How Often Does OSHA Require Lockout Tagout Training?
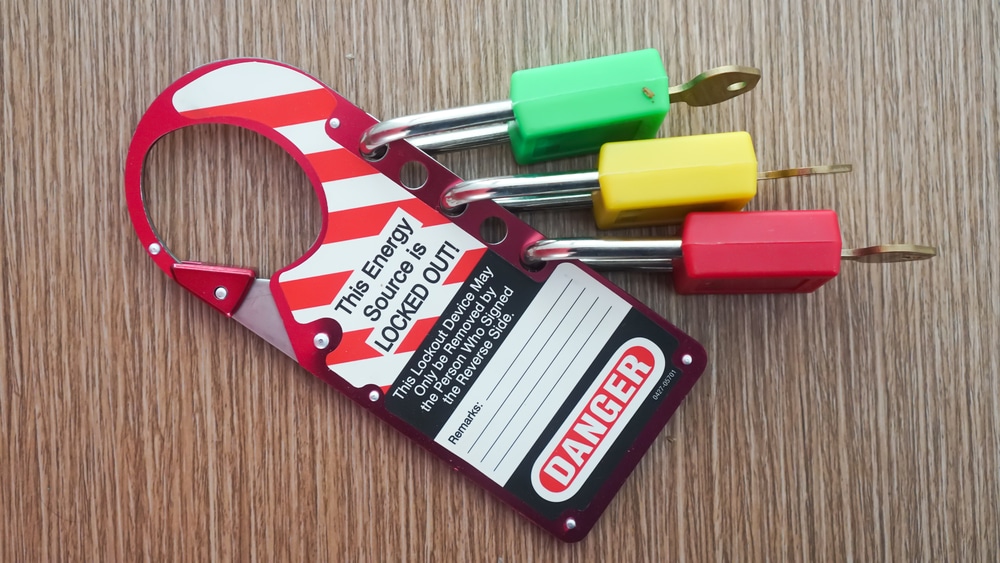
Lockout or tagout is a key energy control procedure for ensuring the safety of equipment servicing personnel. Periodic inspection of your energy control program and retraining of authorized employees is important to provide safe conditions around hazardous energy sources.
Read on to learn more about improving your overall energy control program! Also, we do have an employee training program on lockout tagout.
How Often Do Your Employees Need Lockout Tagout Training?
OSHA does not give a specific timeline. However, training MUST be completed whenever:
- There is a change in an employee job assignment that would require them to understand and apply lockout tagout
- When there is a change in the machines or other equipment within the facility
- Whenever there is a change in process that might present a new hazard within the hazardous energy space
- Whenever employees are fully up to date with their LOTO skills and practices
Finally, best practices would dictate that additional LOTO training be conducted when an injury or a “near miss” injury occurs.
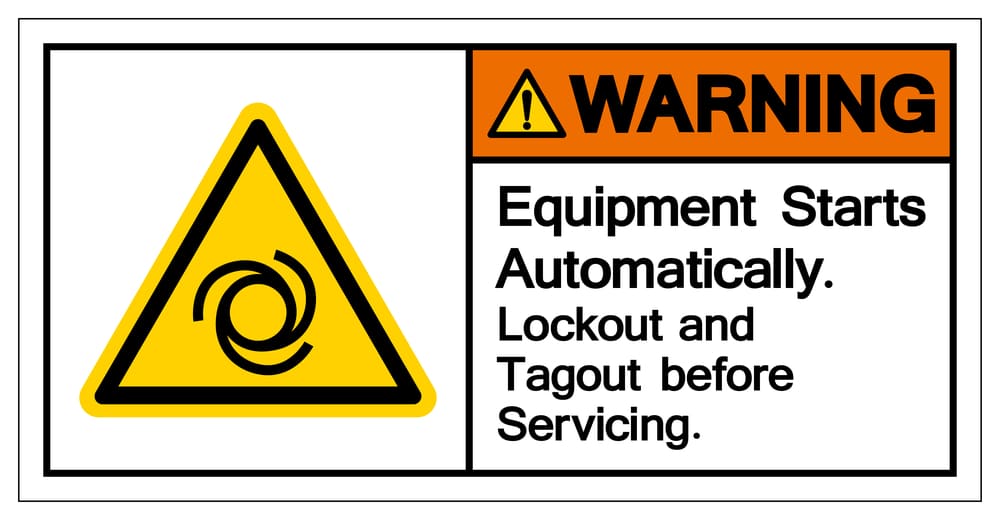
Lockout Tagout Basics
Lockout is when an energy source is physically isolated from a particular system or equipment. Some examples of physical restraint are a padlock on a circuit breaker switch or a blocker bar.
