When is Lockout Tagout Required? – [Updated for 2023]
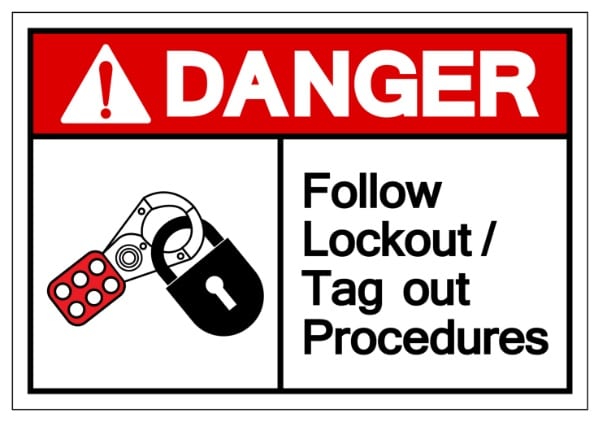
Machinery can malfunction and break down, putting employees at risk of severe injury or death. Lockout Tagout procedures are designed to control hazardous energy to protect workers from electrical or other dangers when working on broken-down machines or electrical panels. Hazardous energy incidents can be avoided by following lockout tagout procedures in the workplace. But, when is lockout tagout required?
Here we’ll explain what a lockout tagout procedure is and when it’s required by OSHA to give authorized employees exclusive control of hazardous energy. We’ll also discuss the importance of having a written plan and what these procedures look like when put into action. Along with our lockout tagout training video will get your team the education they need to work safely. We also have a lockout tagout toolbox talk as well so you should check that out too. For now, let’s get on with the topic at hand.
Is a Written Lockout Tagout Procedure Necessary?
Is it necessary to write down a lockout plan and provide training for employees working in danger zones? Safety hazards are not uncommon in the workplace, and proper training paired with a lockout program can keep employees from using a damaged machine and sustaining an injury.
A written lockout tagout procedure can prepare employees for handling hazardous energy and prevent an unexpected startup from occurring. The Occupational Safety and Health Administration (OSHA) has specific requirements about the use of danger zones and lockout devices that are meant to protect employees from harm. Really, even before you follow any other lockout tagout safety tips, you need to know that a written program is crucial to the success of your hazardous energy program. Always have a written program and provide training to your employee base on how to properly implement your written plan.
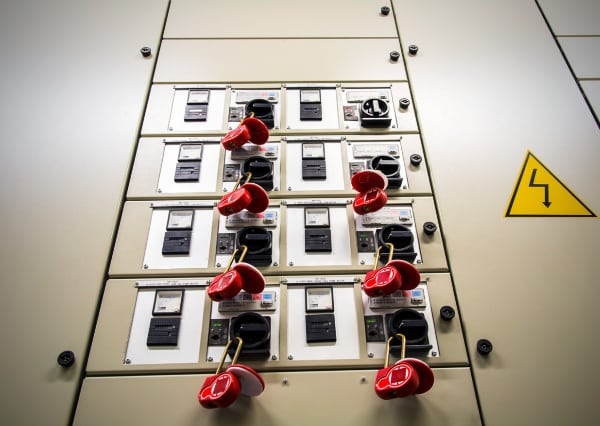
OSHA Requirements for Hazardous Energy
As defined by OSHA, hazardous energy is any electrical, mechanical, thermal, chemical, or any other energy source that supplies machinery with the power to operate. This energy remains dormant while a machine is not operating, but can cause the machine operating cycle to start up unexpectedly. Such hazardous energy poses a serious threat to workers, as unexpected energization can put their lives at risk.
OSHA requirements include the use of multiple locks to prevent energy sources from becoming potential hazards. The OSHA standard covers the safe release of potentially dangerous energy using alternative measures to ensure workers are not hurt. A designated danger zone exists to keep unauthorized employees away.
The control of hazardous energy must be handled by an authorized employee who has received comprehensive training on workplace hazards and how to provide effective protection. Additionally, frequently updated training and retraining for new machinery, electrical hazards, and energy control procedure plans will ensure that workers are familiar with equipment and safety practices.
Lockout Tagout PPE Requirements
Using the right personal protective equipment will keep employees safe from harm. Some commonly asked questions inquire about what kind of PPE needs to be worn when working on equipment that is locked or requires maintenance.
The machinery must be turned off in a safe position so that the hazardous area is contained. Following lockout tagout procedures, the control of hazardous energy requires the authorized employee to wear the same level of safety equipment they would normally wear when operating the device. This is to ensure that the employees are properly protected from construction equipment in the event of an incident.
Only an authorized employee should perform routine maintenance or execute normal production operations when a lockout tagout procedure is in place on certain equipment. They are properly trained to use the equipment and understand the necessary precautions they must take to operate safely.
What are Energy Isolating Devices?
