Ventilation in Hot Work Areas – What Is Required?
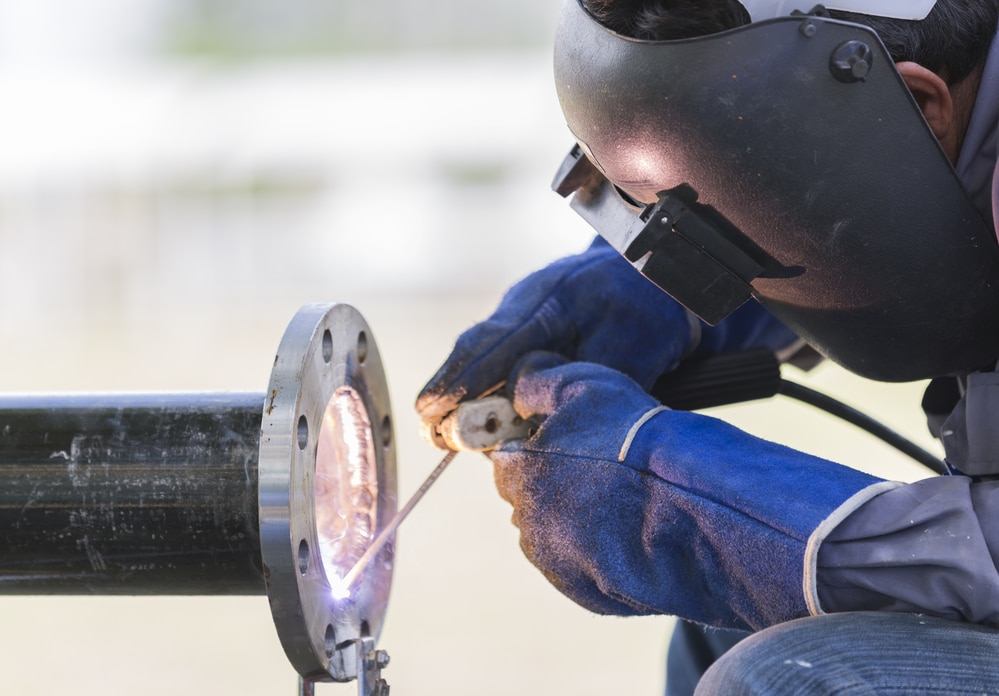
Electric shock, radiant energy, and severe burns aren’t the only heat-related operations hazards. Hot work ventilation ensures worker health and safety during potentially dangerous soldering, brazing, welding, or cutting operations.
Such operations release harmful fumes and flammable gases. Employees risk dangerous working conditions and negative long-term health effects without adequate local exhaust ventilation or mechanical ventilation.
Keep reading for a full rundown of the requirements for hot work ventilation systems. Also, we have a hot work training video you can use for your employees.
Why Is Ventilation Important?
In confined spaces where hot work is being performed, ventilation systems perform the following functions:
- Removing contaminated air and welding fumes from the worker’s breathing zone
- Preventing flammable gases from accumulating
- Maintaining appropriate oxygen levels within the welder’s breathing zone
Regular inspections and maintenance must be conducted to ensure all ventilation systems are functioning properly. If the system is damaged or insufficient, all work in the area must be suspended until the problems are resolved. Also, making sure your employees use the proper PPE when doing hot work is critical to their safety and to the compliance of your company with OSHA standards.
