Recognizing Asbestos-Containing Materials or ACMs
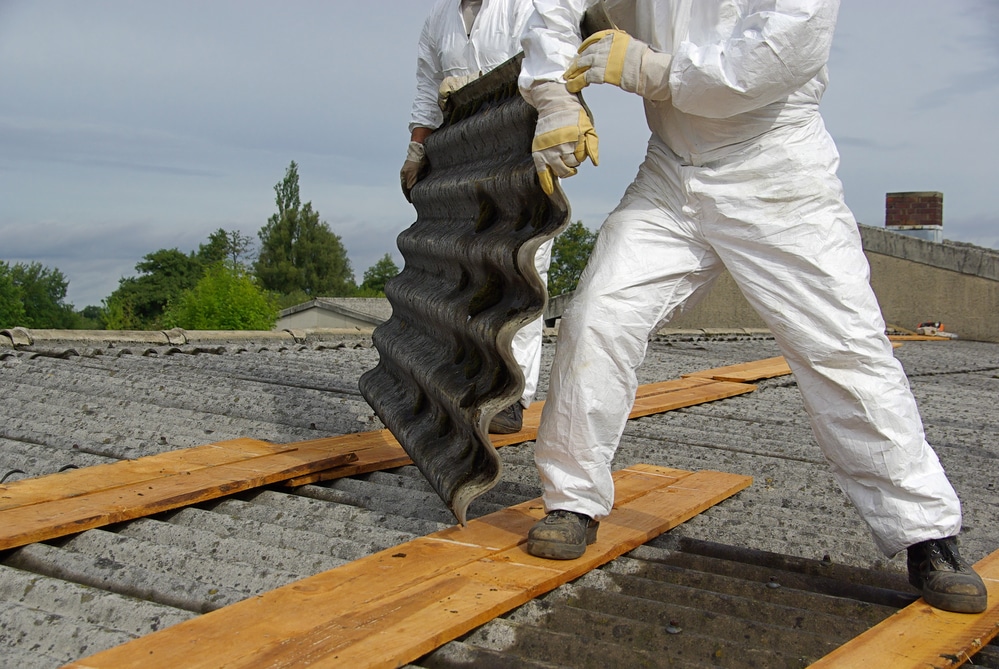
Any industrial hygienist will tell you that identifying and managing asbestos is vitally important. If you’re a building owner, you can almost certainly find asbestos in your building if it was built before 1980, and the mineral is present even in newer buildings.
The numerous laws and regulations around ACMs can be confusing, but it’s well worth the effort to understand your legal and ethical obligations in this area.
Asbestos can truly be a hidden killer, but a little knowledge can help keep you, your customers, and your workers safe. Read on to learn more! Also, if you want to check out our Asbestos Training for Employees, a deeper dive into the topic that can benefit your staff.
What Is Asbestos?
Asbestos refers to a group of soft, fibrous silicate minerals. They can be gray, green, white, blue, red, or yellow. Specific minerals include:
- Chrysotile (white asbestos)
- Amosite
- Crocidolite
- Anthophyllite
These minerals are great electrical and thermal insulators and are highly fire-resistant. Cooking pots containing asbestos fibers were found in a 4,500-year-old archeological site in Finland, and the mineral was well-known to Greeks and Romans.
Asbestos cement products helped build the western US – they were fireproof and affordable. They were also massively popular in Australia and New Zealand.
At the turn of the 20th century, scientists began documenting many early deaths in different mining towns. The UK introduced the first public health regulations around asbestos exposure in the 1930s, though regulation in the US didn’t start until the 1980s.
Today, asbestos-containing materials are banned from the construction of buildings in the EU, UK, and Japan. In the US, use is confined to certain products.
