Skid Steer Accidents – [2023 Facts, Statistics & Safety Tips]
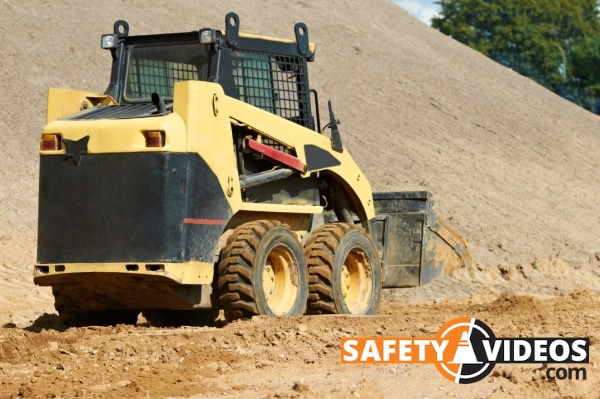
A skid steer loader is a useful piece of equipment across various job sites. However, the severity of accidents involved with this type of machine underscores just how seriously employers and employees should take training and safety precautions. Training on skid steer safety should be one of your main focuses if your company uses these machines on the job site. Along with the accident information we give her, the goal would be to prevent these accidents from happening in the first place, and the best way to do that is through proper training.
Let’s learn more about the facts and statistics around skid steer accidents so you and your team can be prepared for your next job. By the way, we also have a Skid Steer Toolbox Talk that you should check out as well.
What is a Skid Steer Loader?
A skid steer loader, or skid loader, is a popular piece of heavy equipment because of its incredible versatility. Steer skid loaders can operate even in tight spaces, allowing them to get the job done where other heavy machinery can’t. And with a variety of attachments available, they’re suited for many jobs.
Skid steer loaders include a cab for an operator set on wheels or tracks. However, the wheels don’t turn. The machine advances when the operator increases the speed on one side. It all features two hydraulic lift arms on either side of the cab. Depending on the attachment, these are meant for digging, lifting, excavating, and more.
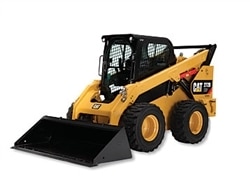
How Do Skid Steer Accidents Occur?
A skid loader accident occurs when either due to failed operations or failure of the equipment, the machine causes injury to the operator or a nearby victim.
Part of the reason for the severity and frequency of skid steer accidents is the inherent design of the equipment that could be considered flawed in terms of safety. This is because the seat of the driver is positioned between the lift arms, and the operator’s seat is in front of the lift arm pivot points. This leaves the only option for entering and exiting to be the front of the cab — between the lift arms and over the bucket. If anything were to go wrong during an entrance or exit, an operator’s chest, hands, feet, or head could be crushed.
However, accidents aren’t limited to this daily maneuver. A skid steer loader accident may occur during operation to someone outside the cab or if an operator is thrown from their seat. Accidents vary, though the final result is typically the victim being crushed or run over.
Injury Facts From Skid Steer Loader Accidents
Due to the severity of injuries sustained by skid steer loader accidents, many are fatal, resulting in a victim’s death. Of course, not every skid steer loader accident will result in death. Mechanical injuries may result in the loss of a limb, broken bones, pinching, asphyxiation, or brain injury.
However, these aren’t the only types of injuries. Those who frequently operate machines powered by diesel engines that emit exhaust fumes could suffer from poor respiratory health. To avoid risks to respiratory health caused by diesel engines on skid steer loaders that emit exhaust fumes, respirators can be worn.
Hydraulic pressure is another important part of how the machine runs that could lead to injury if hydraulic fluid is injected into someone. Luckily, an easy way to prevent this is to ensure only those with training in handling hydraulic fluid manage the pressure on the loader.
Additionally, with the loud noise from the loader, being near without ear protection could be endangering hearing. This can be avoided with proper protection over the ears.
