The Evolution of Hearing Protection Devices in the Workplace
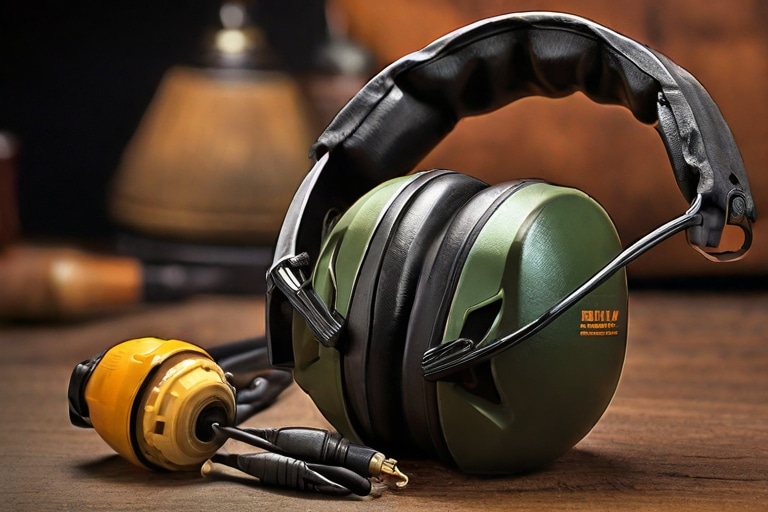
In a little less than a century, hearing protection in the workplace has gone from a bit of a joke to a major concern. Many employees wear earplugs to loud events, even off the job. And some employers spend thousands every year to keep up their hearing conservation programs.
How did we get here? When did hearing protection become mandatory? And what can the history of occupational noise controls tell us about where the field is headed?
We also offer a hearing conservation video kit to help train your employees on the ins and outs of OSHA hearing protection.
Early History
Ancient Hearing Protection
What is the history of ear protection? It probably doesn’t start where you think….
The first known reference to humans using hearing protection could be in The Odyssey, Homer’s epic poem about Ancient Greece in the aftermath of the Trojan War. To make it home safely, the hero Odysseus and his ship’s crew needed to avoid the Sirens, dangerous mythical creatures with seductive and alluring voices.
To protect his crew, Odysseus had them stick beeswax in their ears, a proto-earplug. (Wax earplugs were still the most common kind well into the 20th century.) The plugs drowned out the sounds of the Sirens, and Odysseus eventually made it back home.
For the most part, though, noise levels in the ancient and medieval world were far lower than what we’re used to today. Noise-induced hearing loss hasn’t been much of an issue for anyone.
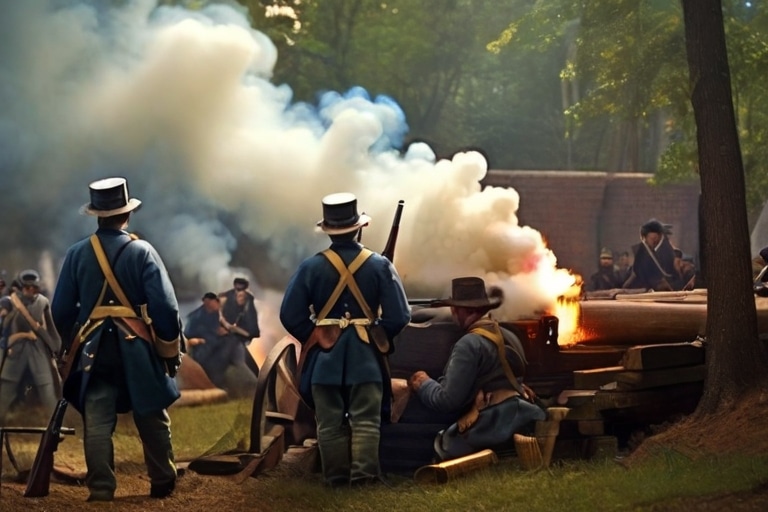
The Workplace of War
Things started to change with the development of gunpowder. Warfare, never quiet to begin with, became much louder with guns and cannons. As early as the 16th century, doctors reported seeing acoustic trauma in soldiers.