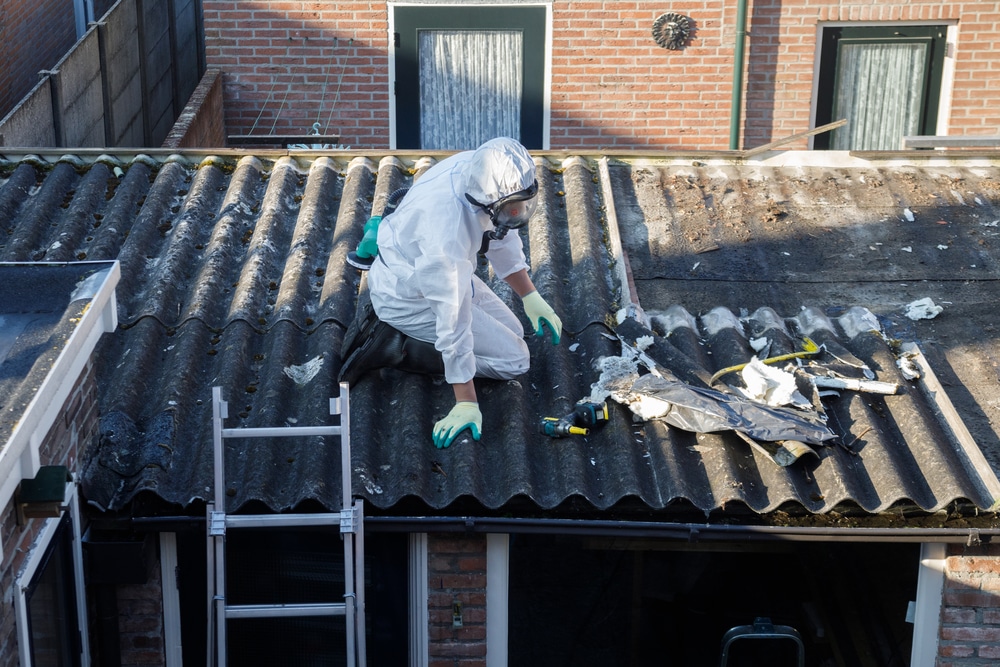
Asbestos Containing Material in Residential Spaces
Because of asbestos’ ability to inhibit fire was commonly used in many building materials, especially before 1980. These include:
- Vermiculite insulation in your attic or walls
- Textured paint, including the kind used to make the “popcorn ceiling” effect
- Vinyl flooring material and floor tile
- Roofing shingles and siding
- Paper or insulation around a wood-burning stove
- The insulation or fireproofing around hot water pipes and furnaces
You may also find this mineral in your car. While most auto manufacturers have stopped using the material in manufacture, many aftermarket brake and transmission parts have been found to contain asbestos. And if you have a vintage or classic car, there may be asbestos-containing material in the original parts.
Residential buildings of four or fewer units are generally not covered under regulations. However, you should still consider inspection and abatement options if you’re concerned about asbestos materials.
Asbestos Fibers in Commercial and Industrial Spaces
While the average homeowner may have asbestos-containing material in their home, the real risk from ACMs is in the industrial or warehouse space. This is mainly because asbestos-containing materials are more likely to be cut or knocked about – the real risk comes from inhaling the fibers.
Asbestos use is common in fireproofing, especially spray-on fireproofing. It may be in fire blankets and fire-resistant gloves and aprons as well. Hidden asbestos is everywhere in many industrial settings.
And, of course, if your facility produces asbestos-containing material, there is also a risk of exposure from that.
An estimated 1.3 million American workers, most in the construction field, are at risk of regular asbestos exposure at work.
Regulations require that you identify asbestos materials in your building before a demolition or renovation project. This inspection needs to be performed by an asbestos professional.
