Forklift Accidents – [Facts, Statistics & Tips for 2023]
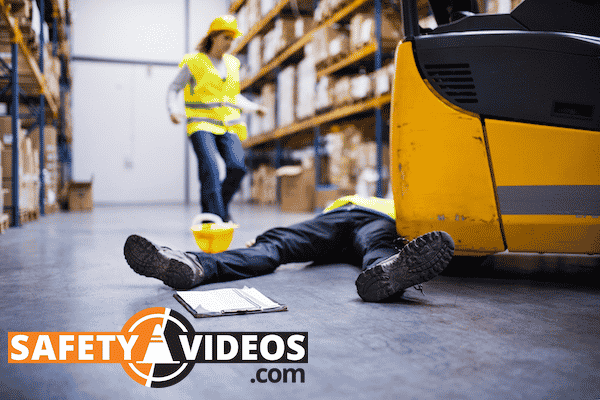
Why is Forklift Safety Important?
A forklift truck is a piece of machinery that can weigh up to 20,000 pounds. This alone should tell you why proper safety education isn’t negotiable. While many trucks weigh between 3,000 and 10,000 pounds, that’s still as much as a mid-sized car, even at the lower end. This is why getting your employees proper forklift certification is important to both your employees and your own business.
These trucks are essential for many workplaces and are frequently used in tight spaces. Knowing how to steer, maneuver, and reverse an industrial truck safely minimizes the risk of running into high shelves that might contain heavy boxes. Aside from the fatal risk that this poses to the driver and other workers nearby, falling inventory will likely be irreparably damaged. This could cost you thousands of dollars in replacements.
When operating a powered industrial truck around pedestrians, the burden is on operators to understand the hazards. While the work area should be marked so that accidents are impossible, pedestrians will generally assume a “safe distance” without understanding that some trucks can rotate on the spot and risk a collision. Falling loads from the truck can also spill over and hit passers-by.
How Common are Forklift Accidents?
The Bureau of Labor Statistics (BLS) estimates that between 2011 and 2017, approximately 8,500 to 9,000 non-fatal forklift accidents occurred per year. That’s a rate of about 25 injuries per day across the U.S. Meanwhile, between 74 and 94 deaths occurred each year involving this type of industrial truck.
What is the most common accident on a forklift?
The most common forklift accidents tend to involve either:
The vehicle overturning, or falling loads.
Injuries aren’t limited to the forklift operator – a large proportion of accidents also involve passers-by, whether they’re colleagues or pedestrians.
Both these issues can be mitigated by improved educational resources. A properly-trained forklift driver will never attempt to lift a load that risks toppling – they’ll always accept that the job needs to be done slightly more slowly but far more safely.
While it’s impossible to reduce the chance of an accident to zero, education should focus not just on load manipulation but when to accept that a load simply can’t be moved safely.
How many people have died from a forklift accident?
Roughly 1% of forklift accidents result in a fatality. It’s been reported that a rough average of 1 in 6 deaths in the workplace is forklift-related in the U.S. – it’s one of the most deadly parts of any workplace. Too often, this comes down to poor training and rushed operation.
Proper maintenance routines and the ability to report faulty equipment are so important for improving safety standards. Operators should know how to identify common problems and pass this data along to their companies – the companies should then take the vehicle out of commission until it’s fit for service.
Failure to provide better training for operators in terms of maintenance and usage causes needless fatalities and costs industries millions of dollars each year. By contrast, teaching employees using simple videos and other techniques costs almost nothing.
What are the most common forklift injuries?
The most common forklift accidents tend to result in broken bones, crushed limbs, and often traumatic injury. This can prevent workers from returning to the workplace for years or even rule them out of their old job for life.
Employees injured in a forklift-related incident are liable for significant payouts from their employers if specific standards weren’t observed. This applies whether it’s non-serious injuries like minor scrapes or life-threatening damage – educating operators and staff to safely use and work near heavy equipment is a no-brainer for employers.
What is the most common forklift fatality?
