Ensuring Safety During Forklift Refueling and Recharging
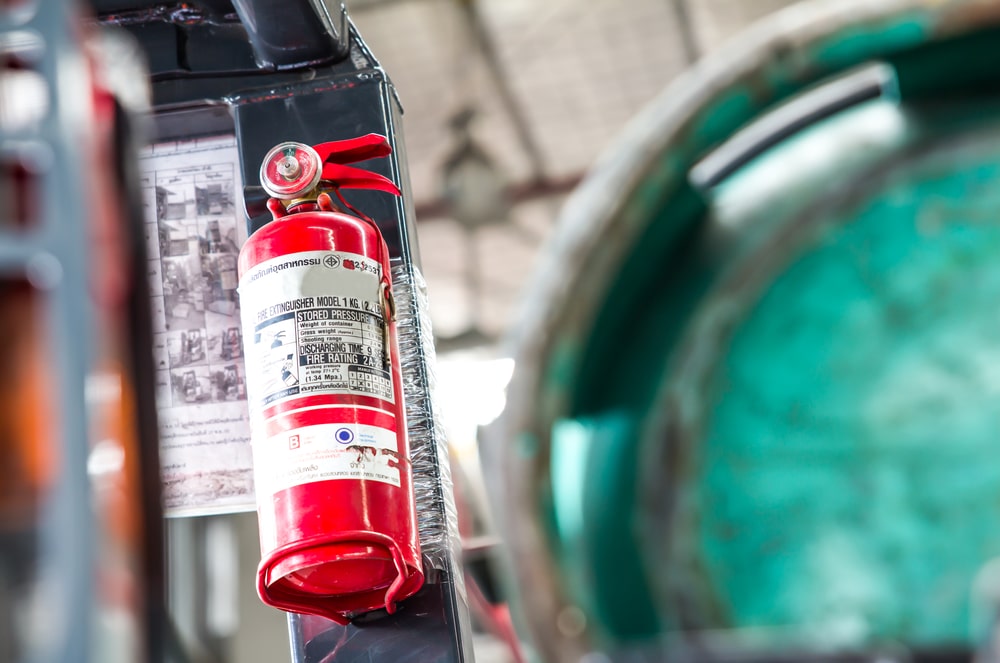
Forklifts are useful but potentially dangerous pieces of equipment. One of the riskiest moments during their use is when an operator refuels or recharges a forklift. The chances of injury are there, and fire hazards are also present.
Forklift accidents can have serious financial repercussions for your organization; OSHA fees and other expenses can easily reach six figures. Read on to learn more about safety for forklift refueling and recharging and how training your employees can really help.
If your employees need OSHA forklift training, we have a complete program.
Why Is Forklift Safety So Important?
Forklifts may be small, but they can cause some big accidents. An average of 87 people die every year in the US as a result of forklift accidents, and that number is only increasing. About 35,000 forklift incidents result in serious injury.
Training can help minimize forklift accidents and save lives.