The guns only grew faster and louder throughout the 19th century. By the end of the American Civil War, a third of Union soldiers were diagnosed with hearing loss.
Devices to prevent hearing loss were patented as early as 1864. Multiple earplugs had been developed by the start of WWI. Still, many armies resisted using them – it was thought that soldiers just needed to build a resistance to loud noise.
20th Century Revolutions
It wasn’t until well into the 20th century that people started to take hearing protection seriously. The experiences of soldiers and doctors during WWI and WWII played a huge role.
As many as 20% of those receiving a disability pension for WWI French Army service had permanent hearing loss.
The American Air Force instituted the first recommended noise exposure limits in 1948 and the first enforceable noise regulations in 1958. Soldiers who experienced hearing loss from service in WWII or Korea had a much different experience than their grandfathers who served in WWI.
The military realized what workers know today – loud noises can impair situational awareness and decrease safety even beyond hearing loss.
Industrial Hygiene
In the 1950s-70s, the military’s awareness of noise-induced hearing loss intersected with a flourishing culture of industrial hygiene. By 1948, each state had its own department of industrial hygiene charged with keeping workers safe and healthy at their jobs.
In these pre-OSHA/NIOSH days, organizations like the American National Standards Institute (ANSI), the National Academy of Science, and the National Research Council developed standards and recommendations for industry to use.
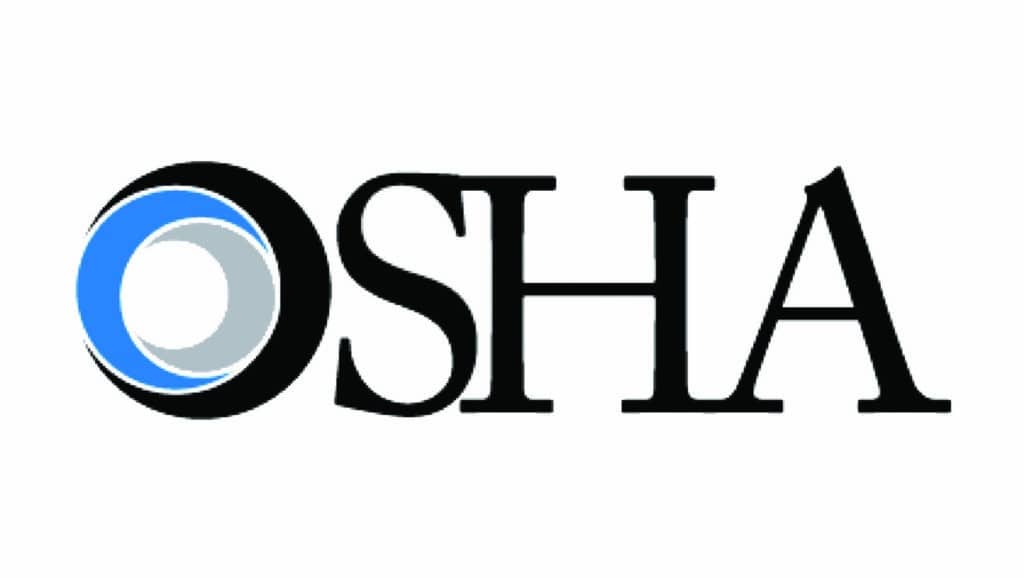
New Regulators
The Occupational Safety and Health Act of 1970 established the industrial safety system we know today.
First, employers were responsible for providing a safe and healthy workplace (the “general duty clause”).
Next, the OSH Act established the Occupational Safety and Health Administration (OSHA) within the Department of Labor. It also established the National Institute for Occupational Safety and Health (NIOSH) as an independent research body. NIOSH is currently under the aegis of the Centers for Disease Control (CDC).