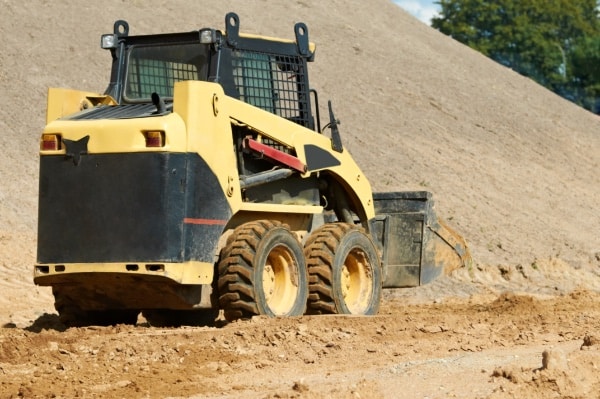
Skid Steer Safeguards and Protective Structures
Despite the design that places people entering and exiting the cab of a skid steer loader in danger, there are safety features that are meant to prevent accidents.
While there are numerous features, these are two that are a must-have for all skid steer loaders. Don’t invest in skid steer loaders without these safety features to avoid avoidable, fatal accidents.
Interlocking Controls
Interlocked controls are designed to keep the engine switched off, and the hydraulics disengaged if an operator isn’t in their seat and ready to maintain control. The pressure switch is used to determine whether an operator raised themselves out of the chair or not.
If the pressure switch doesn’t keep the interlocked controls in action to control the vehicle, the lift arms may not be kept immobile. In this case, a load falls because the arms aren’t locked.
A further safety feature is that the operator can manually lock the arms when they have exited the cab and the skid steer loader is under repair or maintenance. But overall, interlocking controls are a crucial backup. And those that are enacted automatically are best.
Rollover Protective Structures
Rollover protective structures are parts of an overall system to keep accidents from happening that result from a skid steer loader rollover incident. For example, a skid steer loader may easily tip over under the right conditions, even when in a wash bay.
But whether in a wash bay or out in the field, this system must keep operators in the cab, far from the danger of being beneath the front wheels or lifting arms. If a loader rolls, the operator may be ejected from the cab, resulting in to prevent serious injury.
These protective structures include:
- Safety Bar
- Seat Belts
- Side Screens
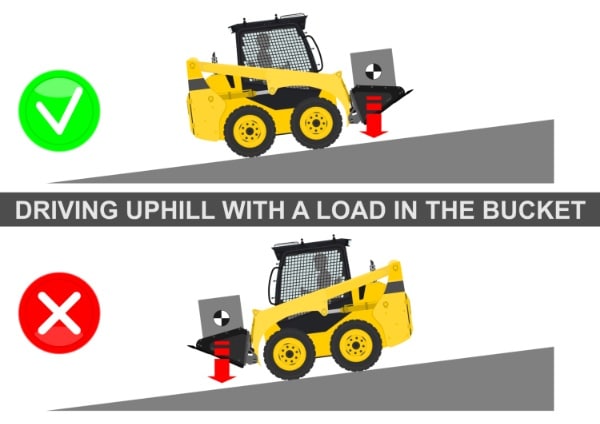
How Skid Steer Accidents Happen
With so many components involved in operating skid steer loaders, from loader arms and a loader bucket to what happens when heavy machines don’t operate on level ground, a lot can possibly go wrong. Unfortunately, workers may find themselves visit visiting a local hospital or, worse, pronounced dead at the scene, all because of due to skid steer loader accidents.
But how precisely do skid steer accidents come about? This question must be thoroughly answered for employers and employees alike to do everything to avoid these accidents.
While this is by no means an exhaustive list of skid steer loader accident possibilities, some of the most common skid steer loader accidents are due to situations like these, with some examples provided by the National Institute for Occupational Health and Safety and the Occupational Safety and Health Administration.
Interlocked Controls Failure
As mentioned above, interlocking controls ensure lift arms are locked when an operator isn’t in their seat and operating the vehicle. But if the pressure switch fails, leaving the interlocked controls not functioning, this means a crucial safety feature isn’t working.