Tagout refers to essentially warning devices affixed to the energy-isolating devices. There is no prohibition on whether a tag, label, or sign must be used. The warning device should be clear, easy to read, and contain the signature of a responsible person.
This signage helps employees understand why a piece of equipment is out of use and prevents them from trying to get it back online.
LOTO energy control procedures were initially developed by OSHA in 1982 and came into legal force in 1989. Energy control procedures and employee training have been shown to save lives, cut insurance costs, and increase productivity.
These OSHA regulations cover all applicable hazardous energy sources. In fact, OSHA establishes strict criteria for exemption from the LOTO energy control program and the use of alternative measures.
Such equipment must meet all of these requirements with no exceptions:
- Have no residual energy.
- Have an easily isolated energy source that can de-energize without risk of unexpected energizing.
- Only require a single lockout point.
- Be serviced by a solely authorized employee.
- Provide no hazard to authorized and affected employees.
- Have a clean record with zero accidents.
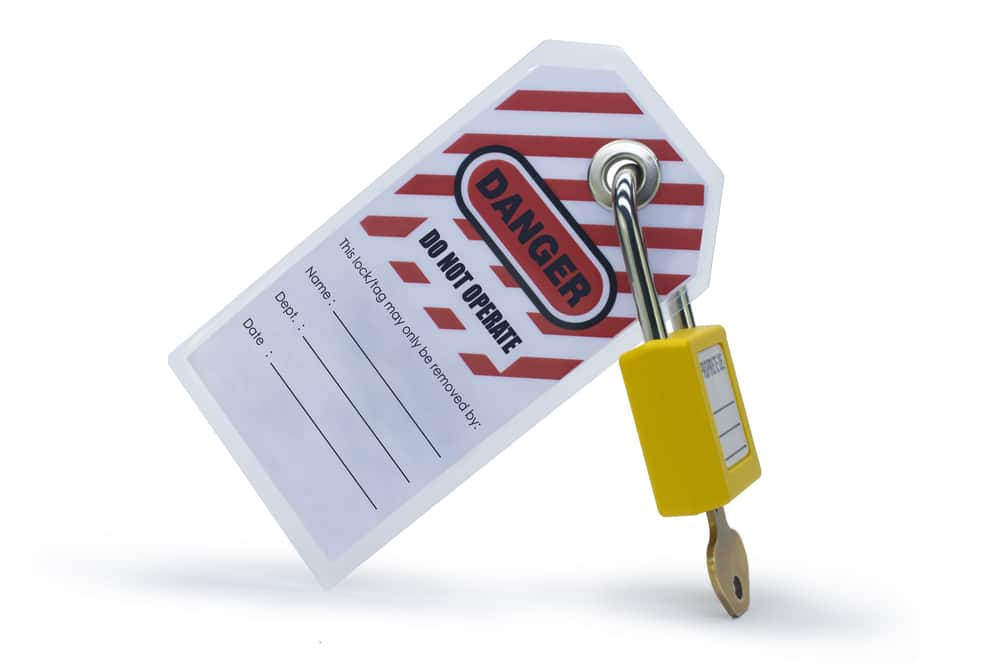
Best Practices for Energy Control Procedures
Some best practices recommended by OSHA include:
- Ensuring proper transfer of LOTO during a shift change or handover of responsibilities to other employees.
- Temporary removal of energy-isolating devices should be done in compliance with OSHA 1910.147 c. How to clear machines, reenergize machines, and restore a zero energy state with no stored energy are all covered in 1910.147 c.
- OSHA standards explicitly forbid using an employee standing guard at an energy isolation device instead of a sign or label.
- Testing should be done to confirm that the system is in a zero energy state with no electricity or pressure still present.
- Standards should ensure that the responsible employee performs the same procedure every time.
Other best practices will depend on the exact needs of your company or industry. Construction and agriculture are two industries where OSHA regulations don’t technically apply, but similar LOTO-type protocols do.