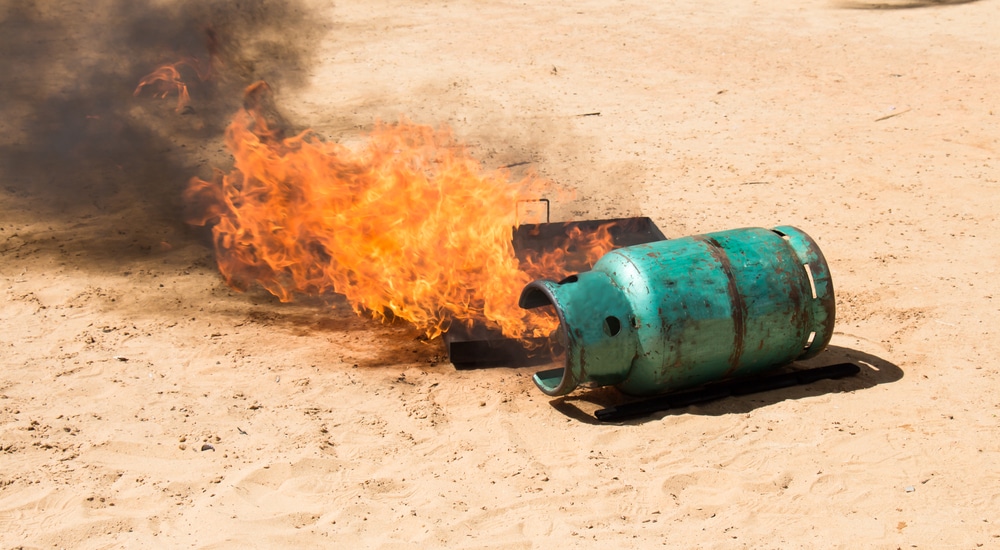
Costs to Employers
Forklift accidents can also cost you big. One organization found the average forklift accident costs $38,000 in direct costs like worker’s comp. It’s an additional $150,000 in indirect costs like lost productivity and decreased morale.
If you’re a small or medium-sized organization, inadequate training can really wipe you out. Proper training for forklift operators just makes financial sense.
The Employer’s Responsibilities
Employers must create and administer forklift training to all operators. This training needs to include both a lecture/video component as well as demonstrations and practice with an actual forklift.
An employer needs to certify that a forklift operator is trained and safe to operate forklifts. This training needs to be refreshed every three years or:
- After the employee is seen operating a forklift incorrectly or has been involved in an accident or near-miss.
- When operating conditions in the workplace change.
- When an operator is assigned to another vehicle or type of load.
Many accidents occur during forklift refueling and recharging. Even experienced operators aren’t immune. Be sure to include those topics in your forklift training.
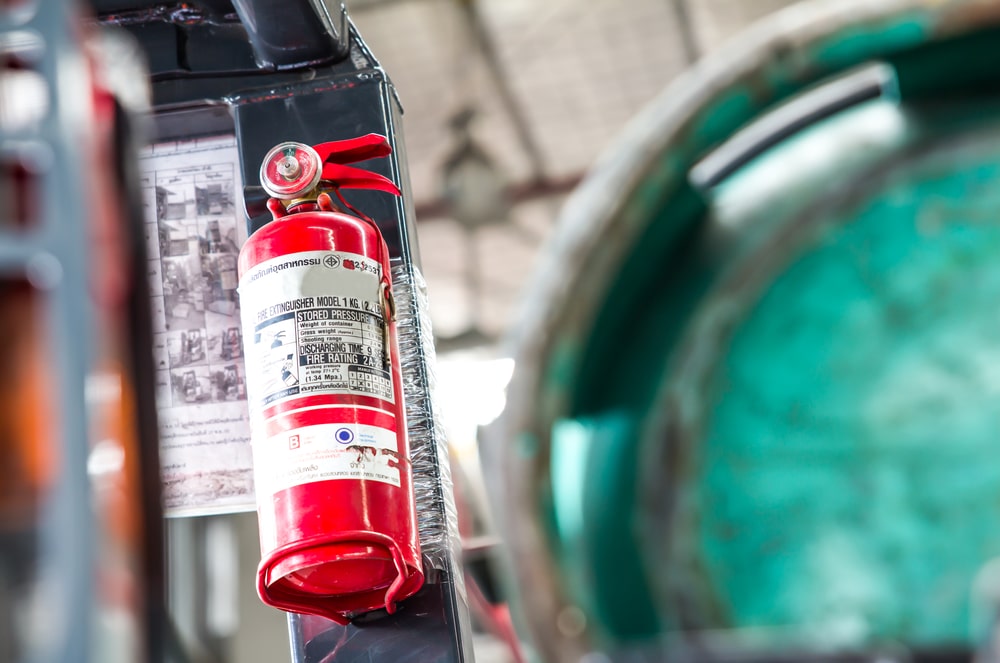
Diesel Forklift Refueling
- Turn off the engine and engage the parking brake. Make sure the fork of the forklift is fully lowered.
