13+ Best Construction Safety Tips for 2023 – SafetyVideos.com
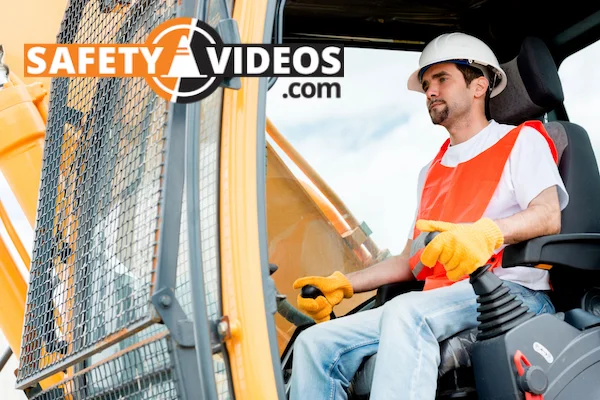
Construction sites are dangerous work environments full of potential hazards. Therefore, a solid understanding of safe working practices is essential for employees and operators whenever they work on a construction site.
So what do you need to know before working on a job site? What construction safety tips are available that you can share with your crew?
A well-managed job site with proper precautions keeps workers safe, ensures that work operations are as smooth and efficient as possible, and protects your company from OSHA fines and penalties.
Our construction safety tips cover everything you need to know about training staff, implementing suitable safety measures, and managing a construction site. And if you are looking for general safety tips for work we have a separate list of those.
Vital Construction Site Safety Tips
Common sense underpins all these safety tips – however, this needs to be backed up with proper training. The construction industry is notorious for having a high level of workplace accidents. Still, many of these are caused by untrained staff assuming responsibilities or operating equipment they aren’t prepared for.
Safety procedures must be understood and implemented from the highest management level downward. Every worker on a site should understand how to identify hazards, check vital equipment where appropriate, and what type of protective systems need to be in place for safe operation.
Employers need to provide construction workers with ongoing training to keep them up to date with guidance from OSHA and ANSI. Offering regular OSHA-compliant training for your team helps keep them safe and means you’re fulfilling your obligation as an employer.
Below we’ve outlined 15 essential construction safety tips to underline the importance of proper training. Understanding these guidelines will help your team take adequate safety precautions and create a safer environment for your workers.
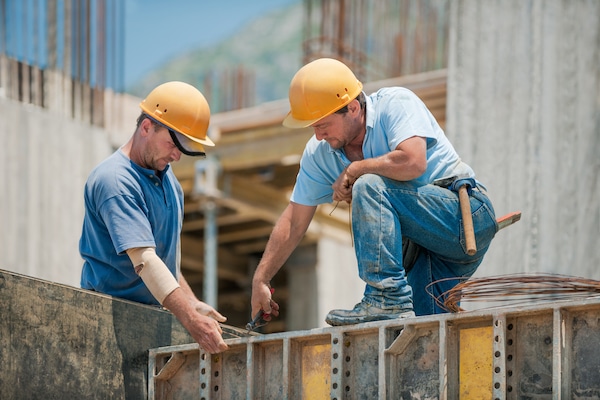
1. Provide Appropriate Personal Protective Equipment
Lack of personal protective equipment is a leading cause of construction accidents. This describes fall protection systems such as harnesses and fall arrests, but it’s also essential to ensure you’ve covered the basics. This includes:
- Hard hats. A hard hat is mandatory for anyone working on construction sites. Falling objects are a permanent risk, and head protection is a compulsory layer of defense. Hard hats can reduce the risk of severe injuries and even save lives – they’re essential and affordable protective gear.
- Protective goggles. Wherever workers might be exposed to flying particles or heat (e.g., on a welding project), face protection such as goggles should always be worn and provided by the employer. Employees are at risk of life-changing injuries such as blindness caused by flying debris, and the risk isn’t worth taking compared to the low cost of safety goggles.
- Appropriate footwear. Durable, non-slip footwear is vital on any job site. Employees working around electrical hazards also need footwear that meets electrical safety regulations. High-quality, well-made footwear also reduces the risk of impact damage and is critical to ladder safety.
- High-visibility clothing. High-visibility clothing is mandatory on all job sites. It enables employees to keep an eye on who works in the vicinity and provide hazard communication wherever necessary. One of the best ways to stay safe on a construction site is clear communication – appropriate clothing makes this much easier.