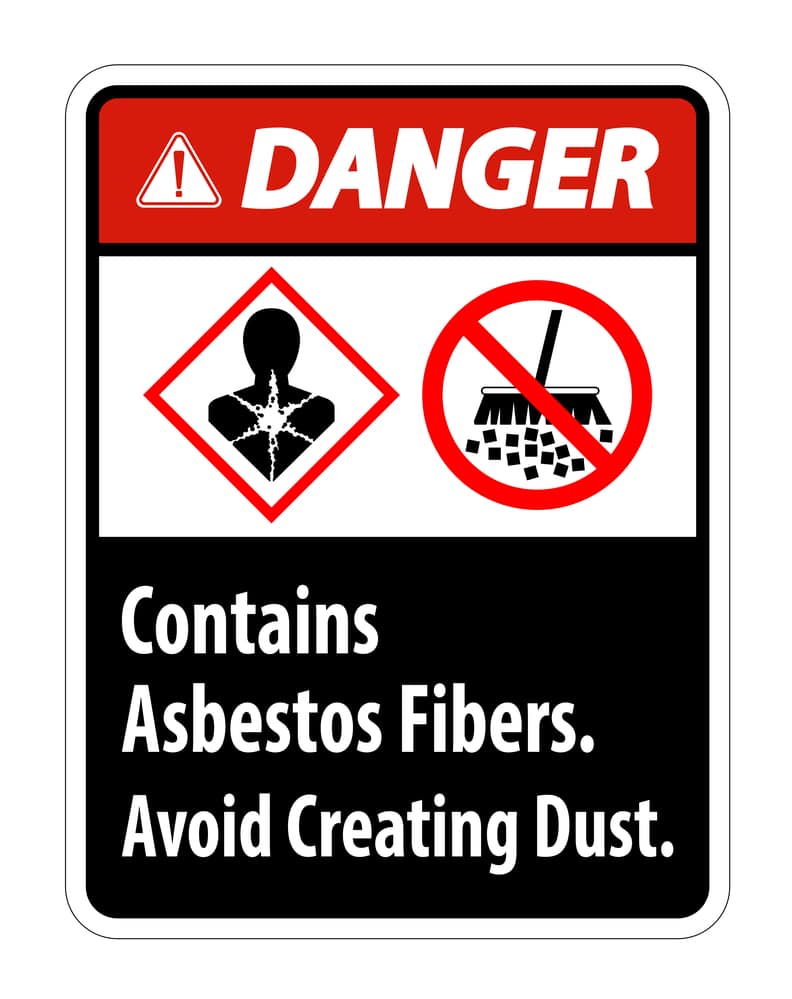
Health Risks of Asbestos Exposure
There is minimal risk to simply being around intact asbestos-containing materials (ACMs). However, free-floating asbestos dust in the air can be quite dangerous.
The fibers are sticky and can become lodged in lung tissue after being inhaled. These fibers then trigger an immune response as the body tries to clear them. It may take years after exposure for asbestos-related diseases to develop.
This immune response can cause fibrosis or excessive scar tissue. When fibrosis occurs after asbestos exposure, it’s called asbestosis. Asbestosis can cause wheezing, coughing, and shortness of breath.
Sometimes, fibers in the lungs will lead to a cancer called mesothelioma. This is a tumor of the pleura or the membrane on the outside of the lungs.
Mesothelioma is an aggressive and highly deadly cancer; at least 80% of cases are caused by asbestos exposure. It typically develops 20-50 years after exposure; the median survival time is 12-21 months.
For those reasons, the Occupational Safety and Health Administration (OSHA) says there is no safe level of exposure to asbestos fibers. It’s a hidden killer that’s well worth identifying.
Who Regulates Asbestos?
The three government agencies overseeing use in the United States are the Environmental Protection Agency (EPA), the National Institute on Occupational Safety and Health (NIOSH), and OSHA.
NIOSH is focused on occupational health science. Their findings often influence OSHA regulatory decisions.
OSHA’s mandate is limited to protecting workers, and their regulations are focused on minimizing asbestos exposure and health risk in the workplace.
The EPA regulates what ACM products are allowed to be sold. The EPA tried to implement a ban on most uses of asbestos in 1989, but the courts overturned much of it in 1991.
An EPA rule from 2019 says that the agency must review and approve any new uses. That means that anything taken off the market prior to the rule would have to have EPA approval before reintroduction.
What Common Material is Most Likely to Contain Asbestos?