One way they may fail is in extreme winter conditions. If the controls freeze, they may not lock the arms when the operator exits. Then, during repairs, maintenance, or entering and exiting, a skid steer loader’s lift arm may unintentionally be turned on, harming an operator.
Improper Exiting
If a skid steer loader rolled or the lift arms were suddenly enacted, an improper exit from the machinery is fatal. Operators should only exit when the lift arms have been completely immobilized by locking controls.
Because of the design of skid steer loaders, the side of the cab is between lift arm supports and arms. Side screens are designed to keep riders inside in the event of a rollover, but operators may purposefully defy these regulations. And while exiting from a side of a cab vs. the front may not sound serious, it can be fatal. This was the case for one operator who had removed the screens, exited from the side, and then was the victim of lift arms that had accidentally been turned on.
Unsupported Bucket
If there isn’t a mechanism providing support for a bucket on a skid steer loader, the lift arms could be activated accidentally at any time. When this happens, the load falls along with the bucket.
If someone is working under an unsupported bucket, perhaps performing repairs on the skid steer loader, entering, or communicating with an operator, this could leave the person pinned between the bucket and frame when the load falls.
Any operator or bystander must be aware that controls must be in place to keep buckets raised. Without controls, they may fall, pinning a victim.
Working Near or Under a Loader Bucket
Similar to a bucket lowered accidentally, workers are often the victims of simply working too close to the cab beneath a bucket. If an operator raised a load, it might seem safe to be near or underneath.
Even if controls are firmly in place, accidents can still happen. When a bucket is raised, a skid steer loader doesn’t have a strong center of gravity. This is why operators drive them with any bucket lowered. So while working, if skid steer loaders easily tip due to a lack of balance, anyone under the bucket is in danger. This could also occur if an operator simply doesn’t see someone else while working.
Backing Incorrectly
Due to the nature of how skid steer loaders move, backing up isn’t always simple. Each side must move before the other set of wheels can.
In one incident, a left rear tire went over a small retaining wall and was followed by the right rear tire. This resulted in the machine rolling over, leaving the driver between the operator’s seat and the side screen. This person suffered from asphyxiation, and the operator died.
Operators must stay aware of their surroundings and unlevel surfaces to avoid tipping the machine over.
A Lack or Removal of Safety Side Screens
As mentioned before, the right and left side screens are important safety features to prevent serious injury to an operator. If a loader hit an obstacle and tipped forward or over, an operator could only be kept in the cab by screens. If the screens aren’t there, the operator may be left under the bucket or arms. If these move down, the operator would be crushed or pinned by the skid steer loader.
A lack of screens should be immediately rectified by an employer. However, employees may naively remove the screens for greater convenience. These should never be removed, as this could result in fatal injuries.
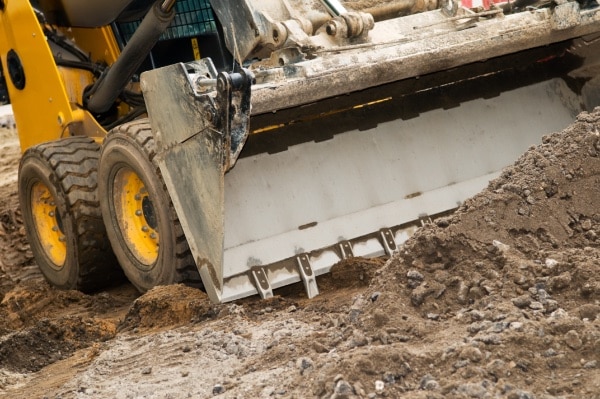
Skid Steer Loader Accidents — Fatality Statistics
These heavy machines are known to cause fatal injuries to operators and bystanders alike. This means that, unfortunately, there are many cases to explore and study the accidents caused by this equipment.