Ensuring that all employees wear PPE is a critical responsibility of employers. Workers should be trained to know what personal protective equipment should be worn on any given construction site and should be able to ask for extra safety equipment wherever necessary.
2. Maintain a Clean, Orderly Workplace
The typical job site isn’t considered a pinnacle of cleanliness, but cleanliness and order are extremely important in the construction industry. When using MEWPs (mobile elevating work platforms), ensuring that the platform is kept clean and free from trip or slip hazards is integral to any proper safety program.
Equipment should always be cleaned following bad weather to prevent slips. This is important for platforms and equipment like metal ladders or any raised environment where slipping might put workers’ safety at risk.
Keeping tools and the working environment in order is also essential. Devices should always be returned to their proper place following use. If a job involves working around power lines or other dangerous environmental features, special attention should be paid to keeping high-risk areas neat and orderly.
3. Inspect Equipment Daily
Daily inspections should be performed on aerial lifts, scissor lifts, and all heavy machinery used for construction. A trained operator and cover areas like should carry out the assessment:
- The platform: this should be clean and free from trip or slip hazards.
- The guardrail: loose or faulty guardrails should be reported instantly.
- The lifting mechanism: this should be tested before any operators can stand on the platform when it lifts.
- The emergency controls: emergency fail safes are a vital extra precaution when using heavy machinery. They should be tested every day.
Ensuring that construction staff knows how to perform daily tests speeds up the workflow and provides workers the highest level of safety at all times.
4. Keep an Eye Out for Fall Hazards
Loose guardrails are just as much of a hazard on fixed-raised areas (such as roofs) as they are on MEWPs. Likewise, trip hazards near the edges of raised work surfaces can cause fatal accidents if not identified and removed – if something can cause an accident, it will eventually. Never risk it.
Falls are one of the leading causes of fatalities and life-changing injuries in the construction industry. Any work surface more than four feet above the ground should be subject to daily health and safety inspections to keep fall hazards out of the way. Furthermore, employees should know that routine inspections don’t guarantee safety – taking the initiative to identify and remove hazards whenever they appear is always essential.
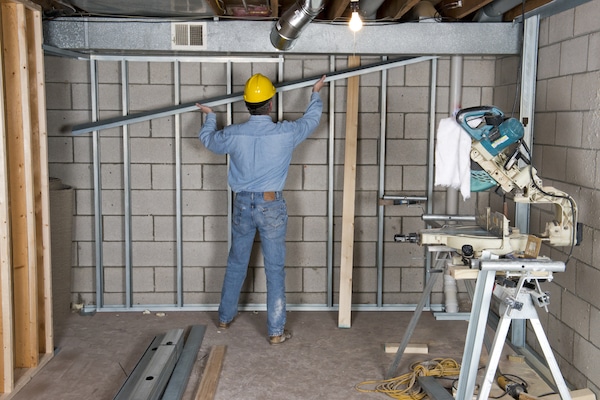
5. Don’t Risk Using Malfunctioning Equipment
Any tool or machinery that isn’t functioning correctly, from power tools to heavy equipment, shouldn’t be used. It should immediately be put to one side, labeled as faulty, and maintenance should be scheduled as soon as possible.
Using malfunctioning equipment exposes construction workers to various hazards, from the risk of electric shock to compromised protective gear. If a pair of gloves used for electrical work has developed a hole, they need to be replaced. A hammer with a loose head should be tagged and put aside. Essential safety tips like these prevent so many avoidable accidents.
6. Know Your Work Environment
Construction workers should be trained to identify all areas of a work environment that present a risk and know what safety devices and protective equipment (e.g., face protection) will be needed. Blind spots should be identified before work begins, and high-risk areas like overhead lines should be marked.
Construction projects take place in diverse environments and change their environments, exposing new risks as work progresses. The best way to prevent accidents is to conduct an assessment at the start of each day and ensure that all employees understand where they need to stay safe.
7. Use Fall Protection Systems
One of the most vital construction safety tips is to use fall protection systems suitable to the environment. This might include:
- Fall prevention devices like guardrails. These minimize the risk of workers falling when they move to give themselves more room or lose their footing.
- Protection systems. Safety net systems are essential when using an aerial lift or wherever there’s a high risk of workers suffering a long fall.
- Fall arrest systems. Protective harnesses and appropriate anchor points should be in place for any construction environment with a risk of falling more than 6 feet.
Even simple head protection like a hard hat can make a huge difference. Workers should know which safety measures are appropriate whenever working at a height and have access to the appropriate gear and safety training.