In recent estimates, the most common type of fatality involved a truck tipping over. This category includes operators, pedestrian traffic nearby, and employees working alongside the vehicle.
It’s worth restating that powered industrial trucks typically weigh thousands of pounds. Their active stability is very poor for such heavy vehicles compared to other heavy machinery because they’re tasked with lifting loads high into the air. A slightly off-center truck is a threat to the operator and anyone around it.
What Causes Forklift Accidents?
There are many reasons for forklift injuries, but most come down to poor operating practices. Mechanical failures are another frequent reason for accidents, but most issues are avoidable if proper procedures are in place and followed by staff.
Nobody should operate a forklift unless they feel entirely comfortable working with the equipment. Staff needs to be able to speak up and request more safety education wherever necessary – this isn’t expensive and saves lives and money.
What is the most common cause of forklift accidents?
Operators who haven’t been appropriately trained are the single most common cause of workplace accidents. The “technical” cause of the problem might vary, but it usually stems back to operators who shouldn’t be using the equipment in the first place.
A forklift accident caused by a faulty parking brake is only half-caused by the machinery itself. Operators should know to check brakes and the vehicle’s functionality before using them to lift loads.
Likewise, understanding whether surface conditions will allow for safe operation is a knowledge problem. A well-trained driver will point out when conditions aren’t suitable for lifting a load or rounding corners while carrying loads.
Forklifts are substantially different from other vehicles and should never be approached by someone who has operated “something similar”. There are also many types of forklifts – educational resources should be suitable to the types of machinery used in your workplace, rather than a one-size-fits-all guide.
What are the 4 main causes of injuries when using a forklift (OSHA)?
Generally speaking, the 4 most common causes of injury are:
- Untrained operators
- Mechanical issues
- Excessive speed
- Poor floor design
Navigating tight spaces in an industrial truck is difficult and requires practice. “Complete racking failure” refers to an incident where the truck collides with racking that holds inventory. The racking tumbles in a domino effect, creating thousands of dollars worth of damage and putting the lives of everyone working in adjacent aisles at risk. While this type of incident is relatively uncommon, it can be devastating.
Someone trained in forklift safety will know to alert pedestrians in nearby work locations before they begin using the truck in a tight space. Safety solutions like floor tape should also be in place to ensure that the driver knows exactly how close they can move in any direction.
An operator using excessive speed should be reported immediately by any nearby staff. Lift trucks aren’t toys, and a workplace isn’t an empty parking lot. Whether it’s simply someone hurrying to get their job done or a forklift driver “having a bit of fun”, speeding is a no-go for forklift safety.
Safety Information for Forklift Operators
Data on the number of people killed annually by forklifts is sobering. Here’s what you need to know to ensure that you don’t risk becoming a statistic as a forklift operator. You can also check out our write up on Forklift Safety Tips.
What should I know about a forklift?
Here’s what to check for before operating an industrial truck.
Is it safe to drive? You should feel confident that the lift truck is working at 100% before using it for any lifting application from the rear axle to the seat belt fitting.
Have I been trained properly? Do you feel comfortable with the resources you’ve been given? You should have had access to safety videos and practice in a non-industrial setting. You should also have been mentored by an experienced driver when using the truck for work.
Is the overhead guard appropriate? This guard can protect you against falling items. Is it sturdy enough to protect against the type of materials you’re working with? Not all work environments are the same!
Is the fuel mixture topped up? You don’t want to run out of power while lifting a load. The truck should indicate when power is low but always double-check before use.
Is my forklift license current? Sometimes, employees get their forklift licenses revoked and can no longer legally operate a lift. It’s up to the employer to make sure all licenses are up to date and above board.
What is a forklift mainly used for?
Forklifts are used in a wide variety of industrial settings, including:
- Manufacturing
- Warehouses
- Retail
- Construction
- Recycling & waste facilities
- Dockyards
Ensure that the truck at your workplace is the right equipment for your setting. Companies should choose carefully when investing in machinery – it makes your workers’ jobs safer and easier. Furthermore, if there’s an incident (e.g., a forklift tipped over) and it transpires that the truck was inappropriate, it could land you in legal hot water.
