How to Properly Inspect and Maintain Your Safety Harness
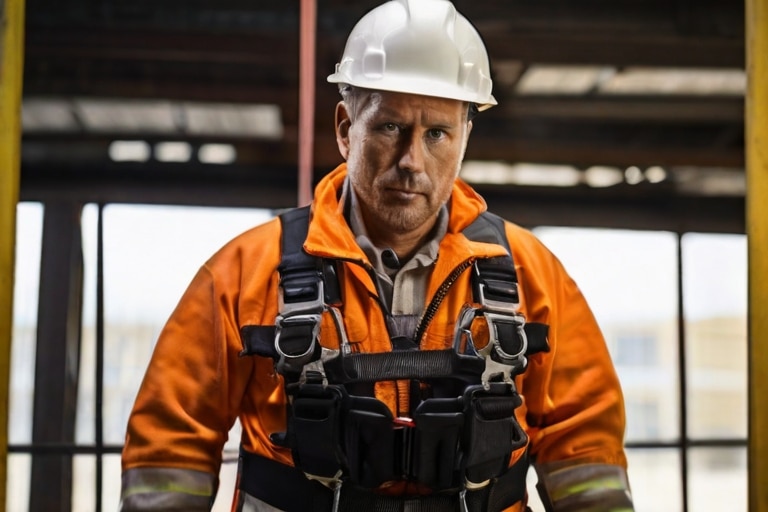
Routine safety harness inspections can be the difference between life and death for workers.
Harnesses are worn as fall protection equipment when there’s a significant risk of injury in the event of a fall. However, they’re not infallible, and if they aren’t inspected regularly and maintained by a competent person, the consequences could be dire.
This guide will cover:
- Different types of harnesses
- How harnesses work & their uses
- When to wear fall protection harnesses at work
- How to properly inspect and maintain your safety harness
- How to identify unsafe fall protection equipment
Let’s get right into it. But first, if you want to check out our video training on fall protection, we have a full course available.
What is a Fall Protection Harness?
Harnesses are safety equipment that keep workers safe when working at a height. They can operate both as fall arrest systems and suspension systems, meaning that a worker may be protected from a fall or allowed to “sit” in the air while safely suspended.
Harnesses are full-body items – they’re worn over other protective clothing. The critical feature of a harness is the dorsal D-ring – a strong metal buckle secured to both the fall arrest harness and the rope part of the suspension system. This allows workers to descend vertical surfaces safely.
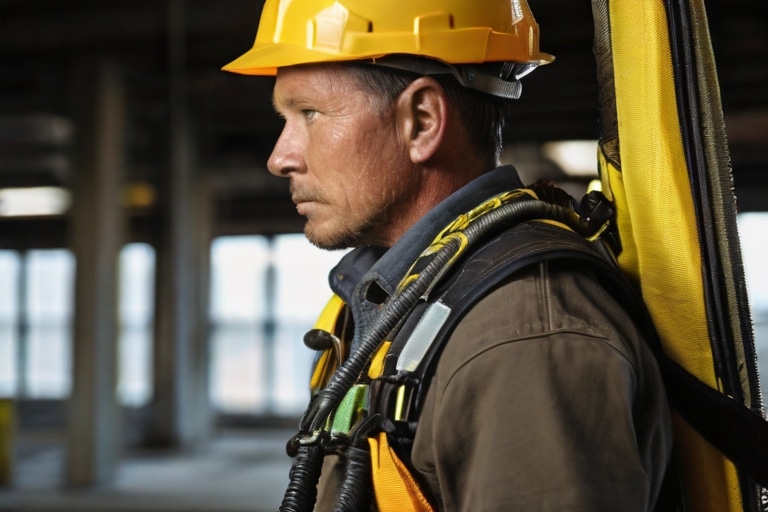
How Do You Inspect a Safety Harness?
It’s recommended that an in-depth safety harness inspection take place once per month. However, inspecting them before every use is the best practice, as with all fall protection equipment.
The formal inspection must be conducted by a competent person who has been trained to OSHA standards – this may be a worker or a supervisor. It is partly visual and partly relies on touch.
