Best Practices for Workplace Noise Monitoring Programs
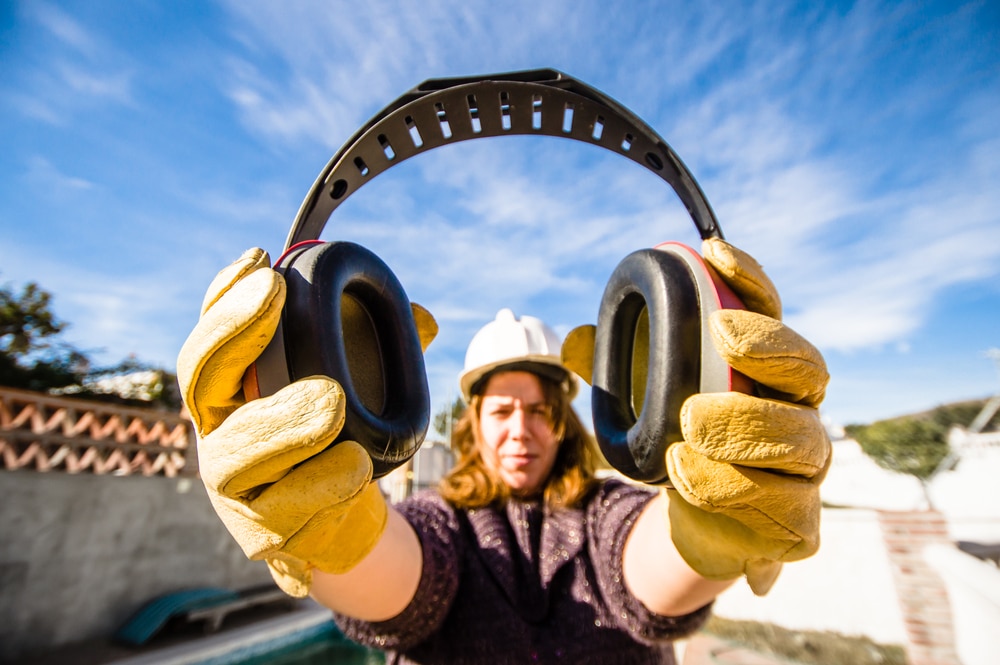
Noise control is vital to occupational safety. Specific job tasks have higher average noise levels than others, but even mild to moderate noise exposure can damage workers’ hearing over time.
Prolonged exposure to chronic loud noise can result in partial or permanent hearing loss. A well-designed hearing conservation program should protect all workers exposed to unhealthy sound levels.
Keep reading to learn about the hazards of occupational noise exposure and how hearing conservation programs protect workers from excessive noise in the workplace.
If you need a hearing conservation training program for your employees, we have a full course available.
When Is a Loud Workplace Hazardous?
How much noise is too much?
The National Institute for Occupational Safety and Health (NIOSH) states that daily noise exposure of 85 decibels or more over an 8-hour time-weighted average constitutes a hazardous work environment.
There must be a hearing loss conservation and sound monitoring program in any workplace where the average noise level regularly exceeds this recommended exposure limit (REL).
If workers must raise their voices in order to communicate with each other from a distance of three feet apart, noise levels should be considered dangerous.