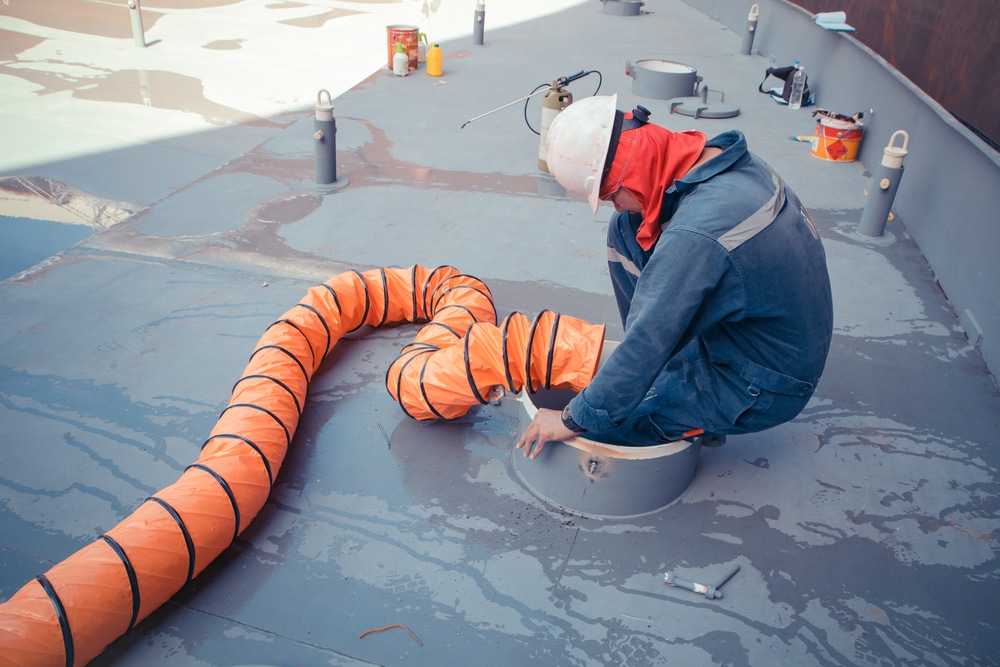
Types of Hot Work Requiring a Ventilation System
Cutting and welding operations and other allied processes involve many materials and substances, some of which release toxic fumes and gases.
Some of these materials include:
- Metals coated with lead-bearing materials
- Lead base metals
- Fuel gas
- Zinc-bearing base and filler metals
- Chromium-bearing metals (also metals coated using chromium-bearing materials)
- Cadmium-bearing filler materials
- Beryllium-containing base and filler metals
- Metals coated with mercury-bearing materials
- Welding wire with a high manganese content
- Cadmium-coated base metals or filler metals
- Zinc-bearing materials
Prolonged exposure to these materials without sufficient ventilation can cause severe health issues.
Here are four examples of hot work procedures that may expose workers to the above contaminants. All of these procedures require effective ventilation systems, especially when conducted within confined spaces.
Electric Arc Welding
Electric arc welding – also called metal arc welding – uses an electric arc to heat and join various metals.
Shielded metal arc welding is frequently used in the repair and maintenance industry. Depending on the substances involved, it has the potential to release various toxic fumes and irritants that can damage sensitive tissue and cause long-term health effects without proper ventilation.
Inert gas metal arc welding involves a higher concentration of potentially dangerous substances and byproducts. This process requires both mechanical and local exhaust ventilation in order to be conducted safely.
The arc welding process is inherently dangerous due to the tools involved. Using electrified tools and instruments always carries a risk of electric shock. This risk can be exacerbated in enclosed areas with poor ventilation since moisture is more likely to build up.