Asbestos was used in a wide range of building materials in the US prior to 1980 and is still allowed to be used in some products. Insulation, fireproofing, and flooring are three of the most likely sources, but it was used in a wide variety of products, including:
- Cement products
- Tar and gravel or built-up roofs (these are typically flat roofs on commercial buildings)
- Adhesives like contact cement, joint sealant, or window putty
- Backing for floor tile
- False brick cladding
- Elevator brake pads
- Cement pipes and pipe insulation
- Electrical insulation
Resources online can help you spot suspect material. These resources often include lists of brand names that used asbestos and information about when certain manufacturers stopped using the material.
If you don’t have the product labeling, you’ll need testing to determine if the product actually contains asbestos materials. The safest course of action is to assume something contains asbestos until otherwise proven.
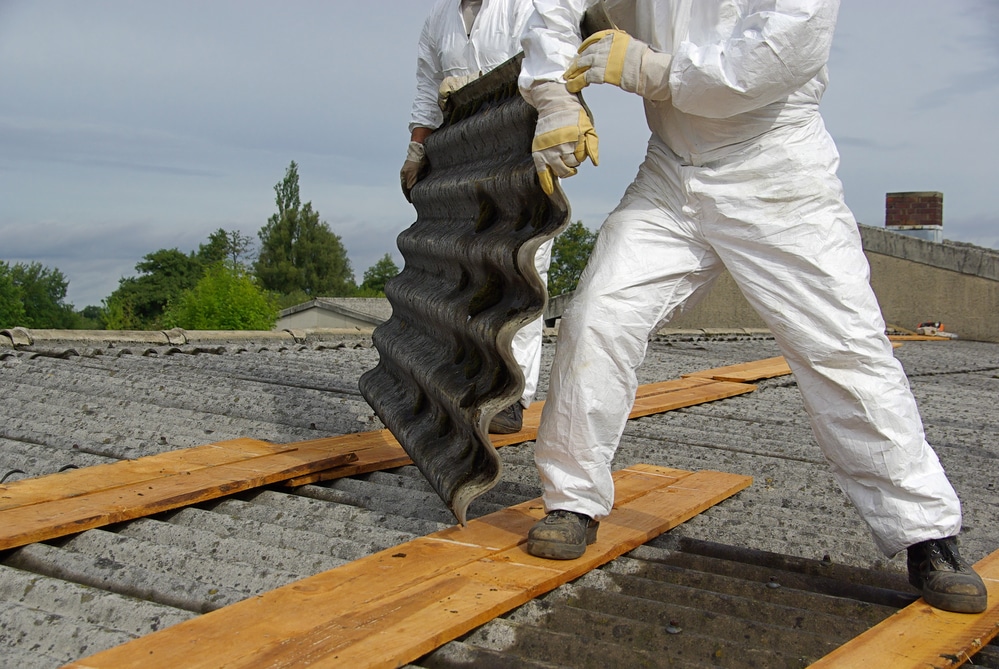
Does ACM Mean Asbestos?
ACM stands for asbestos-containing material. It refers to any materials that contain 1% or more asbestos.
Products containing less than 1% are not required to be labeled as asbestos-containing in the US.
How Do I Identify Asbestos?
You can’t simply tell if something is an asbestos-containing material by visual inspection. Instead:
- For newer materials and building products, check to see if you still have the product labeling and if it lists asbestos.
- For older materials and building products, you can see if the product is on a list of known asbestos-containing products
- You can have the product tested by an asbestos professional (more on that below)
Treat suspect material in your buildings as if it contains asbestos until you have a professional asbestos identification. There are definitely best practices for workers to work around asbestos, and those should always be followed.
What Does PACM Mean?
PACM means “presumed asbestos-containing material.” It has a very specific meaning under OSHA regulations – thermal insulation and surfacing materials in a building built no later than 1980.
Other materials that may contain asbestos are typically referred to as suspect materials. This term is not specifically defined by OSHA, but is commonly used by contractors and asbestos professionals.