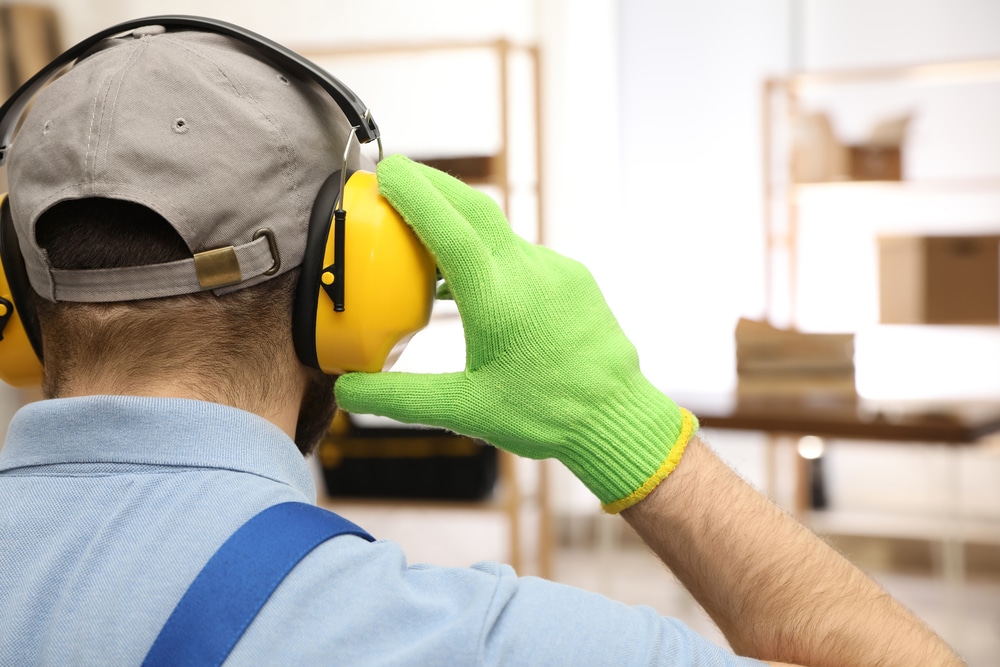
Potential Consequences of Excessive Noise Exposure
Unregulated sound levels can affect a workplace in two major ways: by endangering employee health and through financial consequences for the company.
Consequences for Worker Health
Working in an environment with an unhealthy sound level throughout an entire workday – whether it be from machinery, tools, vehicles, or a poorly serviced ventilation system – can have devastating and even permanent outcomes for exposed employees.
Hearing loss is the most obvious – though not the only – health consequence of working in noisy areas for extended periods of time. Noise-induced hearing loss can be a threat at any workplace, not just construction sites or industrial facilities.
Some other potential consequences of long-term exposure to unhealthy noise levels include:
- High stress levels
- Anxiety
- Depression
- Heart disease
- Tinnitus
Repeated exposures can worsen these symptoms, all of which can have permanent impacts on worker health and safety.

Financial Liabilities
Workers suffering from initial occupational hearing loss may choose to leave their jobs to protect their remaining hearing.
A high rate of employee turnover is a bad look for any business. It results in an unstable and inconsistent work environment. It can also make hiring highly qualified workers difficult, hurting productivity and efficiency, ultimately affecting revenue.
Neglecting to prioritize occupational health in the workplace can result in heavy fines, legal fees, and lower revenue. Fines vary from state to state and can easily surpass tens of thousands of dollars. Workers’ compensation and lawsuits due to workplace injuries can also drain the company’s finances.
Workplace sound level is controllable, and hearing loss due to occupational noise exposure is 100% preventable. The best course of action is to be proactive in identifying each potential noise hazard in the workplace and addressing it before it affects workers’ health.
What Are the Standards for Noise Monitoring?
OSHA and NIOSH both mandate that every employer whose workers are exposed to time-weighted average (TWA) noise levels of 85 decibels or higher must institute an employee training program that educates workers on protecting their health and hearing.
In many cases, it will be necessary for employees to measure the sound level in their work area using noise monitoring equipment such as sound level meters and dosimeters.
Employers are responsible for ensuring employee participation in this training program.