8. Label & Store Hazardous Materials Safely
If hazardous materials are being used on-site, these should be kept separate from construction work wherever possible and stored in a safe location. These types of potential hazards should be labeled and handled with extreme caution.
Workers should be provided with full safety training regarding storing and handling dangerous chemicals if they work in an environment containing these risks. These safety topics aren’t always included in construction-specific safety training materials, so it’s worth investing a little extra in extra training.
This mitigates the risk to your employees and reduces the chance that corrosive or flammable materials could cause property damage if they’re not stored and appropriately protected.
9. Wear Seatbelts
It bears repeating as many times as necessary: one of our top construction safety tips is to wear a seatbelt whenever operating any vehicle or machinery. Whether lifting heavy objects, raising a platform, or simply moving around, there’s always the chance that a vehicle will overturn or need to come to a sudden stop.
A seatbelt can protect you against life-changing injuries and is a mandatory part of any construction safety program. Ensure that employees understand and respect the need to use a seatbelt on a construction site – it should fit snugly and pull tight when required. It’s so basic, but it saves lives. We also have some other driving specific safety tips you should check out as well.
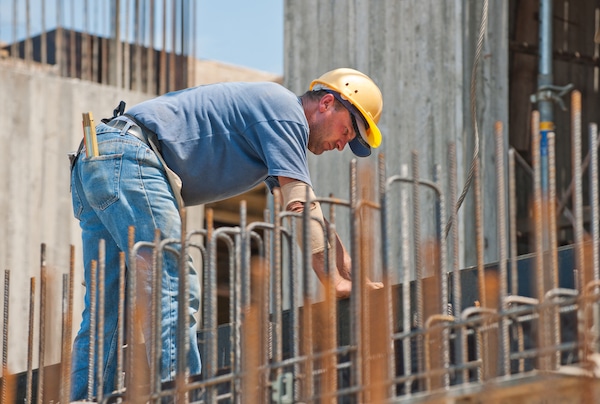
10. Provide Proper Safety Training for Construction Workers
Workers should be provided with safety training covering all hazards they’re likely to face and the equipment they’ll use. The training should be specific to the role, e.g., an aerial lift operator will need extra training if they operate a scissor lift. An experienced construction worker who hasn’t recently been trained to work safely around power lines needs to update their knowledge on these hazards – complacency invites injury.
Employees should ensure that all safety topics are accounted for. Training materials should be OSHA-compliant and standardized – training videos are perhaps the best way to achieve this. They’re a cost-effective way to ensure construction site safety practices are followed at all times, and knowledge is tested after each module with a short test.
11. Schedule Routine and Annual Inspections for Machinery
Besides the daily operational inspection, heavy machinery used in the construction industry should receive routine inspections. An in-depth review by an operator should typically be scheduled every three months or so, or more frequently if the equipment is being used often.
Meanwhile, OSHA mandates that equipment like MEWPs receives an annual full inspection from a qualified engineer. While these inspections aren’t cheap, they cost less than the fines companies incur for ignoring OSHA’s guidelines and significantly less than the lawsuits employers can face when they fail to follow basic safety procedures and have their equipment inspected by a trained professional.
Heavy machines become hazards when they’re not properly maintained. Make sure you’re keeping yours in shape.
12. Document Issues and Fixes
It should be documented whenever an issue is noticed, and the relevant equipment should be taken out of service. Likewise, when a fix is issued, and the equipment can be used again (or replaced), the previous note should be signed off as actioned.
This takes almost no time and is an excellent practice for construction workers to get into. It ensures that the right equipment can be identified and passed or failed as “fit for purpose” whenever needed and that nothing slips through the cracks.
13. Use Warning Signs
Safety signs are another cost-effective and advantageous way to improve safety on a job site. Warnings should be in place for areas with slip hazards (i.e., wet floor signs), but also to cover hazards such as potential falling debris and electrical hazards.
These are also helpful when it comes to controlling pedestrian traffic. Not all injuries on construction sites happen to workers – sometimes, a member of the public is injured because they didn’t realize work was taking place. If the area wasn’t properly signed, this could lead to more fines and lawsuits for your company.
High-risk areas where dangerous chemicals or materials are being stored or moved should also be denoted with clear signs. This indicates to workers what additional protection they might need if they’re entering a high-risk area, even if that’s just a pair of safety goggles.