- Unscrew the fuel cap slowly – evaporated diesel can cause pressure buildup inside the tank.
- Insert the fuel nozzle into the tank and make sure it’s secure.
- Start fueling and stop when the tank is about 90% full of fuel.
- Wipe up any fuel spills or drips, and wash your hands after refueling.
- If you’re aware of any leaks, report them to a supervisor or designated safety officer.
A diesel refuel area should be a safe distance from hazards like open flames, machines that spark, and active traffic lanes.
LPG Forklift Refueling
- LPG fueling should only be done in designated areas. Park the forklift and remove any load prior to refuel.
- Ensure the engine and fuel isolating valve are both shut-off.
- Remove the old cylinder and replace it with the new one.
- Ensure the new cylinder is positioned with the safety relief valve facing upwards.
- If you’re aware of any signs of leaks, report them immediately to your supervisor or a designated safety officer.
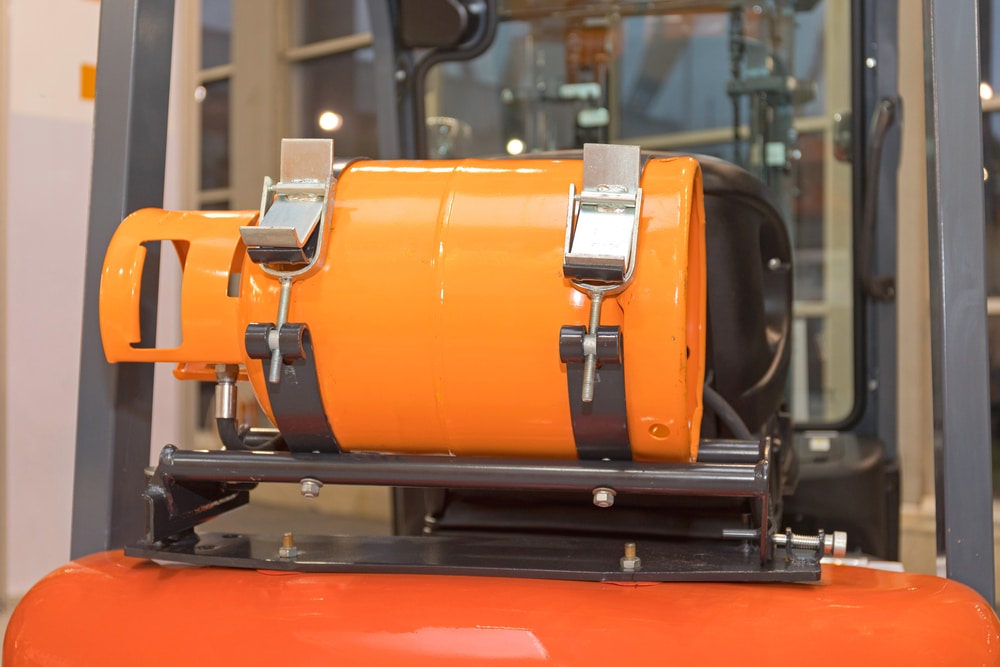
What Precautions Should Be Taken When Refueling a Gas Propane Lift?
LPG is stored at a temperature of -44F – that’s cold enough to cause frostbite. It’s also heavier than air, so it can displace oxygen and cause asphyxiation. Avoid close proximity to pits or holes where the gas can pool.
You should only perform LPG forklift refueling wearing gloves and goggles. There should be adequate ventilation as well.
Electric Forklifts
Flooded Lead-Acid Batteries
You should plan on only getting one shift (8 hours) of work a day out of one of these batteries. After that, they’ll take about another 8 hours to charge and another 8 to cool down before the next workday.
These batteries also contain liquid acid electrolytes that can splash out. Always change a flooded lead-acid battery while wearing safety equipment (apron, goggles, and gloves).