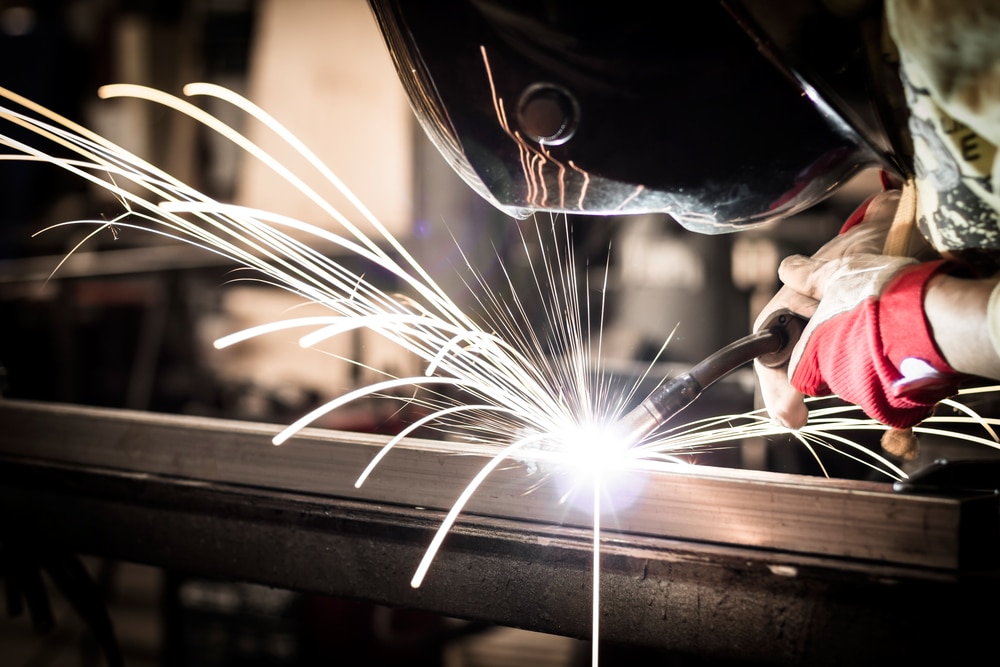
Gas Welding
This process uses a flame created by burning acetylene and oxygen. The chemical reaction between these two compounds can produce large amounts of carbon monoxide over a short period of time, so ventilating the work area is of the utmost importance.
As with other types of welding, gas welding occasionally exposes workers to toxic metals that are alloyed with the ones being welded.
Plasma Arc Cutting Operations
Plasma cutting uses superheated ionized gas to cut and shape electrically conductive material into the desired design. It’s used frequently in fabrication because it’s budget-friendly and highly cost-effective – especially compared to water jet and laser cutting.
Different gases are used in plasma cutting depending on the material’s thickness and type. Some of the most common include:
- Compressed air
- Oxygen
- Nitrogen
- Mixtures of argon and hydrogen
Nitrogen is considered a hazardous substance in workplaces because it can replace oxygen in the air at high concentrations, causing lightheadedness, loss of consciousness, and death.
Oxygen cutting is used to shape stainless steel and other conductive metals. The fuel gas used in this process varies depending on the scale of the job and the type of metal being cut.
A small 4 x 4 cutting machine requires 3,200 to 3,600 cubic feet per minute airflow to remove dangerous fumes. Workers performing plasma cutting shall be protected by efficient ventilation systems of the appropriate size for the size of the cutting machine being used.
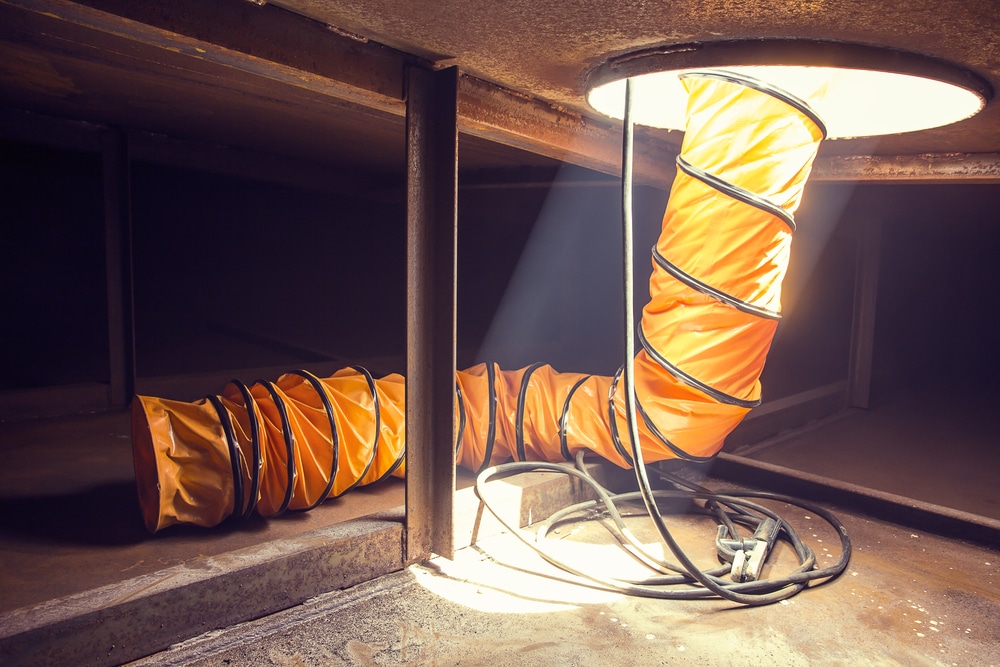
Ventilation Requirements for Hot Work Operations
The Occupational Health and Safety Administration mandates that either mechanical ventilation or local exhaust ventilation, meeting the administration’s minimum safety requirements, be present in any confined space where hot work is performed. All employees shall be protected from the dangerous byproducts of general welding and cutting equipment.