Here are some of them as compiled by the Center for Disease Control (CDC):
- Of the 54 fatalities caused by skid steer loaders between 1980 and 1992, these were the exact causes:
- 25 victims were pinned between the bucket or lift arms and frame
- 15 victims were generally crushed
- 11 people were rollover victims — i.e., a skid steer loader tipped forward or sideways
- 2 people were pinned between an object and a skid steer loader
- 1 person was killed when a loader ran over them
Clearly, incidents in which a victim is pinned by the equipment itself are the leading cause of fatalities. However, the cause for being pinned varies as well. Below are the situations that led to a pinning accident by a skid steer loader:
- A person working or standing beneath a raised loader bucket
- An operator leaning out a window and was beneath the lift arms when they moved down
- Someone entering or exiting the cab and was pinned by the bucket to the frame
These statistics are good indications of how training should be directed to help operators understand their duties and how best to prevent accidents caused by skid steer loaders.
Standards and Regulations for Operating Skid Steer Loaders
The Occupational Safety and Health Administration often referred to simply as OSHA, has many standards in place. For businesses to be in compliance with OSHA, they must follow regulations put forth by the organization. This is beneficial not only for reducing employee injuries but also for other financial benefits like insurance savings.
Because a skid loader is designed with the cab in front of the lift arm pivot points and between the arms, there are many machine-specific requirements in addition to general safety measures.
- Safety tips for a skid steer loader include:
- A distinguishable horn to signal to others
- Scissor points are guarded
- Seat belts are provided
- Buckets must be lowered or blocked during repairs and maintenance with controls in neutral and brakes set
- Adequate rollover protective structures (ROPs) must be in place
- Any changes that affect the safety of the machine must have written approval from the manufacturer
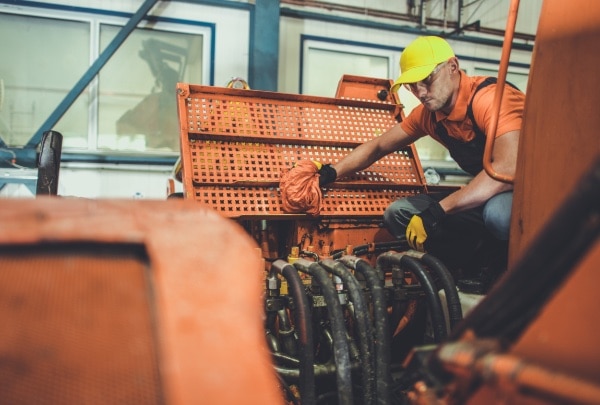
Tips for Maintaining Skid Steer Loaders Properly
Performing maintenance is a necessary part of having a loader on site. Here are tips for ensuring your maintenance check goes well:
- Don’t perform maintenance with the engine running. Unless otherwise noted by your manufacturer’s manual, keeping the engine running during maintenance is a serious safety hazard.
- Follow all the manufacturer’s guidelines and instructions.
- Ensure the foot controls are clean. They should not have any debris, ice, mud, or snow.
- Only conduct maintenance with the bucket lowered, the machine in park, and the key removed from the switch.
Maintaining Safety Devices On The Skid Steer
To meet adequate safety precautions, the below safety devices must be both present and maintained. Regular inspection is a must to ensure they are working properly to keep operators and bystanders safe.
Lift Arm Supports
Lift arm supports are used to keep the load secure while the loader is receiving maintenance or repairs. Lift arm supports must be used during these scenarios. If your loader didn’t come equipped with these devices, reach out to the provider immediately. DIY solutions like concrete blocks won’t be enough to support the load, leading to serious injuries for whoever is caught under the bucket or arms while working on the loader.
Interlocked Controls
Interlocked controls keep lift arms in their place if an operator isn’t in the seat and properly strapped in. This means failure of the interlocking controls could be fatal to anyone near the arms or bucket if the controls were to fail.
To ensure safety for operators, bystanders, and the repair team, regularly inspect the controls. If they’re not engaging properly, maintenance must be performed before using the machine.
Seat Belts and Safety Bar
During maintenance inspections, the seat belt should be tested to see if it can fit securely around operators. The safety bar should also be secure when engaged to keep the operator in the cab in the event of a rollover.