So, a building constructed before 1980 may have both PACM and suspect materials. A building constructed in 1981 or after, by definition, cannot have PACM.
How Do You Identify ACM?
A laboratory test or manufacturer’s information is the only way to prove that something contains asbestos definitively. But a few criteria can help you determine what’s worth testing.
Age
How old is the material? In the US, OSHA uses 1980 as a cutoff date for determining potentially asbestos-containing materials (ACMS).
This isn’t a surefire way, as an asbestos building material is still being used today. However, older materials are more likely to contain the mineral.
Usage
Thermal insulation, surfacing materials, and fireproofing are much more likely to be ACMs than other products.
Any product claiming to be fire-resistant or fireproof (even if not fireproofing) is far more likely to be an ACM.
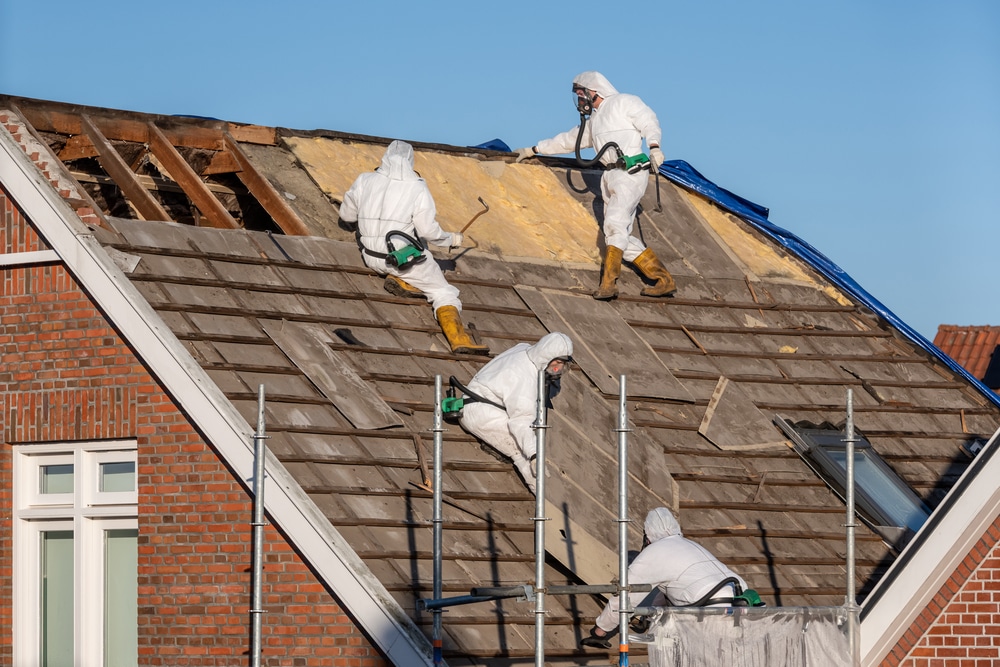
Friable vs. Non-Friable ACM
The main distinction when talking about ACM is friable vs. non-friable. Friable means that something can be crumbled in your fingers, much like soil or a piece of cake.
Because the main risk comes from fibers floating in the air, friable asbestos is a real threat. Non-friable ACMs that are unlikely to shed fibers are far less risky.
Some ACMs may be non-friable until moved or removed. One common example of this is vinyl floor tiles. These may have fibers embedded in the vinyl or have asbestos-lined backing paper. In either case, removing the tiles can break up the asbestos and make it friable.
Visual inspection can help to identify friable PACMs. If something is visibly crumbling, leave it be until you can get the professionals in.
Handling PACM
PACM should be handled exactly the same as actual asbestos-containing material. Depending on the circumstances and likelihood of disturbing material, this can mean:
- Using respiratory protection. This can mean an N95 mask, or preferably a mask or respirator with a P100 filter.
- Containing the area. Depending on the work to be done, you can use drop cloths, mini-enclosures, or HVAC shutdown. Workers may also use coveralls, booties, and gloves.