OSHA (Occupational Safety & Health Administration) advises that while you must closely examine parts such as the lanyard and webbing visually, some other defects may not be identified without feeling the equipment.
We’ll cover the key elements of safety harness inspections below.
How Do You Take Care of a Safety Harness?
Maintenance of fall protection gear is mostly preventative. The best practices for storing fall arrest harnesses are described below, but the most important thing is keeping safety equipment in a clean, dry place and hanging it rather than leaving it on dusty or dirty surfaces.
Maintaining harnesses is quite easy and doesn’t require specialist equipment. Harnesses that have endured years of wear and tear usually need to be replaced, but their lifespan can be extended for years with simple cleaning and storage measures.
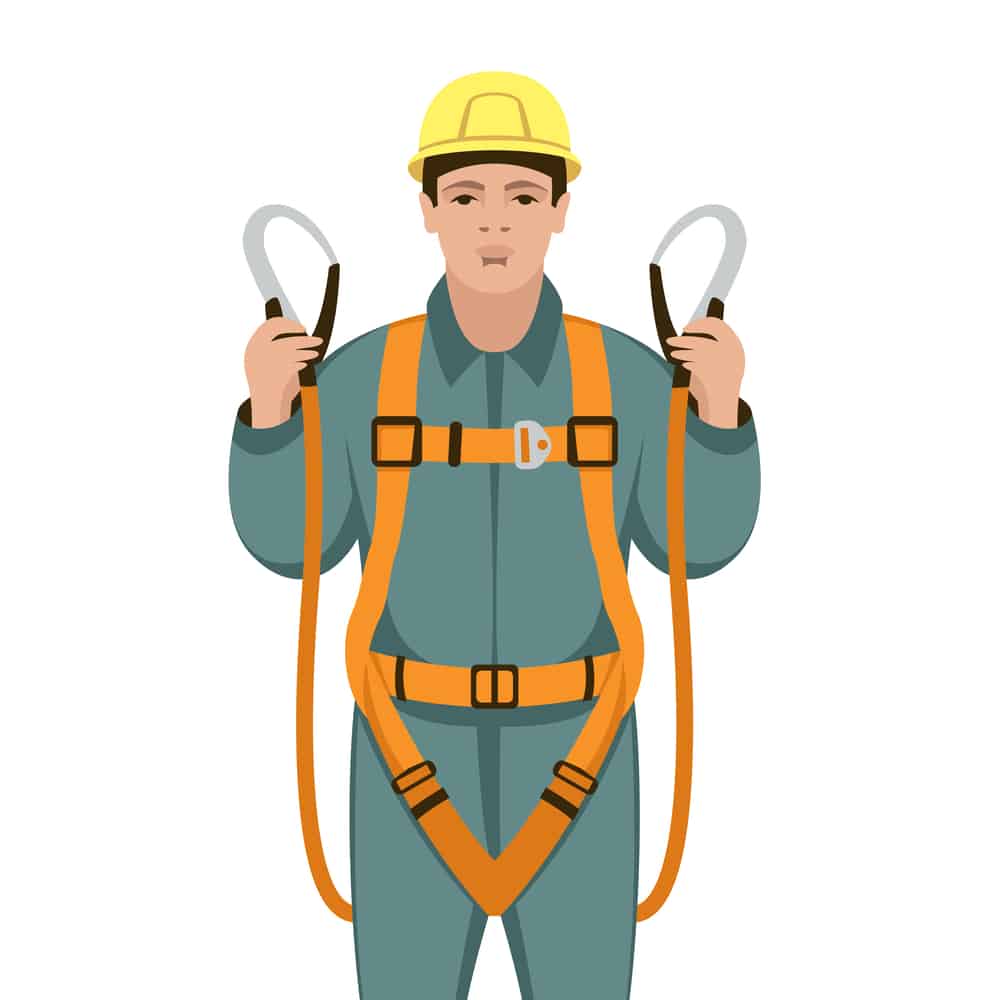
Uses of a Full Body Harness
A fall protection harness is typically used when workers are operating at a height. OSHA requires fall protection equipment to be in place when workers are operating at the following heights:
- 4′ – general industry operations
- 5′ – shipyards
- 6′ – construction industry operations
- 8′ – long shoring
Fall protection at lower heights of just a few feet may be guard rails or PPE such as hard hats – harnesses are not necessarily required at these low heights. Employers should be mindful of the unique circumstances of their work sites and use common sense to judge whether a safety harness is necessary.