When these safety features aren’t engaged, interlocking controls should be enacted. Ensure these various features are correctly working in tandem.
Additional Retrofit Packages
Any safety equipment that your loader is missing must be retrofitted for additions. This might include replacement screens or lift arm locks to keep arms raised during repairs or maintenance. If anything stops functioning correctly or comes up missing during maintenance checks, contact the manufacturer about replacements or additions.
Tips for Operating Skid Steer Loaders
During training sessions, employees should learn all the following safety tips:
- Upon entering, use the safety belt and bar
- Don’t operate the machine from outside the cab
- Remain seated during all operations
- Keep all body parts inside the cab
- Work on level, stable ground as much as possible. The less level the ground is, the higher the likelihood of rolling the machine.
- When the machine is in motion, keep the bucket as low as possible to lower the equipment’s center of gravity
- Never exceed the maximum load capacity of the given loader
- Travel straight up or down slopes rather than across
- Keep bystanders away
- Face the way you are traveling
- Follow all safety instructions
Tips for Entering and Exiting Safely
Because of the lift arms, entering and exiting is perhaps the most dangerous part of operating the machine. To keep things safe, follow these tips:
- Have the parking brake on
- Keep it on stable surfaces — surfaces should also be free of debris, mud, and ice
- When entering, face the seat and use the grab bars and steps — use a three-point contact rule
- Never exit through the side
- The bucket should be lowered
- Enter and exit when the engine is turned off
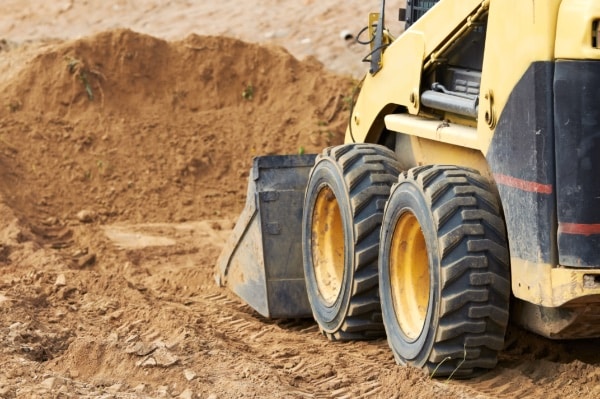
Skid Steer Loader Training for Occupational Safety
Because a loader can easily tip when unstable and comes with additional risks for any job site, training is crucial. Here is what employers and employees can do to prepare for training and beyond.
What Employers Should Do
Employers should plan training opportunities to keep employers aware of what they need to know when operating or working near a loader. They should also ensure safety signs are posted, their team is performing maintenance, and that a plan for contacting emergency personnel when needed is ready.
What Operators Should Do
For safe operation, anyone planning on using a loader should adhere to guidelines set forth in training sessions, follow the operator’s manual, and perform simple safety tips like wearing a safety belt. They should also wear any additional PPE to avoid the risk of endangering hearing or directly breathing fumes from the diesel engine to address additional risks.
Be aware of your surrounding so you can operate safely with each lift arm and avoid accidents.
The Essentials of Avoiding Skid Steer Loader Accidents
A skid steer loader accident happens quickly, and there’s little time to react. This means that rather than preparing for incidents, you should spend more time preventing them. Of the most common incidents, here are the tips you should follow to prevent them.
Crushed by Moving Parts
If an operator exits the cab beneath the lift arms and the loader bucket is lowered, they can be crushed by the moving lift arms. To avoid this, operators should:
- Enter and exit when the engine is off
- Don’t use control levers as grab bars
- Use the steps
- Park on level surfaces
- Ensure the bucket is lowered
Rollover Accidents
When unstable, a loader can tip over. Once a loader rolls, the operator can’t possibly act quickly enough to save themselves.
For example, if a loader rolled and an operator was ejected and pinned under the front wheels on the operator’s chest, it’s likely the operator died before any help could be brought in. This is why safety precautions must be in place to stop the accident.