In 1969 – before the OSH Act passed – the American Conference of Governmental Industrial Hygienists, a non-profit organization, developed and published a Threshold Limit for Noise. The government employed that standard first for contractors and the entire construction industry.
In 1971, OSHA and NIOSH adopted this standard (sometimes called the Walsh-Healey standard after the labor law it was first incorporated into).
Many people weren’t even unaware of noise-induced hearing loss one hundred years prior. Now, governments are making hearing protection a priority.

Technological Developments
If government regulation was one major driver for the widespread adoption of hearing protection devices, the other was technology. Options for keeping the noise to a dull roar have exploded since the 1970s.
Earplugs
Earplugs have only been around for a century and a half. Up until the middle of the 20th century, most of these plugs were wax and clay. These plugs were better than nothing but could still be uncomfortable.
In 1962, silicone earplugs were invented, and in 1972, the first “memory foam” earplugs were introduced for commercial use. However, OSHA was slow to recommend these insertable hearing protection devices.
Today, OSHA requires you to provide employees covered by a hearing conservation program with at least one choice of ear plug. A trained person must help the employee choose a device that fits and show the employee how to insert the plug into the ear canal properly. A good fit is necessary in order to achieve the best hearing protector attenuation.
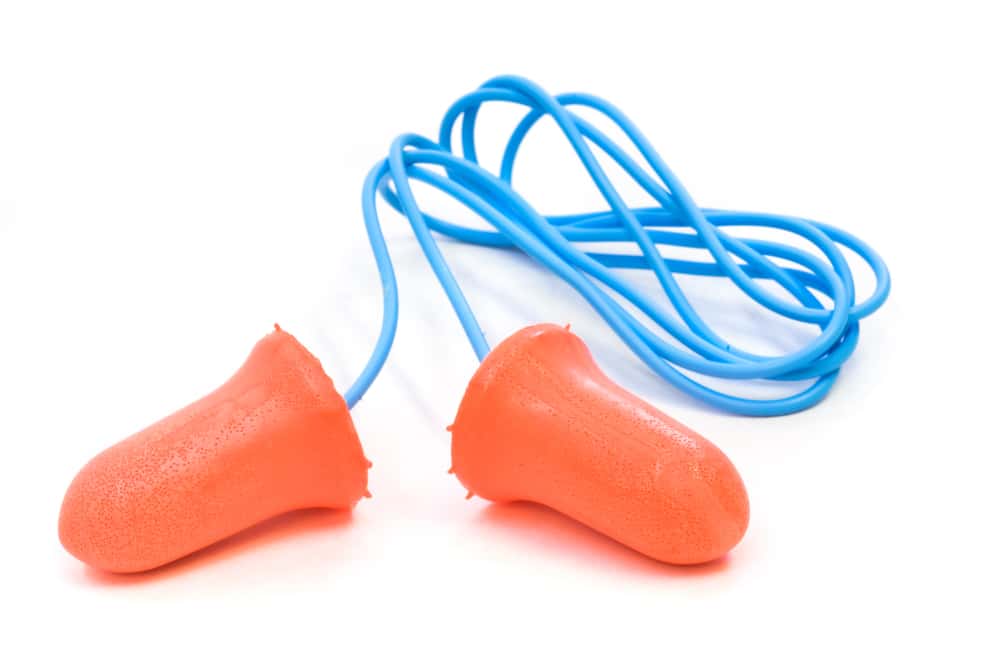
Over-Ear Protection Devices
OSHA used to consider over-ear protection as the gold standard. However, these days, we understand that both earplugs and ear muffs can be appropriate protection when worn correctly.
Over the years, ear muffs have become more comfortable and protective. Still, ear muffs must be properly fitted. Small differences in fit (for example, wearing ear muffs over glasses) can make a big difference in field attenuation – correction factors can be above 25% for some devices.
Many workers may also find it harder to wear ear muffs for long periods of time.
