of energy from de-energized equipment. Valves are the most common energy-isolating device, followed by breakers, switches, and restraining devices. These devices can be manipulated to prevent power from flowing to or from a machine.
Note that selector switches, control circuit devices, and push buttons should not be considered effective means of control on their own or as substitutes for a lock or tagout device.
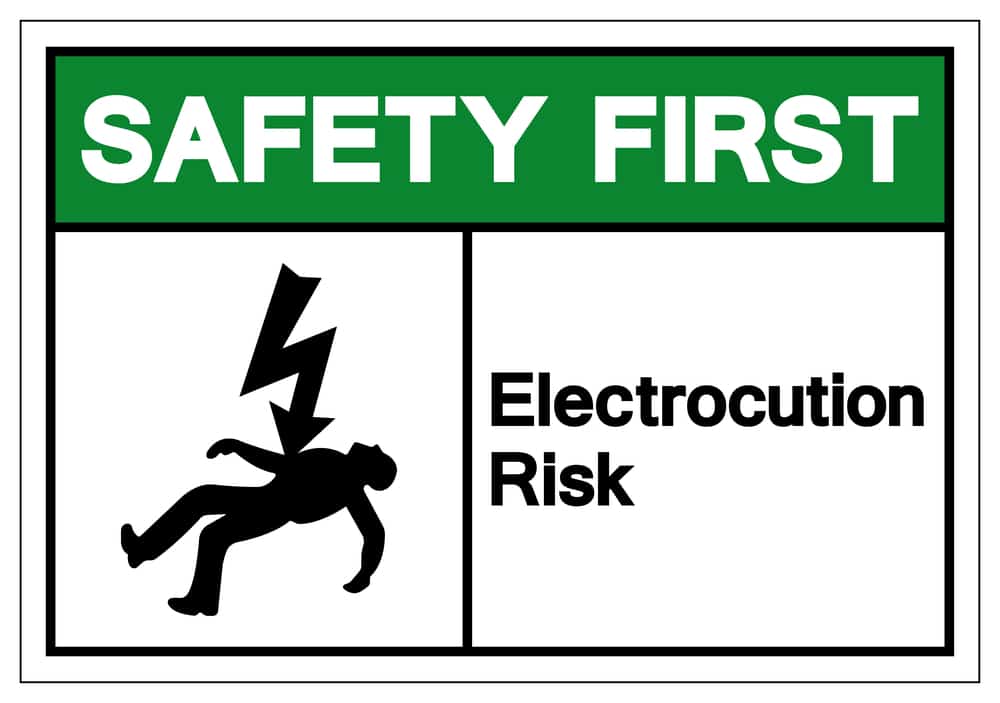
4. Lockout/Tagout the Isolating Device
Once the energy isolation device has been activated, a lock must be applied to keep it in place. If the device cannot be locked, a tagout device must be used instead.
Tags also refer to identification cards that are attached to machines to signify that they are fully de-energized and safe to work on. These tags carry important information about the given piece of machinery as well as the name of the person who performed the lockout procedure.
If multiple shifts work on the same equipment, the previous shift’s tagout devices or locks must remain in place until the next team has put their own devices in place. Premature removal of these devices may result in serious injury to personnel or damage to the equipment or work zone.
There are situations in which temporary removal of locks and tags may be necessary. These include testing and repositioning the equipment. Control is paramount during such procedures, and the equipment should be locked and de-energized as soon as possible.
5. Check the Stored Energy and Verify the Isolation
Industrial employees understand the importance of double-checking their work – even if they’re certain every step of the process has been carried out.
The qualified person performing the lockout procedures must verify that the energy-isolating device is in place and that all potential hazardous power sources are under control.
Even if the machine has been disconnected from its power source, any stored or residual power within it can still present a danger to the employee in charge of servicing the equipment.
Only when that person can safely assure their coworkers that the energy isolating device is locked and functioning as expected can any servicing or maintenance take place.
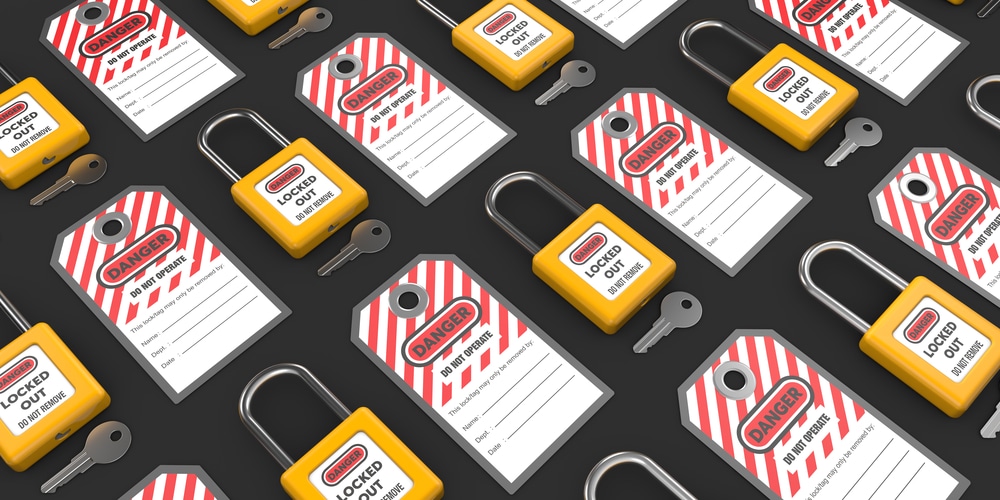
Common Types of Hazardous Energy Sources
The following types of power are frequently used to fuel machines and other equipment that need to be locked and tagged out before being serviced.