A good rule of thumb is that if it feels unlikely that the worker will not be able to land on their feet comfortably, a harness should be worn. This could be because they would be falling from a significant height or because they’re working in an awkward position and wouldn’t be able to adjust their body if they fell (e.g., working on a sloped roof).
While Descending a Vertical Surface
Harnesses are commonly worn when workers are operating against a vertical surface. Construction workers, commercial window cleaners, and electrical professionals are good examples of workers who may have to work in these conditions.
In these cases, a fall protection inspection and proper maintenance (if necessary) should be conducted on every part of the fall protection equipment before use. This includes the harness, the self-retracting lifelines, the anchor point, any platform that may be in use, and all other components.
The straps on these harnesses should ensure that the worker can maintain a standing position or rest their feet against the surface as if abseiling. Free movement of the legs may be necessary, and a platform may also be in use which the worker should be able to stand and walk on.
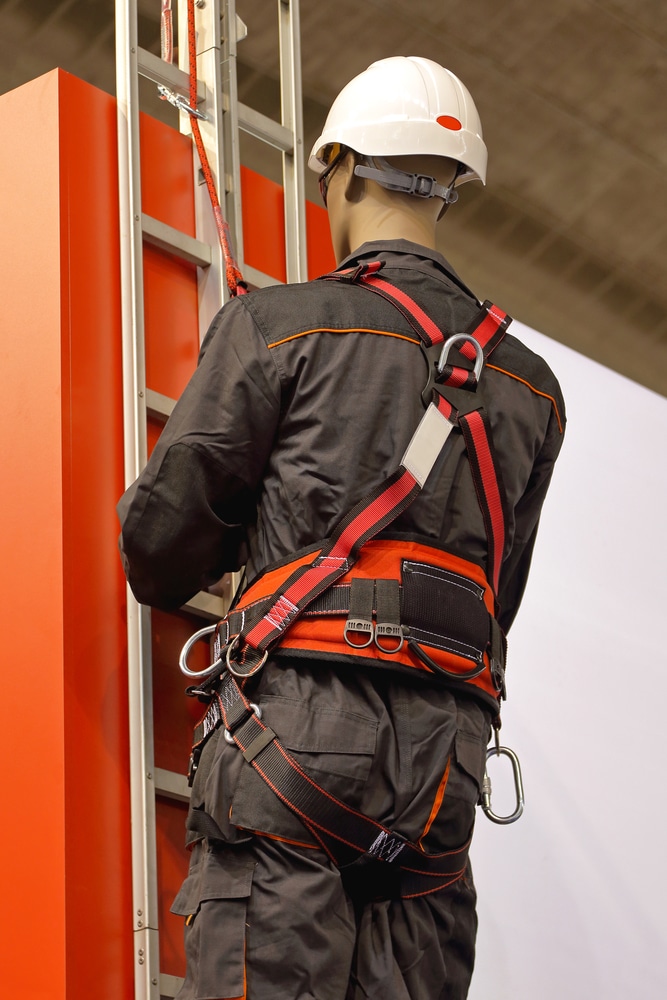
Free Suspension
A climbing or “sit” harness is commonplace in construction, rescue service operations, window cleaning, and sometimes confined space operations. The straps on this harness should keep the user secure and suspended in a sitting position.
While standing harnesses are often used for fall arrest, a sit harness is used for strategically lowering a worker when no platform is available. These harnesses typically include sturdy leg straps to ensure the individual can be lowered comfortably and securely.
Fall Protection Harness Inspection
The fall protection inspection should cover every part of the harness. The common components of harnesses are outlined below, but if any item of fall protection equipment has additional components, these should also be checked according to the manufacturer’s instructions (these should be presented on a legible tag).
The manufacturer’s requirements should always take precedence over generic advice. This ensures that companies using harnesses are not held liable if the equipment fails.