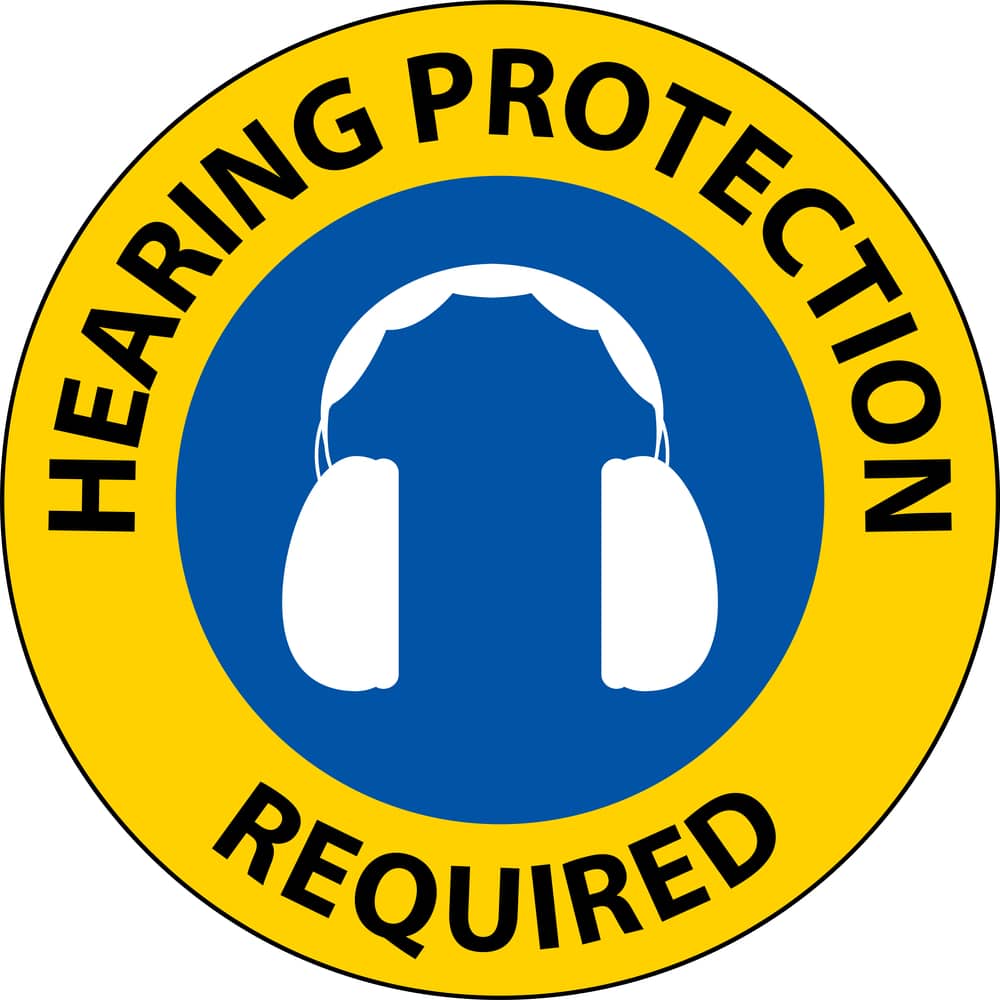
Key Elements of a Hearing Conservation Program
Noise control is everyone’s responsibility in the work area.
Effective hearing conservation programs must take a comprehensive approach to identifying, monitoring, and alerting workers to hazardous noise sources within the work area.
The purpose of a hearing conservation program is to empower all employees with the knowledge and training to protect themselves and fellow workers from dangerous noise exposures.
Here are some of the steps these programs should incorporate to ensure worker health and safety.
Measure and Monitor Noise Levels Using Sound Level Meters (SLMs) and Other Tools
Effective noise controls depend on accurate measurements of sound levels within the work area.
In order to protect their workers, employers must know the following about their facilities:
- The noise levels within each given zone (in other words, how loud those areas are)
- How much of that sound can reach a worker’s ear
- The sound frequencies within those noises
- The noise source for each potentially hazardous sound level
Employers can determine these factors by taking detailed noise surveys of their facilities. A noise survey is conducted by collecting noise measurements in the work zone.
There are two primary methods for taking sound level measurements. They are:
- Sound level meters (SLMs). A sound level meter allows workers to assess the noise level in a given area, figure out how much sound a particular machine or piece of equipment produces, and obtain a general idea of the frequency of that sound. Employees can use a sound level meter to measure the sound pressure levels in a particular area in real-time.
- Dosimeters. These devices measure the personal noise exposure of each worker by assessing their noise dose.
A sound level meter is most useful in environments where the noise level is relatively consistent and workers tend to remain in one place throughout the day.
If noise levels fluctuate or employees are required to move around frequently, personal monitoring devices like dosimeters are more effective.
Reporting work area noise levels is usually achieved using one of these three parameters:
- Sound level. This is the measured noise level at a given moment within the workspace.
- Time-weighted average (TWA). This measurement describes the average noise level over an exposure time of eight hours.
- Noise dose. This is the percentage of acceptable noise exposure for a worker throughout an eight-hour period. If the noise dose reaches or exceeds 100%, that employee has surpassed their daily exposure limit and is in danger of hearing loss and other adverse health effects.