- Proper cleaning. Any dust or debris from ACM or PACM should be handled with a wet mop or HEPA vacuum.
Consult OSHA or EPA guidance for more information on the proper handling of ACM and PACM.
Asbestos Inspections
Under the EPA and OSHA guidelines, you need to have an inspection or exposure assessment prior to a demolition or renovation project. State and local laws may require one, as well.
An inspection should be the first step of any asbestos abatement project. And inspections are often done in the wake of damage from a weather event or natural disaster to ensure that ACMs are still intact and non-friable.
Various tools are used for asbestos inspection, each serving a specific purpose. Whatever tool you need to identify the ACMs in a given location should be used. This will ensure the safety of all workers in the area.
Who Should Conduct Inspections?
Inspections should be conducted by a certified asbestos professional, not regular contractors or construction workers. These individuals are typically licensed by the state.
You can flag potential problem areas for the inspector but shouldn’t disturb materials or perform sampling yourself.
Errors in judgment around asbestos can be both costly to your organization and potentially deadly. Prior to the inspection, verify the inspector’s credentials and ensure they’re carrying extra insurance related to environmental testing.
When and How Often Should You Get an Inspection?
Schools are the only buildings that require regular inspections. A professional inspection is required at least once every three years, and surveillance inspections by a trained custodian are required every six months.
In most states, other building owners only need to conduct an asbestos survey to identify asbestos materials prior to a demolition or renovation project. You may want to get an inspection done after damage to the building from a weather event or to ensure occupational safety.
Visual Inspection
The asbestos inspector will start by taking a look at the PACM and suspected ACM you’ve identified in your building. They’ll then broaden their search to look at every material in the building, even if it hasn’t been flagged as a PACM. In addition to seeing what’s there, the inspector will also check the condition of the material.
They may perform field testing, as well. This is to check the friability of any ACM or PACM, which may impact their recommendations.
Material Sampling
After the visual identification, the inspector will need to take samples of PACM and suspected ACM for laboratory asbestos testing. This is the only conclusive form of asbestos identification.
The sample amount is generally about the size of a thumbnail or a little bigger. There may be minor cosmetic damage, but the asbestos professional will typically try to limit it as much as they can.
Depending on the material, the inspector may take multiple samples. For instance, if ceiling tiles are the suspect materials, they may take several samples from different parts of the building.
Why take multiple samples? Think of a bowl of vegetable soup – any spoonful may be just broth and noodles, but that doesn’t mean there are no vegetables. Remember that an ACM may only contain 1% asbestos – taking multiple samples ensures that nothing is missed.
Laboratory errors are uncommon, but they do happen. Taking multiple samples the first time means that a second inspection won’t be needed if just one sample is compromised.
OSHA, the EPA, and state regulations have very clear guidelines for how an inspection should take place and exactly what lab techniques should be used (typically polarized light microscopy). Some states require that the lab analyzing samples be on an approved list.
Asbestos is a silicate mineral with a crystal structure that interacts with polarized light rays. Though polarized light microscopy requires expensive equipment and an experienced microscopist, it is relatively quick and easy to do.