Before any welding or cutting operation takes place, any surfaces prepared using chlorinated solvents must be thoroughly dried. The ultraviolet radiation produced by welding and other processes decomposes the chlorinated hydrocarbons within these solvents, creating toxic gases that can lead to rapid asphyxiation in enclosed spaces.
Chlorinated solvents should also be kept at least 200 feet from any exposed arc during arc welding or cutting.
Employees exposed to the same atmosphere as the burners or welders shall be protected using the same methods. These methods might include personal protective equipment as well as local exhaust ventilation.
3 Types of Ventilation for Confined Spaces
OSHA recognizes three methods of ventilating enclosed areas: local exhaust, mechanical, and natural ventilation.
Local Exhaust Ventilation
Local exhaust systems consist of movable hoods that the burning, welding, or cutting operator should place as close to the hot work operation as possible. It’s the preferred method of filtering out the fumes, vapors, dust, and gases produced during gas welding and other heated operations.
Effective local ventilation requires functional equipment that is kept in excellent repair. Additionally, workers must know where to place the hoods to ensure the local exhaust ventilation system works as designed.
If highly toxic substances such as beryllium-containing base metals are present, local exhaust systems should be paired with mechanical ventilation systems and personal protective gear for maximum safety.
Mechanical Ventilation
General mechanical ventilation includes any machine or device that improves air quality within a given space.
Examples of mechanical ventilation systems include:
- Ducts
- Fans
- Heat-to-air exchangers
Mechanical ventilation devices need frequent maintenance and inspections to continue functioning properly.
Note that negative pressure ventilation should never be used to ventilate areas where flammable gases are present because it dramatically increases the risk of ignition.
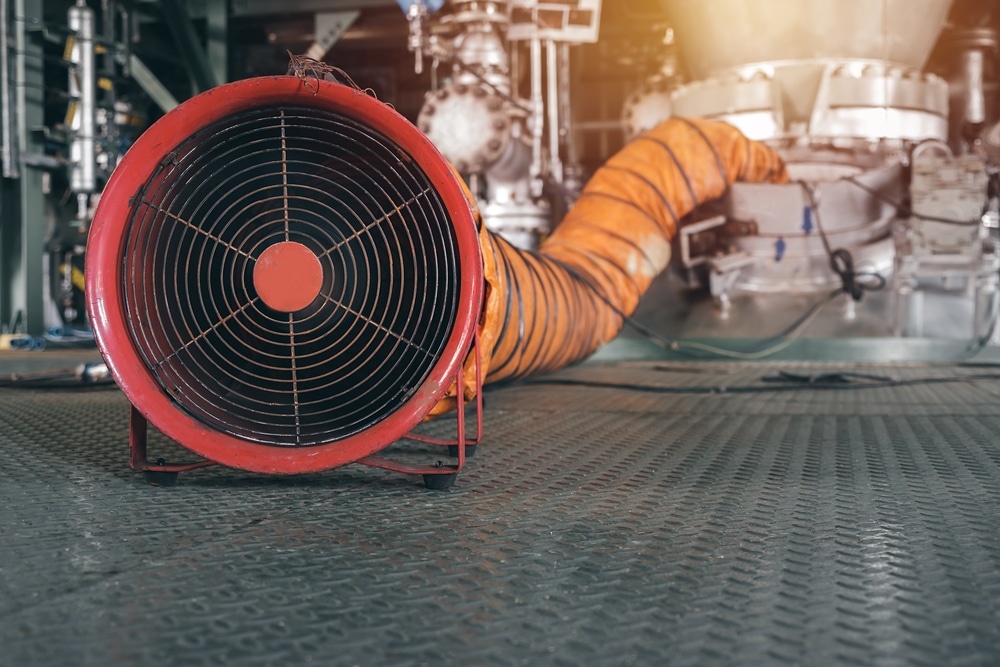
Natural Ventilation
Ventilating a workspace naturally involves improving the space’s air quality using non-mechanical means. Opening windows and doors to allow fresh air into the workspace is an example of natural ventilation.