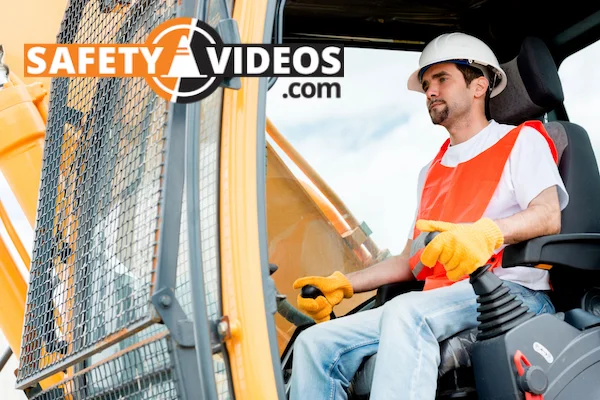
14. Don’t Let Untrained Workers Operate Machinery
Employees should be able to determine whether they should use a type of machinery based on their training. Still, supervision should also be in place to ensure that untrained workers never operate equipment they’re not trained to use.
This type of oversight typically occurs with machinery that is seen as easier to operate or low-risk, e.g., it’s more likely that an untrained employee will drive a forklift than try operating a crane. However, the safety risk is exceptionally high, whatever equipment is used.
Staff should feel comfortable identifying and reporting when these breaches occur. There are two common cases when an untrained worker might try using equipment they should be using:
When the time pressure of getting on with a job causes workers to “take matters into their own hands” and work by lower safety standards
When proper safety standards aren’t in place, untrained employees can “have a go” at using dangerous equipment without caution.
Either of these instances puts construction operatives at risk and should be reported immediately.
15. Use Regulatory Compliant Training Materials
When choosing training materials for your team, you must select OSHA compliant training materials that include a knowledge test at the end of the module. Materials that aren’t compliant with OSHA might miss key points, which will put your workers in danger. You’ll also risk fines if OSHA discovers you’re using low-quality construction training materials.
OSHA inspects construction sites regularly to ensure that proper safety procedures are followed. Whether it’s an untrained employee repairing damaged electrical cords or workers missing functional safety gear like a self-retracting lanyard on an aerial lift, the best way to ensure that your workplace is OSHA-compliant and as safe as possible is to use high-quality training materials.
Well produced and complaint training videos are simply the best way to ensure that your staff’s knowledge of hazards and best safety practices are up-to-date and complete. They’re cost-effective, and videos are available for a vast range of specialist topics within the construction sector. Furthermore, high-quality training videos come with a thorough knowledge test at the end of the module to ensure that your workers understand what they’ve been shown.
FAQ
What are 5 basic safety rules?
Five good rules of thumb for a safe workplace are:
- Never use equipment you’re not trained to use
- Inspect equipment and your environment every day
- Ensure that areas containing hazards are adequately signed
- Report unsafe behavior whenever you see it
- Always wear appropriate PPE – this includes your seatbelt!
Safety is a blend of common sense and in-depth training. Construction workers typically possess plenty of the former, but it falls on the employer to ensure that this is backed up with OSHA-compliant training.
What are some important tips for construction safety?
Remembering the basics is essential for safety on a construction site. The little details like ensuring that everyone is wearing a hard hat at all times and that PPE such as protective goggles is available whenever needed make a huge difference.
For employers, ensuring staff understands the importance of all safety aspects creates a more harmonious and efficient workforce. Employees are less likely to care about safety measures if they arrive in a work environment and observe that rules are poorly enforced or find that they’ve received inadequate training.
Remember that construction sites are full of dangers, whether that’s a wrench falling from a high platform or having to work around live power lines. Respect for the work environment starts at the top: employers must instill good practices into their team at every level. This all begins with having high-quality, OSHA-compliant training materials available.
What are the 7 safety tips?
There’s no “set” number of good safety tips. The more areas you can identify, the better protected your workers will be. While it’s helpful to summarize critical points in numbered lists (as above), the most important thing is for employees to understand every potential hazard in their work environment and what they can do to mitigate these risks.
Keeping Construction Sites Safe
By following the construction safety tips outlined above, you’re giving your workforce the best possible protection.
Backing up common-sense decision-making with thorough OSHA training videos is the best way to ensure that your workers never face unnecessary risks in their workplace. It’s also the best way to protect your business against fines and lawsuits for violations.
Consider the range of training materials available, think of specific training employees at your workplace require, and keep your workers safe with up-to-date knowledge and training.