But technology has transformed ear muffs, too. High-end models incorporate Bluetooth technology, allowing workers to communicate with hearing protectors. Some models also allow workers to stream their own music.
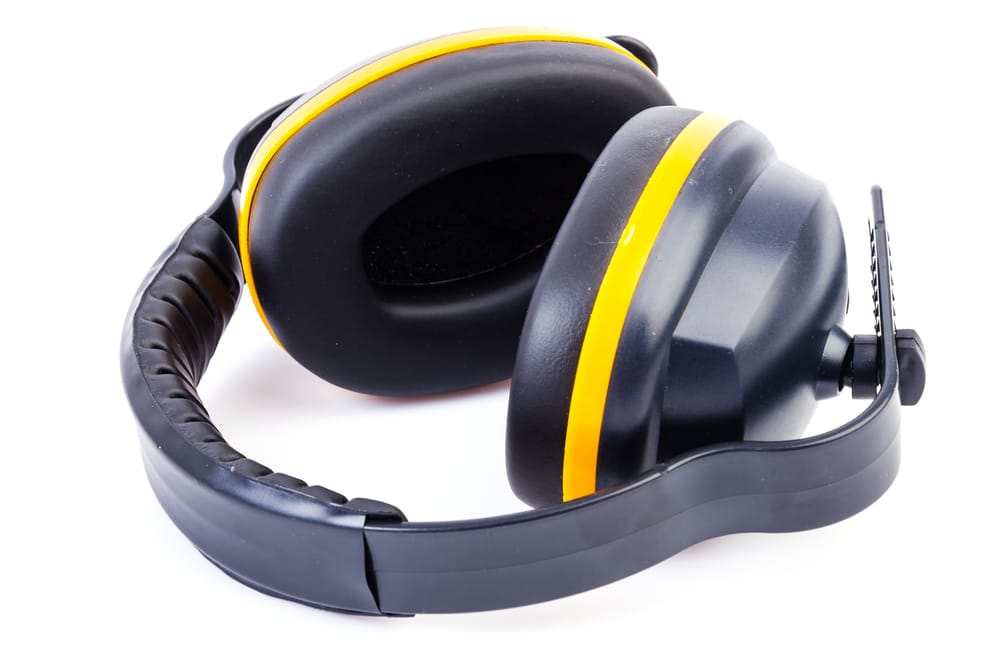
Noise Control Engineering
Before you sign off on buying a significant number of fancy ear protection devices, OSHA wants you to look at other ways to reduce the workplace’s noise level.
Taking a look at the hierarchy of noise controls in the workplace can help you find better options:
- Elimination – can noisy devices be engineered out in future designs?
- Substitution – can you buy quieter tools or use a different process that’s less noisy?
- Engineering controls – these can include putting a noisy device in a distant corner of a factory, installing sound-dampening materials, or creating a soundproof booth for employees to work from.
- Administrative controls – Changing work practices can also help protect hearing. Can you adjust production schedules so too many noisy tasks aren’t done at once? Can you provide employees with opportunities for downtime from noise?
If feasible engineering and administrative controls haven’t brought noise levels down below the limit, the employer must provide a selection of hearing protectors. A good program would also develop baseline audiometric testing so that progress on noise reduction can be measured, tracked, and calibrated.
Legal Developments
Our current regulatory system places responsibility for hearing protection in the hands of several agencies. Though there is some overlap, each agency has its own area of responsibility.
OSHA Regulations
OSHA was established by the OSH Act of 1970. The agency was charged with “ensuring] safe and healthful working conditions” through education and training. OSHA can also create and enforce binding regulations.
From an industrial hygiene and safety perspective, OSHA is the main agency you have to think about.
OSHA currently says that occupational noise exposure should be at or below a time-weighted average of 85 dB over an 8-hour day. This is slightly lower than the 90 dB limit the agency originally used.