What are the OSHA regulations for forklifts?
OSHA requires that all operators undergo operator education described here. One of the most accessible ways to train employees is through industry-compliant videos. It also notes that nobody under the age of 18 should operate a forklift.
What are the hazards of forklifts?
Common hazards include:
- Unbalanced loads falling
- Vehicles tipping over
- Insufficient head protection
- Collisions with racking
- Collisions with pedestrians (e.g., the rear wheels running over someone’s foot)
What are the 8 safety principles when using forklift equipment?
Educational resources may use different principles and techniques to teach how to avoid forklift-related injuries. While there’s no “exhaustive” list of best practices, any educational materials should be rigorous and backed up with practical lessons for a novice operator.
8 good tips might include:
- If in doubt, don’t lift it. If a load doesn’t feel steady or secure, wait until it can be arranged properly.
- Know what’s around you. Spatial awareness is key to preventing collisions with racking.
- Know who’s around you. Account for all your colleagues’ whereabouts before moving and any other people who might be nearby.
- Inspect before use. Notice anything “acting up” on the truck? Report it, and don’t use it until it’s fixed.
- Are you trained? Not all trucks are the same. Were you trained for this type of truck? If not, why are you using it?
- Are you prepared? Is your belt secure? Is the guard in place? Basic checks can save lives.
- Is the environment safe? Slippery floors and unstable racking are environmental hazards. Not a good place for a 5,000lb behemoth.
- Does it meet OSHA standards? If in doubt, ask. Your employer has a responsibility to keep you safe in the workplace.
What are the types of forklifts?
There are many types of forklifts – this is why it’s so important to ensure that the one you’re using is appropriate for your workplace. Common types include:
- Counterbalance trucks
- Order pickers
- Powered pallet trucks
- Reaching trucks
- Stackers
Forklift operators should feel confident with any truck they’re asked to use. The best policy is always to ask for more training if you’re unsure.
FAQ & Forklift Accident Statistics
Who invented the first forklift?
It depends on the truck’s application and who you ask! The Clark Company is considered an early pioneer alongside Yale & Towne Manufacturing. Similar vehicles were developed worldwide in the mid-20th Century.
What is the chance of you dying on a forklift?
Very low – as long as you follow basic forklift safety practices. Your employer should provide comprehensive preparation before asking you to use one of these trucks. This is your best protection against injury or a fatal accident. It’s also essential for keeping those around you safe in a dangerous workplace.
How many forklift fatalities occurred in 2020?
Data suggests that 78 fatalities occurred due to a forklift accident in 2020.
How many forklift fatalities occurred in 2019?
79 fatalities were reported in 2019.
How many forklift accidents were there last year?
Information for just this past year isn’t currently available. However, the number of deaths in this area can be significantly reduced over the coming years by implementing proper safety procedures in your workplace.
What does a forklift accident cost?
A forklift accident has several “costs” that must be considered:
- The cost of the workers compensation claim that will happen if an employee gets injured on the job operating the lift
- The cost to repair a wrecked forklift
- The cost of “lost time” for an injured employee being away from work
- The cost of “lost productivity” which results from a damaged forklift being off the production floor
The best estimate is that the average forklift accident would cost in upwards of $28,000 when all factors are considered.
How to prevent forklift accidents?
The best way to prevent a forklift accident is to provide your employees with proper training. This would include how to maintain a forklift, how to properly operate the lift, what to do when operating a forklift around pedestrians, the importance of not allowing “horseplay” among forklift operators, etc.
Improve Forklift Safety In Your Workplace Using Forklift Training Videos
Safety videos are an essential part of proper training. They should be backed up with on-the-job experience so that your workers can feel confident when operating heavy machinery and minimize the risk of injuries or deaths.
Take a look at our OSHA-compliant forklift training for all types of forklifts and workplaces. Be smart, be safe – prevent disasters in your workplace.