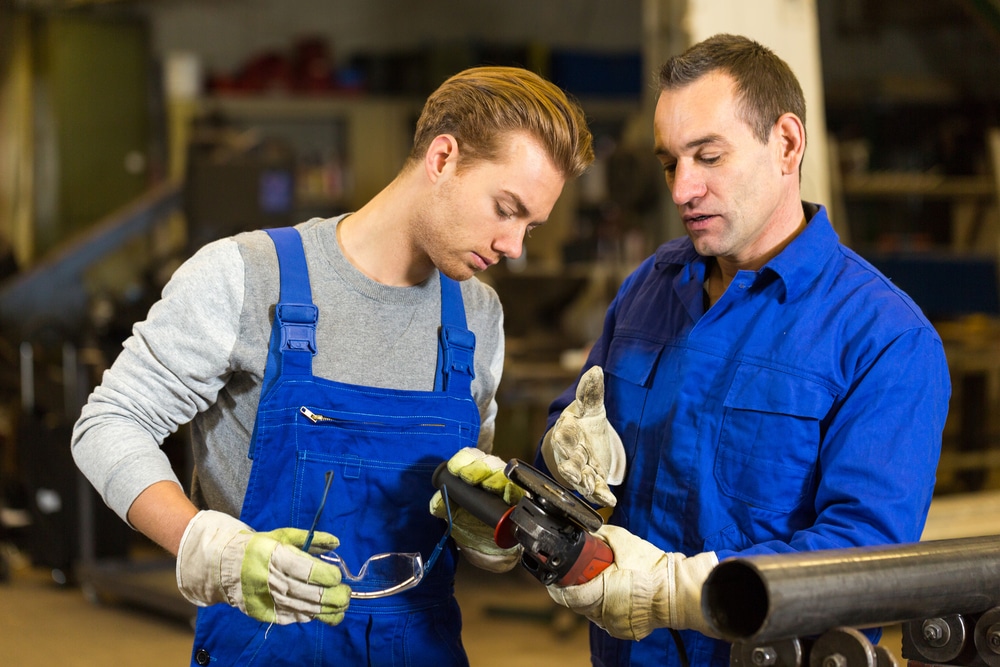
Energy Control Procedure Training
Training on energy control procedures with an authorized person is vital to assuring safe maintenance and servicing of machines or equipment.
Authorized and affected employees should feel competent in the energy control procedure, and other employees should feel safe. Effective training requirements think about real-world work operations and the environmental conditions encountered during maintenance work.
How to Determine Affected Employees
There are a few situations when retraining of authorized employees is required.
- They change job responsibilities, or a procedure being inspected has changed.
- New equipment is added. This is true even if the equipment is the same brand and model number. The best occupational safety practice is to have a separate LOTO checklist for each machine, even if two are identical.
- Affected employees need to be retrained if there is any change in hazardous energy procedure.
- An authorized employee commits a violation, intentional or not.
- The employer has a reason to suspect that an employee needs more information on energy control procedures.
OSHA Training Requirements and FAQs
There are a few definite requirements for employee training on lockout tagout procedures.
- Affected employees must sign off that they fully understand the hazardous energy procedures.
- There must be sufficient written training documentation on energy control procedures.
- Employers must provide training to employees prior to those employees starting maintenance or servicing responsibilities on a machine.
- Employee retraining should occur when any procedures change, a new hazard is introduced, and as needed.
- Any contractors that service your company’s equipment must also be trained in how to perform lockout tagout, and their training requirements should be similar to yours.
- The on-site employer and contractors should share energy control procedures.
- Periodic inspection of the LOTO program often results in changing the procedure being inspected. This will necessitate the retraining of employees.
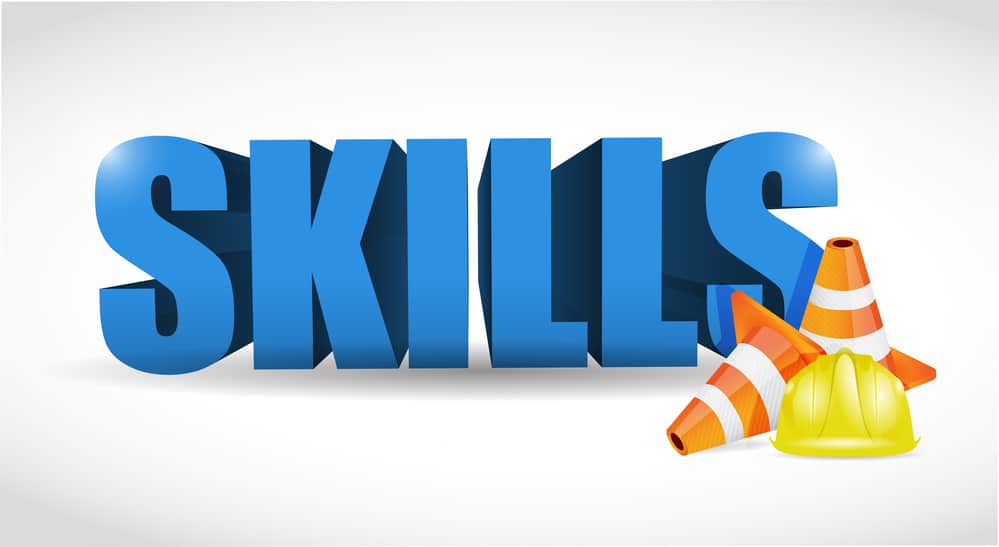
An effective training program consisting of well-documented procedures is the end goal. Employers should ensure every employee receives it. Making LOTO procedure training a staple in your overall safety training program is crucial for both regulatory compliance and employee safety.