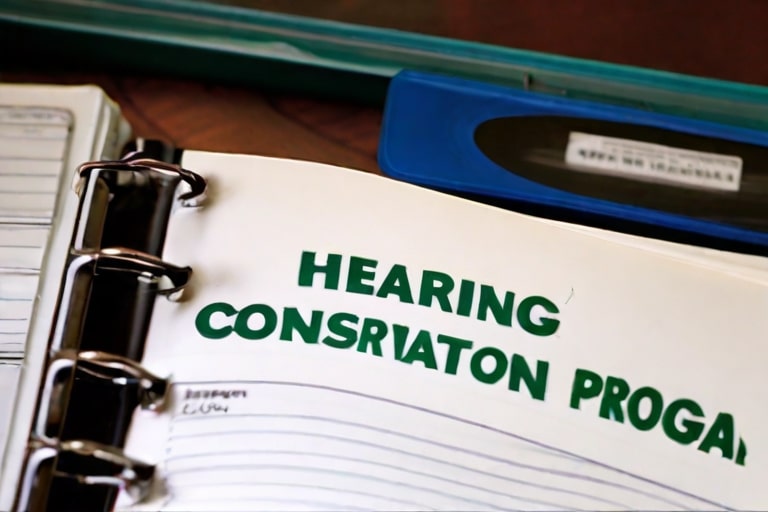
Hearing Conservation Program
What year did OSHA implement the hearing conservation program?
The biggest update to OSHA’s noise exposure regulations came in 1983 when the Hearing Conservation Amendment was implemented.
This amendment required all employers to implement hearing conservation programs when employees were exposed to noise levels at or above 85 dB for 8 hours.
An effective hearing conservation program consists of several main parts:
- First, the employer must identify and monitor those employees subject to excessive noise levels. This starts with an initial noise assessment. Employers have a fair amount of leeway when it comes to methods of noise monitoring and informing employees.
- Second, the employer must develop an audiologist testing program. This program must offer audiometric monitoring at no cost to employees covered by the hearing conservation program.
OSHA regulations also specify the employer’s responsibilities when it comes to hearing protection devices.
- Employers must offer a choice of hearing protection devices to employees covered by the conservation program: at least one needs to be plug-style, and at least one needs to be muff-style.
- Employees must wear hearing protectors prior to getting a baseline audiometric screening anytime they’re exposed to a weighted average of 90dB or above or if an audiologist has determined them to be sensitive to noise.
- Employees need to be fitted for a hearing protector by a trained individual who can help ensure a proper fit. Employers must do testing to ensure that the hearing protectors do an adequate job of noise reduction; it’s not sufficient to go by the product’s listed noise reduction rating.
- Employers must provide training to employees on occupational hearing conservation. They must also provide training on proper care of personal protective equipment.
EPA Regulations
The EPA was created in 1972, and it soon began to tackle noise pollution as part of its remit to provide a clean environment to all Americans. The agency developed its own permissible exposure limit for sound in 1974 – 55dB over 24 hours. During the day, sound shouldn’t rise above a 75dB average.
The World Health Organization quickly adopted this EPA standard and is still the standard to which much of the world aspires. However, the Noise Office of the EPA was broken up in the early 1980s and hasn’t been reformed. The same regulations are on the books, but there are no enforcement mechanisms.
Recently, though, there’s been talk about bringing the noise office back. Getting on top of noise levels in the workplace can help employers stay ahead of any new regulations.