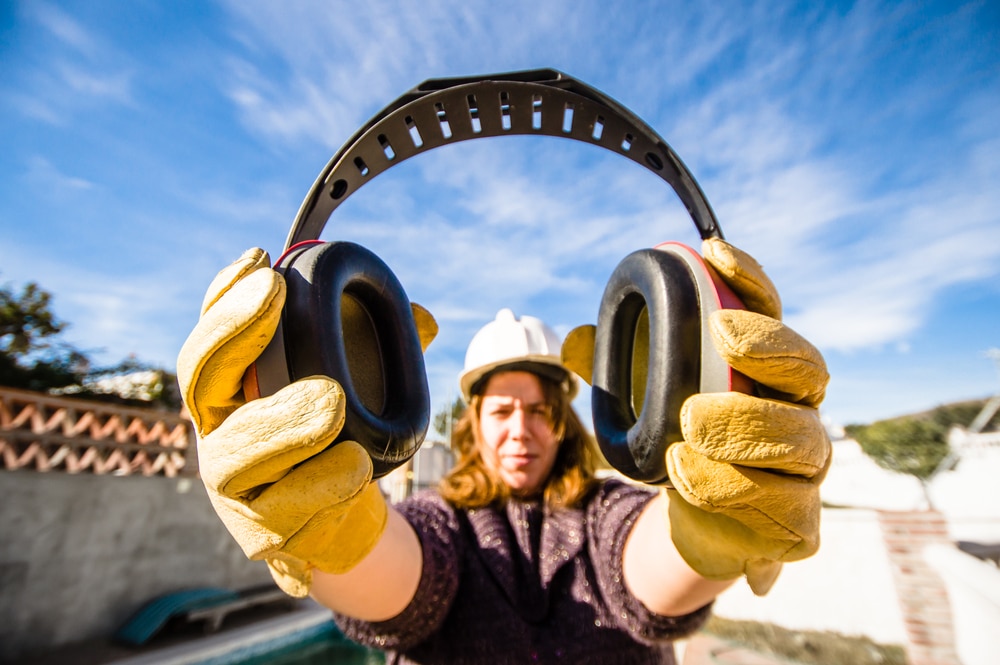
Create a Sound Map of Expected Workplace Noise Exposure
Once the workplace has been assessed using a sound level meter, it will be easier to determine where the noise level needs to be controlled and where workers should wear hearing protection while on the job.
To create a sound map, workers should move throughout the facility using a sound level meter to measure the frequencies in each area. Measurements should be taken every few feet, with sound levels being measured for at least 30 seconds in each zone.
These measurements must then be recorded on a facility map showing where each piece of equipment and worker is located.
When the map is complete, pinpoint the loudest areas within the facility and determine whether the machines or equipment in those areas need to be replaced. If replacement isn’t possible, consider implementing engineering controls to dampen or reduce the sound.
Evaluate Employee Noise Exposures
Conducting noise surveys of the facility as a whole will determine the specific areas in which hazardous sound levels are present. The next step is to use personal noise dosimeters to figure out which workers are subjected to sounds over NIOSH’s recommended limits throughout their workdays.
To conduct their personal noise survey, each worker must:
- Calibrate their dosimeter before and after every use
- Set the device to NIOSH’s recommended settings
- Affix the dosimeter’s microphone to the shoulder on the side with the highest exposure (follow the user manual for specific guidelines)
- Ensure the microphone is pointed upwards, away from clothing – use a windscreen for added isolation
- Record each measurement in detail and update records each time a survey is conducted
Employees whose measured sound exposures exceed the recommended limit must be enrolled in a hearing loss program.
Replace Noisy Equipment and Implement Sound Barriers
Use the sound map to identify each hazardous noise source within the facility. Noisy machines and equipment may need to be serviced or replaced.