To this end, employers can use various official OSHA resources and commercial training plans. Videos, kits, and info sheets can make training more efficient and memorable.
Lockout tagout retraining is required in case of a change in job assignments, a change of procedures, machines, or equipment, or if an employee requires more training.
Does OSHA Require Annual Lockout Tagout Training?
No. OSHA only requires employees to receive lockout or tagout training if there is a change in job assignment or procedures or if an employee has violated procedure.
How Often Do You Need to Do LOTO Training?
Training and retraining are not required to be on a set schedule.
Instead, employees should be trained in LOTO procedures prior to them performing any servicing or maintenance duties and whenever the employer has reason to suspect the employee is deviating from the procedure.
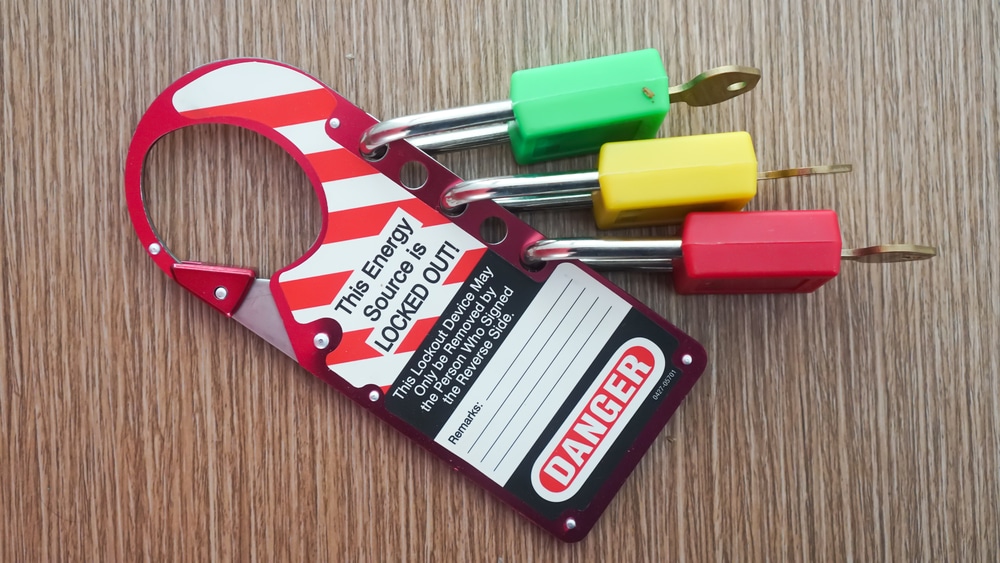
How Long Is LOTO Certification Good For?
LOTO training never expires, but retraining is required anytime a new source of energy or equipment is added or procedures change even slightly.
The lack of an expiration date on LOTO training may provide a false sense of security about energy controls. However, by requiring situational retraining and periodic inspections of the training curriculum, OSHA aims for more frequent retraining to reestablish employee proficiency.
Employees should receive additional retraining from a qualified person if they have deviated from the procedure or the employer has reason to suspect that they have.
How Often Does OSHA Require the Lockout/Tagout Program to Be Inspected?
You must perform an annual inspection of your lockout tagout standard. This inspection must be performed by an authorized employee who does not operate that machine as part of their job duties.
The review should consist of reviewing the written procedures as well as the authorized employee talking to the other employees who use the machine to review the employee’s responsibilities. Often, periodic inspection reveals gaps in an employee’s knowledge, and the affected employee can be retrained on lockout or tagout training.