Safety precautions that keep an operator in the cab include screens, seat belts, and a safety bar. But to prevent a rolling accident altogether, follow these tips:
- Carry loads low
- Don’t overload
- Avoid rough, uneven surfaces
- Drive slowly
Traffic Accidents
Skid steer loaders aren’t designed for public roads and highways. For safety, it should be brought to job sites. However, if it must be driven on roads, follow these tips so that you won’t have a loader hit a pedestrian, vehicle, or obstacle and avoid injury:
- Lock attachments securely
- Wear a safety belt
- Observe the rules of the road
- Allow faster moving vehicles to go first at intersections and move cautiously
- Don’t drive at night without lights
- Drive with a slow-moving vehicle emblem, sharing that you won’t be going over 25 miles per hour
Runovers
If a loader ran over a bystander, this would be known as a runover loader accident. The injuries sustained could be fatal to the victim and could also endanger the operator by causing a rollover.
To avoid this type of incident, a horn should be maintained and properly used to alert bystanders of where the machinery is. This way, people can get out of the way. Additionally, operators should be diligent about maintaining an awareness of their surroundings.
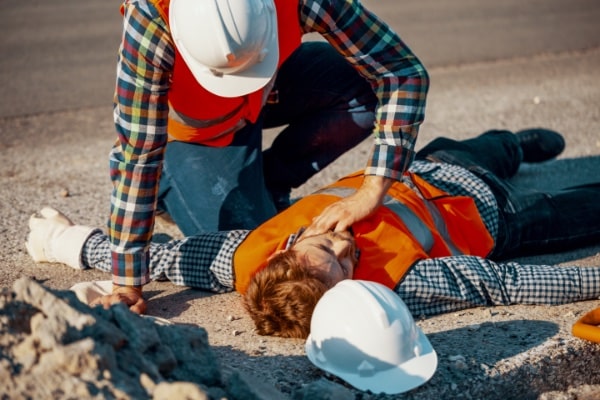
Frequently Asked Questions about Skid Steer Accidents
Are skid steers safe?
With the proper safety equipment, a loader can be safe to operate and be near. However, they can be deadly when used improperly or not adequately maintained. Safety devices like seat belts and support for loader arms are crucial. The best way to ensure a loader is safe is to stick to the standards set by OSHA, adhere to regular maintenance inspections, and follow the tips for proper use.
There are additional risks to be aware of that often come with heavy machinery. As diesel engines emit exhaust fumes, workers breathe in these fumes, damaging their respiratory health. Respirators can be worn for protection. Similarly, the loud noises of a loader may be endangering hearing, so ear protection is recommended.
Are skid steers stable?
A loader is fairly stable when the bucket is lowered. However, it has greater instability on unlevel surfaces, hills, or when the bucket is raised. To ensure you’re operating the loader correctly and with the greatest stability, adhere to all the manufacturer’s instructions.
Skid steer loader accidents often occur when there’s instability with the loader, as it could roll over. For example, if a tree shifted while a loader was pulling it on a stable surface, there may not be a problem. But if a tree shifted while on a hill, the loader could easily tip over, endangering the operator and bystanders.
What should you not do with a skid steer?
As an operator, you should adhere to all the standards and regulations put forth during training sessions and materials. To protect yourself from the potential dangers of skid steer loaders, never operate a loader without ensuring that it’s been properly maintained.
If any safety devices seem to be not working or missing (for example, the seat belts aren’t working or the side screens are missing), do not operate the machine.
Enter and exit as advised per the manufacturer’s instructions and operate with careful diligence and attention.
Operate Your Skid Steer Loader Safely
Skid steer accidents are severe because this equipment is heavy machinery with strong loader arms. Knowing the facts and statistics of the most common injuries and additional risks should be enough to inspire any employee or employer to take safety precautions seriously. In addition to basic PPE, the loader arms should always be accounted for, and the machine should be maintained for optimal safety. Practicing good safety protocol will help lower the number of accidents you have, and this is a benefit to employees and the employer alike.