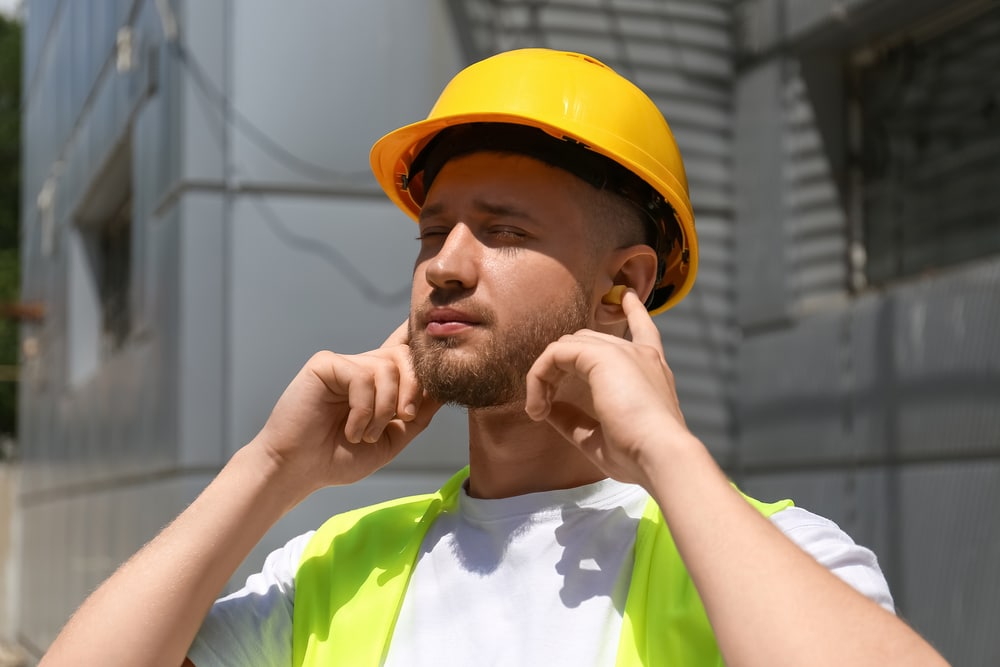
NIOSH
NIOSH was established by the OSH Act of 1970 as an independent industrial hygiene research body. The idea is that NIOSH researches workplace safety topics, and OSHA uses the findings to inform policy.
The NIOSH-published standard for noise exposures is a weighted average of 85 dB over 8 hours. Their estimates tend to be slightly more conservative than OSHA’s.
Non-Profit Organizations
Federal government agencies and non-profits work together closely when it comes to preventing occupational hearing loss. The American Industrial Hygiene Association is one organization that provides information to employers and industrial hygienists – their Noise Manual is a practical guide that’s widely used and quoted.
The National Hearing Conservation Association offers great resources on different hearing protection devices.
New Directions and Current Challenges
After 50 years of OSHA and a governmental focus on hearing loss prevention, where are we today? What advancements are being made in hearing protection?
Hearing Loss as an Occupational Safety Hazard
The biggest challenge in hearing loss prevention is getting people to take it seriously as a part of occupational health. It’s a challenge that regulators face, but employers face a similar challenge in getting employees to care about preventing hearing loss.
The answer is education. The statistics on occupational hearing loss are staggering, especially in certain industries. About a quarter of construction workers exposed to high levels of noise have a material hearing impairment.
Most workers, once they know the pertinent information and how to protect themselves, are enthusiastic about hearing conservation programs.
Making a Niche Field Cool
Let’s face it – there will never be a Hollywood blockbuster about industrial hygiene. And even beyond the “cool factor,” hearing loss prevention has a few other challenges.
We’re only a few generations into our society’s focus on hearing. Many of the occupational hazards in today’s workplace didn’t even exist 40 years ago. The field is having to constantly respond to novel workplace exposures.
This can make it hard to prove that hearing loss data obtained in a study is directly related to any change in the workplace. Developing a detailed analysis of the situation in an industry can be tough.
Still, employers have clear guidelines from regulators and the technology to help meet them. The original NIOSH criteria document from 1971 hasn’t changed all that much.
When employers understand the scope of the issue and provide proper employee training, it’s not hard to meet OSHA’s hearing protection standards.
Need Noise Safety Training?
If you need to update your hearing conservation program training, look at our large video library. A multimedia presentation can help you get the point across to all your employees! Hearing protection has a long history in the United States, and all efforts should be made to protect an employee’s hearing. This benefits both employers and employees alike and keeps your company in line with OSHA requirements.