A safety harness inspection should be conducted by a competent person, which may be either the trained employee who is about to use the equipment or a supervisor.
Stitching
Stitches on the chest strap or leg straps can be pulled loose or severed due to repeated use. They may also be damaged by contact with rough surfaces or sharp edges – this may occur during use or due to poor storage.
A competent person should inspect the stitching on the lanyard for torn or severed threads. Loose stitches can be pulled through when stressed, leading to potentially disastrous consequences. Damaged stitches should be repaired, or if this isn’t possible, the equipment should be replaced.
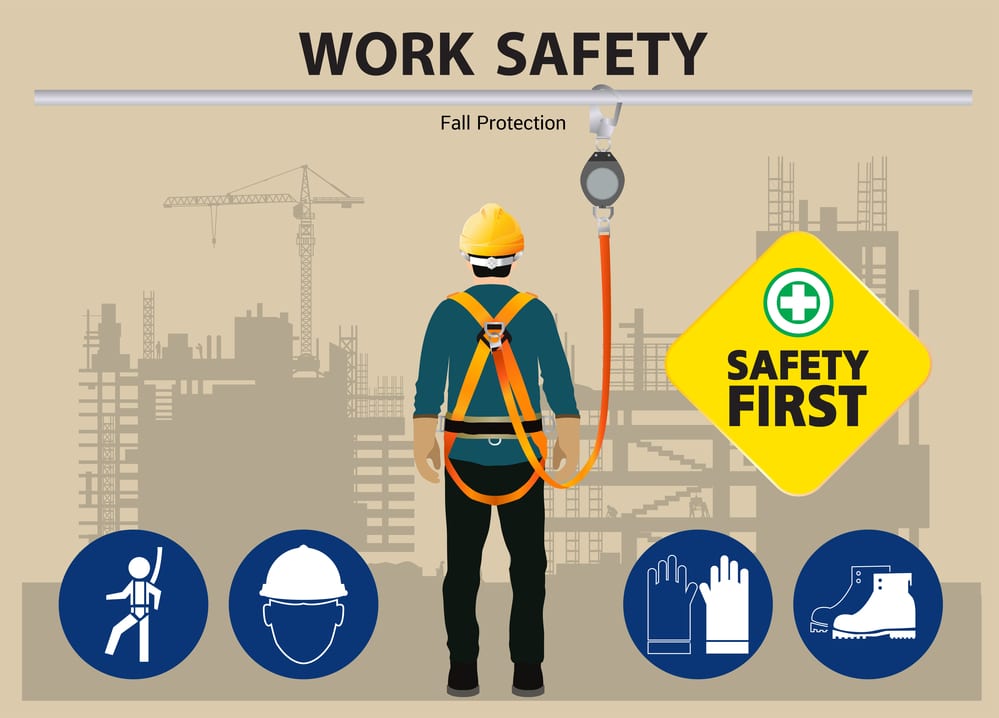
Webbing
The webbing should be inspected both visually and with touch. The webbing should be stretched, which will expose damaged areas.
If the webbing isn’t properly working, the harness should be removed from service and returned to the manufacturer or replaced. Excessive wear to the webbing reduces the harness’s ability to do its job and can put the worker in danger.
Belt Ends
Damage to the belt ends may occur due to excessive heat exposure, general wear and tear, or contact with sharp objects. The belt ends must be tight and able to hold buckles and the D-ring in place without risk of slipping.
The stitching on belt ends should be inspected to ensure they will hold strong under stress. If the belt ends are damaged, the manufacturer will advise that the equipment be taken out of service.
Buckles
The chest buckle and leg buckles may become damaged due to corrosion and rust. It’s uncommon for a buckle to be physically bent or broken, but if it has been bent, the metal’s strength will be compromised, and it should be taken out of use.
D-Rings
The D-ring is what connects the harness to the suspension system. D-rings should be inspected for rust along with all other metal components. Likewise, if the metal is bent or damaged at all, it should be returned to the manufacturer.