- Remove the battery and use a pallet jack to move it to the charger.
- Use the correct charger and ensure neither the charger nor the battery is cracked. (Alert your supervisor if you see a crack.)
- Place a charged battery in the lift truck using the pallet jack.
- Put a bit of distilled water into the battery after charging to correct the fluid levels.
If you’re unable to remove the battery from the forklift prior to charging, ensure the battery compartment is open so gases can escape.
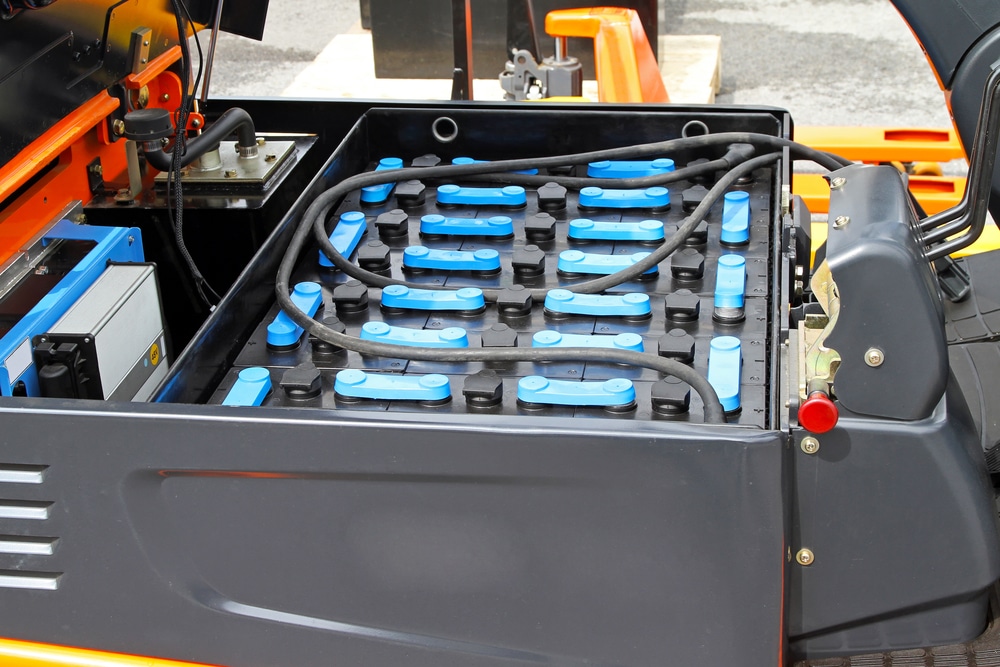
Lithium Ion Batteries
These batteries are fairly straightforward to charge. They also have fewer safety indications than other types. However, there’s still a fire risk.
Take a look at these forklift safety tips:
- Ensure the appropriate safety equipment is in the charging area – this includes a fire extinguisher that can handle lithium ion fires.
- Cool down the batteries before and after charging.
- Never use aftermarket chargers, cables, or other equipment.
- In the event of a fire, immediately evacuate and contact emergency services.
What Should the Operator Do When Refueling or Recharging a Forklift?
No matter what the refueling and recharging situation, there are a few things operators should always do:
- Turn off the engine as soon as the vehicle is in the refueling or recharging area.
- Keep open flames and sparks away from the vehicle – your fueling area should not double as a smoking lounge.
- Ensure the fueling area is well-ventilated and away from operating trucks.