Kinetic
Kinetic energy is mechanical in nature and is created by moving parts such as fan blades and gears. Authorized personnel must ensure any rotating parts are locked and fitted with a tagout device before working on this type of equipment.
A qualified person should conduct testing by attempting to operate the locked equipment before proceeding with maintenance.
Potential
Potential energy is stored energy that may be tapped at any time work needs to be performed. Hydraulic and pneumatic systems under pressure are two common examples of potential energy sources.
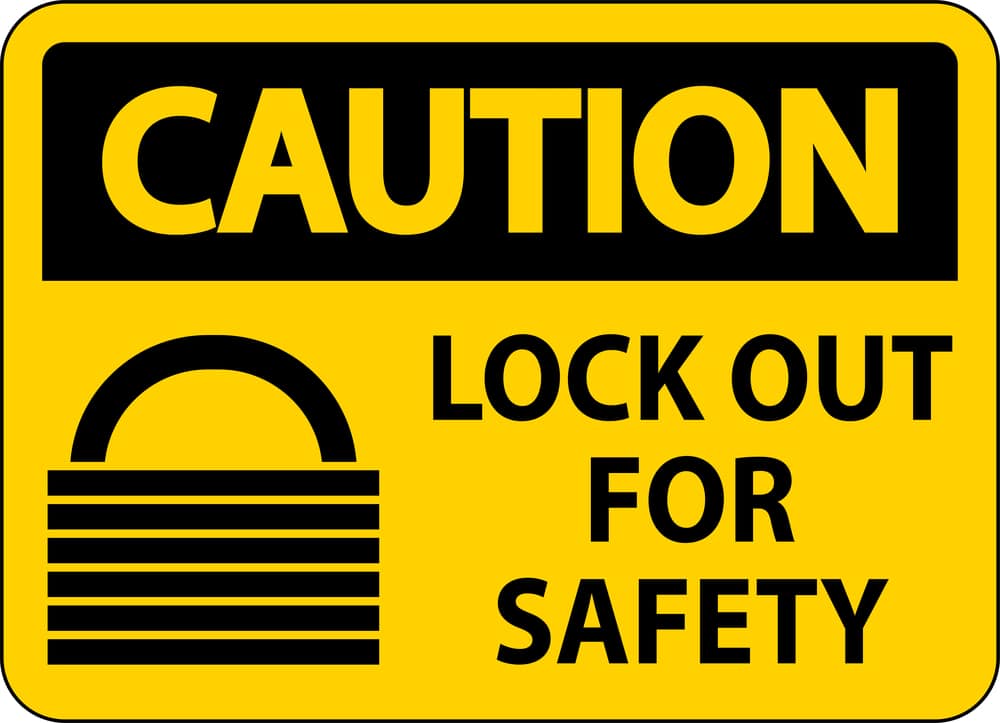
Electricity
Electrical power sources present several serious hazards, including short-circuiting, fires, burns, and arc flash. Be sure electrical equipment is no longer connected to its power source before commencing work or maintenance.
Hydraulic
Hydraulic energy involves moving and pressurizing liquids like water and oil in order to create energy. It is typically controlled by means of a mechanical isolating device and bleed valves.
When Should Hazardous Energy Be Isolated?
An energy-isolating device must be applied before any authorized employee performs maintenance work on the job site.
Any energized equipment or components under pressure must be powered down and subjected to isolation procedures before being serviced to prevent the unintentional transmission or release of hazardous energy.
Other procedures that may require machines to be locked include hot work, confined space entry, relocation, and line opening.
Who Is Authorized to Perform Lockout Tagout Procedures?
Understanding authorized vs. affected employees is a vital component of responsible energy isolation.
An authorized employee is a qualified person who has undergone rigorous training on all hazardous energy sources within the workspace. This employee is responsible for servicing machines in the workplace and ensuring that other employees keep out of the area.
Authorized employees must apply lockout tagout devices before starting work or performing maintenance on a machine.
The term “affected employees” applies to everyone else within the work zone – that is, those who are not qualified or trained in servicing equipment.
Unauthorized personnel should be informed of any potential sources of hazardous energy within the work environment, and they must keep clear during LOTO procedures and while servicing is taking place.

Energy Isolation and Lock Out Tag Out: Final Thoughts
Industrial employees face a lot of pressure to do their jobs as swiftly and efficiently as possible. The longer it takes to service a machine, the more downtime the workplace experiences – which many employers identify as a loss of potential revenue.
The fact is that the risks inherent in disregarding proper isolation procedures far outweigh any costs associated with following those procedures. Consequences can range from injuries and damaged equipment to widespread damages to your facility and even death.
Assure workers that you value their well-being by implementing a strict system for energy isolation and ensuring all authorized employees follow those guidelines to the letter.
FAQ
What are the five steps of energy isolation?
The five key steps for isolating machines from their power sources are:
- Identify all power sources
- Turn off or power down the machines to be serviced
- Isolate the equipment from its power source
- Apply lockout or tagout devices
- Check your work and verify that the power source has been isolated
What are the strategies for energy isolation?
Being thorough and methodical throughout the isolation process is critical to ensure no steps are missed. Cutting corners or rushing the job can easily result in costly errors.
The lockout/tagout process is the number one strategy for isolating hazardous power sources and verifying that equipment has been fully de-energized before commencing any servicing procedures or relocating the equipment.
Isolation procedures and machine maintenance should only be conducted by authorized employees who have received rigorous training and understand all potential hazards associated with the equipment.
What are the hazards of energy isolation?
Isolating power sources can be dangerous if the procedures aren’t followed correctly.
For instance, if the power source isn’t properly disconnected or the isolating device isn’t properly locked or tagged, maintenance personnel may mistakenly believe the machine is safe to work on. This can result in serious injury, particularly if the machine is energized or becomes re-energized due to a power surge during maintenance.