While natural dilution ventilation can help improve airflow somewhat, it is considered the least effective. Hot work in a confined space should always be paired with targeted mechanical and local exhaust ventilation systems.
Pairing Hot Work Ventilation With Personal Protective Equipment
While ventilation is necessary for any hot work performed in a confined space, it’s insufficient to ensure worker health and safety. All workers shall be protected more effectively using proper safety gear during welding and cutting operations.
The type of safety gear appropriate for a given task depends on the nature of the work being done and the type of confined space employees will be working inside.
Self-contained Breathing Apparatus
Even when welding and other heat-related operations are conducted in the open air, workers should wear adequate face protection to shield their eyes, noses, and throats from dangerous contaminants.
Ensure all protective face and headgear fits well and is free of leaks, and avoid using welding helmets or face shields that have highly reflective surfaces.
In enclosed spaces, workers shall be protected by self-contained breathing apparatuses in addition to sufficient ventilation systems. These devices allow workers to breathe if the levels of carbon dioxide and other gases that can cause asphyxiation are elevated within the work area.
Self-contained breathing apparatuses are designed for short-term use. If workers are exposed to dangerous fumes for an extended period, air-supplied or combination respirators should be used instead.
Safety Belts
Safety belts can help pull workers out of confined spaces if the hot work ventilation fails or conditions within the work area become dangerous.
Before beginning welding and cutting procedures in enclosed spaces, an attendant must be trained in a comprehensive pre-planned rescue procedure. This attendant must be stationed where they can always observe the workers and workspace.
The attendant will be responsible for executing rescue operations at a moment’s notice. They must constantly communicate with the welding and cutting team to ensure issues are reported as soon as they occur.
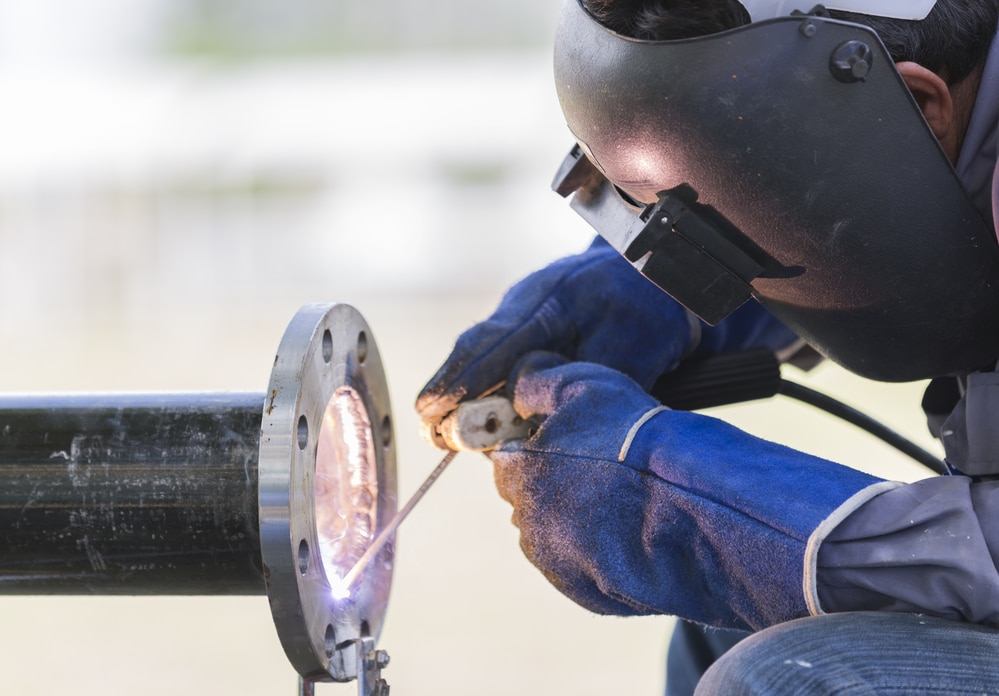
The Dangers of Poor Ventilation in a Confined Space
Failing to adequately ventilate an enclosed space before welding or cutting can have disastrous consequences for everyone in the area.