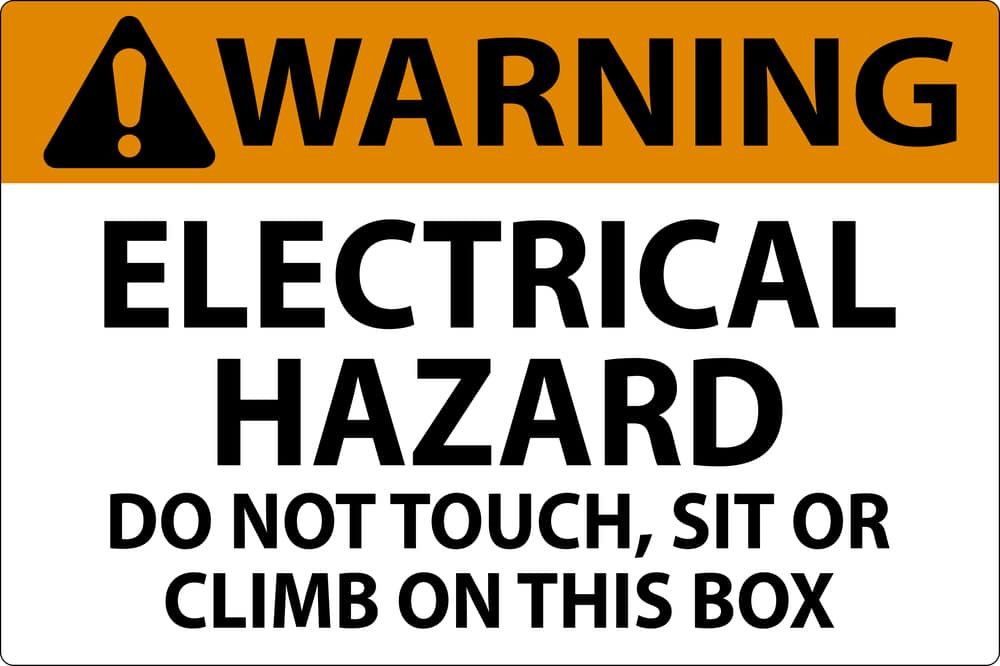
Creating a Culture of Safety for Forklift Operators
Safety administration is everyone’s job – both employees and employers have their roles to play.
Employees need to operate forklifts correctly. In addition to refueling and recharging only in the designated area, this means:
- Ensuring a safe operating distance between the forklift and other vehicles and equipment.
- Having two hands on the steering wheel at all times.
- Being aware of the height of a lifted load as well as the height of the mast and overhead guard.
- Checking tire and fluid levels frequently.
- Never trying to lift people on a forklift.
- Ensuring heavy loads are within the forklift’s capability.
- Avoiding pedestrian walkways while operating a forklift.
- Not wearing loose clothing on the job.
- Wearing all appropriate safety equipment, including hard hats.
Employers can support a culture of safety by:
- Stressing to employees the importance of occupational health and safety it should be more important to avoid injury than to exceed quotas.
- Providing training to all forklift operators.
- Planning worksite traffic patterns that avoid blind corners and hazardous areas.
- Providing supplement training when needed.
- Taking operators seriously when they report potential hazards and faulty equipment.
Employers also need to properly maintain forklifts and other trucks.
Forklift Safety Checklists
You can help ensure compliance with forklift safety precautions by developing checklists. A checklist for the truck refueling and recharging process can make sure workers take all necessary safety measures.
Place checklists and additional safety tips at load docks and fueling areas. The process to refuel a truck can have many steps, and it’s good to have a reminder.
What Does OSHA Say About Forklift Safety?
OSHA mandates that employers provide proper training and a hazard-free work environment. If an employer fails to provide that to forklift operators, they could incur serious fees. OSHA even has a free guide for employers on forklift safety.
OSHA charges a maximum of $12,675 for a non-serious violation. That can increase to $126,749 for repeated or willful violations. If you’re a small or mid-sized employer, that’s a lot of money.
Prevent Forklift Accidents – Train All Workers on Forklift Safety
Training for your forklift operators is an absolute must. It’s the only way to empower your employees with the knowledge to do their jobs safely and efficiently, with minimal risk of injury to themselves, their fellow workers, and the work area itself.
Check out our library or engaging employee training videos on every workplace safety topic.