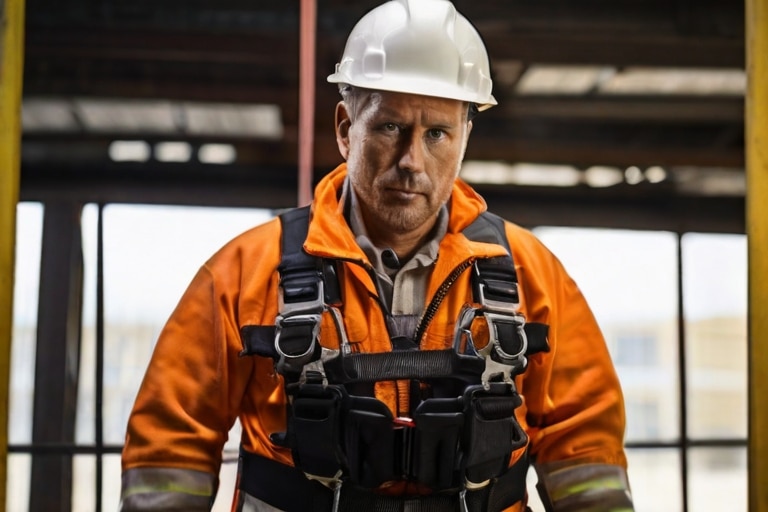
Other Visual Indicators
Some harnesses have unique visual indicators of stress or damage. Closely follow the manufacturer’s instructions when inspecting your harness to ensure that you don’t miss any key signs of damage during inspections.
Fall Protection Harness Maintenance
Poor storage is one of the most common causes of damage to a harness and can compromise its ability to protect the person using it. Full training on maintenance inspections should be provided to staff.
Store in a Temperate, Dry Place
The harness can be damaged if stored in a cold or damp place. Harnesses should be allowed to dry thoroughly after use, as prolonged dampness can let mold set in and can affect the integrity of the webbing and stitching.
It’s worth performing an annual inspection of your storage facility to ensure it’s an appropriate climate for storing fall protection equipment.
Hang the Harness – Don’t Let It Sit in Dirt
A harness should always be hung. This allows it to dry properly and ensures that dirt doesn’t make its way into the material.
Dirt can degrade equipment, and rough particles can even damage stitches. If dirt is identified on a post-use harness inspection, it should be cleaned before the item is stored.
Remove Dirt & Grease with a Damp, Soapy Cloth or Sponge
Safety harness inspections should include time for cleaning. This is simple enough – soak a sponge or cloth in soapy water, wring it out, and wipe the harness clean. Non-abrasive soaps are best; there’s never any need to use bleach or other industrial chemicals, as these may damage the equipment further.
Dry Thoroughly After Washing
After it’s cleaned, the harness should be allowed to dry fully. It’s best to let it dry naturally by hanging it rather than putting it on a radiator or heated surface, as this may affect the webbing.
Once it’s dried, it may be stored as usual and should be inspected again before the next use.
Signs that a Harness is Unsafe for Use
As with any fall protection equipment, harnesses that don’t pass inspections shouldn’t be used. Here are some telltale signs that the harness isn’t safe for use.
- Torn stitches
- Webbing is discolored
- Webbing feels like it may tear when stretches
- Missing or damaged buckles
- Can’t identify the manufacturer to check their inspection instructions (the unique serial number can usually identify the manufacturer)
- Harness is dirty
- Material is torn
The Need to Take Care of Fall Protection Equipment
Companies should inspect all fall protection gear annually to ensure their inventory is up to scratch. However, the best time for an inspection is before using the equipment.
Companies that routinely inspect their safety gear are committed to keeping their staff safe and are less likely to be fined or penalized by OSHA for safety violations.
Wrapping Up
Mandating inspections by a competent person before use is the best thing you can do to ensure that any employee using a safety harness in your workplace is properly protected.
Initial safety training can be delivered through OSHA-compliant videos, backed up by in-person instruction to ensure all staff know how to carry out an inspection.
FAQ
What four things do you check on a harness?
Four of the most important parts of the inspection include:
- The webbing
- The stitching
- The D-ring
- All buckles
What are the steps for inspecting the safety lanyard?
A safety lanyard should be inspected both visually and using your hands to test the surface tension and integrity of the material. It should pass all the manufacturer’s requirements before it is approved for use.