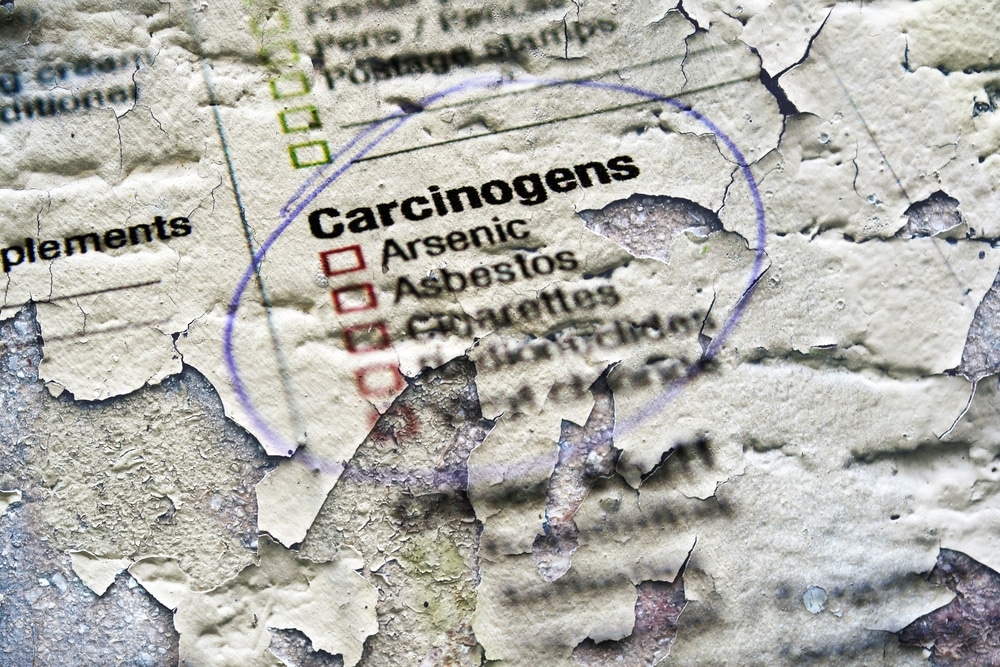
Air Sampling
Air sampling isn’t always a necessary part of an asbestos survey, but it can be a good supplemental technique along with visual and physical inspections. A sample of the air is taken on-site. In the lab, the air is forced through a filter that collects the asbestos fibers.
Those fibers are then counted under a microscope. The standard is below 0.1 fiber per cubic centimeter over an eight-hour shift, though specific states and industries may have tighter regulations.
Air inspection is frequently done at the end of an asbestos abatement procedure to ensure that there are no residual fibers and that nothing is missed.
Rebutting PACM Status
Thermal insulation and surfacing materials in a building completed before 1980 are automatically PACMs. The results of an inspection can be used to rebut PACM status and show that something is asbestos-free.
Your organization should keep those results on file in case you need to rebut PACM status for the building material in the future. Otherwise, you’ll be required to refute the status all over again at the next renovation project.
How Long Will the Inspection Take?
An asbestos professional inspection can take anywhere from a few days to two weeks, depending on the size of your facility and the number of suspect materials or PACMs. The inspector will need access to every part of your facility, including boiler rooms, basements, and crawl spaces.
What Do I Do After the Inspection?
You may not have to do much. If the ACM is in good condition and is unlikely to be disturbed, you can manage it in place with encapsulation or enclosure.
You also need to follow EPA and OSHA guidance if an employee may disturb asbestos – for instance, repairing a light fixture surrounded by ACM ceiling tiles.
You’ll also have to label asbestos-containing material when that material may be disturbed. For instance, if an asbestos-containing floor is being serviced, the entrance to the room should be clearly marked to notify employees and others of the potential danger.
The final report you receive from the inspector will contain recommendations about what can be managed in place and what needs to be removed.
Asbestos Abatement
Asbestos abatement refers to the set of procedures around ACMs to minimize risk and exposure. These procedures can involve encapsulation, enclosure, or removal.
The area where abatement is taking place will typically be sealed off to minimize risk to the building occupants. This can be as simple as using duct tape and polyethylene sheeting to construct a barrier or involve specially designed tents and negative pressure air filters.
Normal business operations should be moved as far away from the abatement area as feasible. Employees who frequently walk past the abatement area may also wish to wear N95 masks.
Who Should Perform Asbestos Abatement?
Abatement should only be done by an asbestos professional. This is not a project for homeowners or ordinary construction workers to take on.
Encapsulation
Encapsulation refers to the application of a seal to damaged or friable ACMs. This seal prevents asbestos fibers from escaping into the air. The technique is also sometimes known as “patch and repair.”
The most common sealants used are polyurethane, polyurea, and epoxies. The process can take up to several days, depending on the size of the area and the number of coats needed.