Energy isolating devices are intended to cut off the power supply to machinery that needs work, allowing staff to begin servicing the de-energized machine. Maintenance cannot be performed while the machine is active and energized, which is where the use of an energy-isolating device comes into play.
Methods of servicing construction industry machinery vary, but one of the most effective is taking control of the energy source and cutting the ties between it and the machine. Equipment cannot be serviced while residual energy is present, so how can you dissipate that so the electrical components can be accessed safely?
How Stored Energy Works
Stored energy, also known as residual energy, is the power that has not yet been released and resides within the equipment power supply system until it is used. An authorized employee will have exclusive control over the lockout tagout procedure and other methods of servicing equipment to ensure the safety of their coworkers.
A lockout tagout program cuts the equipment’s connection from the energy source through an energy isolating device. The equipment continues to store the energy while being serviced, which is why an energy control procedure is necessary to release it. An employee can easily be injured by machines that unexpectedly restart if they aren’t properly locked.
Why You Need an Energy Isolating Device
Standard employee training should have normal production activities covered in addition to other safety device procedures regarding maintenance. The minimum performance requirements for an energy control procedure is that it protects employees from accidentally reactivating machinery that needs service. The lockout device on the machines prevents energy sources from reaching the controls, ensuring everyone’s safety.
The employee assigned to do maintenance and service the equipment is responsible for securing the lockout tagout program. Once service is complete, the employee servicing the equipment can release that energy and secure the lockout device again.
How a Lockout Tagout Procedure Looks in Action
Establishing the minimum performance requirements for an energy isolating device means keeping every employee safe through a lockout tagout program. The training information is one of many free resources in the workplace that employees have access to before operating equipment.
There are several steps to a lockout tagout to secure other devices during routine maintenance. Like other standards for equipment and safety, a lockout tagout procedure is intended to keep employees safe when followed correctly.
Perform Maintenance Regularly
Performing routine maintenance on equipment is a preventative step. Examining the equipment for malfunctioning parts and servicing the equipment with a minor tool for repairs can prevent serious breakdowns from occurring.
Additionally, using comprehensive or free resources for training, employees can learn to recognize warning signs that equipment isn’t functioning properly and report it. This allows authorized personnel to utilize the lockout program and begin servicing the equipment.
Inspect Faulty Machines
An abnormally operating machine is already an issue, which is why a lockout program is used. This ensures that the machine remains dormant when being worked on or operated. Shift changes won’t affect machinery when a lockout program is used.
Using this system to inspect faulty machinery enables engineers to work on the issue without the risk of the equipment starting up without warning and causing serious or fatal injuries to the worker. Any repairs will need to be done when the lockout is enabled to minimize the risk of a workplace incident.
Notify Affected Employees
When the lockout tagout program is active, it’s important to notify the affected employees. Since only authorized personnel can operate the equipment with the designated key, others must be informed about the change in procedure. It’s for their safety and, therefore, they should be kept up to date.
The system is designed to prevent power from being restored to the equipment while it is being operated on or repaired. The only person on-site who can restore power is the individual performing the work themselves. That way no other employee can turn the power back on and put their coworker’s safety at risk.
Repair Broken Equipment
Broken machinery must be repaired immediately to prevent future breakdowns and further incidents. Utilizing a lockout tagout procedure will enable engineers to get to work without the risk of getting injured on the job. Technicians can do their work without worrying about the equipment being active, allowing the repairs to be completed on time.
A machine that starts up unexpectedly, especially a broken one, is a hazard to all employees on the job site. Making good use of the lockout system prevents that from happening so that working conditions are safe for all employed technicians.
Retool The Machine (If Applicable)
The system can also be used to allow the repurposing of the original equipment. These parts can be collected once a lockout tagout system is in place so that technicians can safely remove them. Once collected, the parts can be used to make a different model or product that can benefit the job more.
Doing so is sometimes cost-effective, and yet another benefit of cutting off the power supply. Without the lockout tagout system in place, the machine could begin operating unexpectedly while parts are being stripped, and the technician tasked with retooling the machine could be seriously injured in the process.
Safety First, Always
The construction industry uses the lockout tagout system because it is effective and safe. No matter the reason that technicians must enter a dangerous zone, for whatever purpose they need to work on or near a machine, the proper protocol must be followed to secure their safety.
There are no shortcuts with safety and lockout tagout equipment. They are designed and intended to keep technicians safe from malfunctioning equipment and dangerous work that must be done. Always put safety first and never compromise on it to save time. The safety of the technicians takes priority over the machinery, which is why the lockout tagout system is in place.
The Bottom Line
OSHA requires a lockout tagout system to operate equipment that can be dangerous to any employee if it powers up unexpectedly. This ensures that all technicians are safe on the job and that only authorized personnel can restore power when needed. Following protocol and complying with OSHA regulations will keep your working conditions favorable and your staff members safe. Understanding when lockout tagout is required is the first step in your training program.