Here are a few of the hazards workers face when performing hot work in a poorly ventilated area.
Electric Shock
Cutting and welding operations make extensive use of electrified tools. Consequently, electrical burns and electric shock are two potential hazards of these operations.
Workers are likely to perspire in a poorly ventilated space while performing their labor – particularly when those labors involve working with hot materials.
Sweat’s salt content makes it a powerful conductor of electricity. If welders perspire while working, they dramatically increase their risk of electric shock and other electricity-related injuries.
Other sources of moisture, including high humidity, can increase shock risk in an enclosed space. Ventilation helps prevent these dangerous conditions by keeping the area cool and dry.
Contaminated Air
Bad air is one of the key reasons why ventilating enclosed spaces is of the utmost importance. Harmful gases can quickly fill a small space, making it harder or even impossible for workers to breathe.
Keeping the workspace well-ventilated removes toxic fumes from the breathing area and reduces the risk of respiratory issues and asphyxiation.
Exposure to Toxic Materials
Employees exposed to dangerous levels of fuel gas and other hazards are at risk of developing serious health effects. The eyes, nose, lungs, and respiratory tract are all affected by contaminants in the air.
Toxic metals like beryllium, arsenic, and silver are often alloyed with commonly welded metals such as copper and aluminum. Long-term exposure to these metals can result in the following:
- Chronic cough
- Fatigue
- Weakness
- Severe weight loss
- Shortness of breath
Personal protective gear and efficient ventilation are needed to avoid exposing workers to contaminants and hazardous byproducts.
Fires
Without proper ventilation, flammable gases can build up quickly in a confined space, dramatically increasing the risk of fires and explosions. This risk is increased further if combustible materials such as paper or wood shavings are present within the workspace.
Reduce the risk of fire hazards by keeping all confined work spaces well-ventilated and keeping the floor clear of any combustible substances or materials.
Open Air Ventilation
Even outdoors, mechanical ventilation may be necessary to divert fumes and toxic gases away from the workers’ breathing area.
Workers should still wear personal protective equipment when performing hot work in open spaces. Appropriate PPE may include filter-type respirators or air-line respirators, depending on the toxicity of the materials being used.
Final Thoughts
Hot work ventilation is crucial to worker safety, especially in confined spaces where airflow is more likely to be affected by toxic fumes and byproducts.
All workers should have access to respirators and other personal ventilation systems. All mechanical and local exhaust ventilation systems should be tested before use.
Following OSHA’s guidelines regarding proper ventilation protects workers from immediate hazards and the dangerous long-term health effects of breathing contaminated air.
Frequently Asked Questions
Under OSHA’s regulations, a qualified individual must test the atmosphere and deliver the all-clear before any hot work can commence within a confined space.
Yes, always. The type of system required depends on the materials workers use and whether the workspace is enclosed or open. In some cases, multiple types of ventilation should be used, including both local exhaust and mechanical. Workers should also wear respirators and other PPE as an added measure of security.
There are specific OSHA standards regarding ventilation in various sectors, including construction, maritime, and general industry.
The OSHA standard regarding ventilation in general industry is 1910.94.
In the broadest sense, ventilation involves controlling potential hazards within an interior environment using airflow. Proper ventilation should remove vapors, dust, and fumes from the air to reduce their chances of harming workers within the space.