Encapsulation is typically the cheapest abatement option. It’s also a good choice if the ACM is in generally good condition and useful or if removal is too risky. Pipe insulation is one ACM that’s commonly encapsulated.
Sealants will degrade over time, so encapsulated ACMs still need to be monitored.
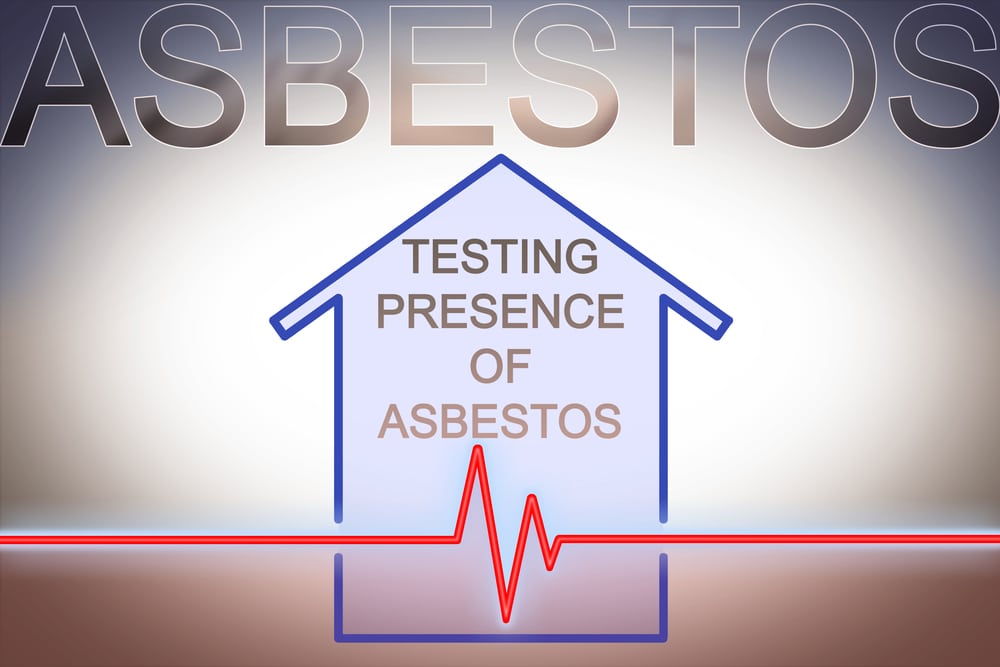
Enclosure
Enclosure involves physically sealing off ACMs. For instance, an ACM insulation could be covered by a layer of drywall.
Like encapsulation, enclosures need to be monitored for safety. Asbestos fibers will continue to enter the air behind the physical enclosure.
Removal
Removal is the only permanent solution for asbestos, but it’s not always the best. It’s costly, labor-intensive, and dangerous to remove ACMs.
During asbestos removal, the area will be physically sealed off. HEPA filters inside the area should be used to clean the air. Exhaust ducts should be used to ensure no fibers escape from the removal enclosure.
Removal workers should wear full protective clothing and respirators inside the enclosure. The material will be placed into thick plastic bags sealed with tape. These bags will then be labeled as toxic or hazardous waste in a dumpster.
Once the ACM is removed, HEPA vacuuming and wet method cleaning can remove any remaining dust and fibers.
Does Asbestos Always Need to Be Removed?
You may not need to remove the material from your building. If the ACM is in good condition, non-friable, and unlikely to be damaged, removing such materials may be a greater risk than encapsulation or enclosure.
Your inspection report may also recommend a combination of methods – for instance, badly damaged insulation around your building’s water heaters may need to be removed, while asbestos-containing floor tiles can be encapsulated.
Recognizing Asbestos-Containing Materials or ACMs – Final Thoughts
Protecting your staff from this hidden killer is non-negotiable. The health risks are numerous, and it’s easy for staff to become exposed if the material’s presence isn’t identified early.
Train your employees in the best practices and teach them about possible health risks. Help your staff stay safe by providing comprehensive guidance on identifying, avoiding, and dealing with asbestos.