If possible, consider replacing loud devices with low-noise tools. Other methods of isolating or reducing sound in the workplace include:
- Acoustic barriers and foams
- Soundproof doors and windows
- Sound absorption systems
- Ceiling baffles
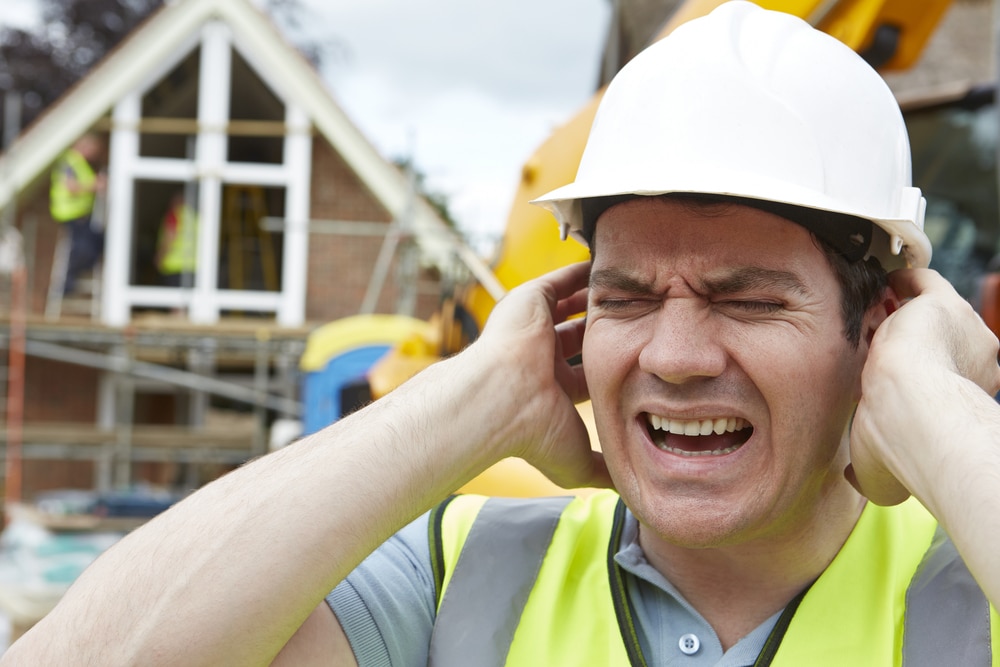
Provide Personal Protective Equipment (PPE)
Hearing protection devices are the best form of personal protective equipment for defending employees from hearing loss. The most common hearing protectors are ear muffs and earplugs.
Ear muffs should cover the outer ear completely. Tighten the fit by adjusting the headband as needed. The earpiece must stay in place over the outer ear in order to ensure the worker remains protected throughout the day.
Earplugs are inserted into the ear canal to totally block sound from entering. Earplugs come in disposable and reusable varieties and can be purchased in many sizes. A secure fit is crucial to ensure effective sound blocking.
In a loud work environment, personal hearing protection can make all the difference in preventing loss of hearing.
Test Employee Hearing Frequently
Providing free annual hearing exams to all employees within the hearing conservation program can help catch and address hearing loss before it becomes permanent. Establishing a baseline for hearing using audiometric testing is a good first step.
Establish workers’ baseline hearing when they are first hired or enrolled in the program. This will provide a comparison point to help determine whether there are any changes over time in their ability to hear.
After a full day of sound exposure, annual tests should be conducted at or near the end of workers’ shifts.
Suppose a significant threshold shift (STS) is detected when comparing a worker’s most recent hearing exam to their baseline test result. In that case, that worker should be informed immediately so that appropriate steps can be taken to prevent any further changes.
Possible adjustments include moving the worker to a less noisy area, testing the worker’s hearing protection, and re-training the worker on proper safety procedures.
Educate Employees on Noise Exposure
Communication and education are the two best defenses when it comes to protecting workers from unhealthy sound exposure.
If workers are aware of the dangers of loud workplaces and empowered to measure their individual sound exposures over time, they will become more adept at protecting themselves and increase the effectiveness of the hearing conservation program.
Encourage workers to communicate with you about their experiences with the program. Use the following strategies to boost worker engagement and ensure everyone is on the same page about safety procedures within the workplace:
- Emphasize that the results of sound measurements will be used to increase workplace safety
- Share all noise maps of the work area with employees
- Highlight loud areas using signs
Monitoring Occupational Noise Exposure: Final Thoughts
The potential hazards and health consequences of noisy workplaces should not be underestimated.
By staying aware of mandated noise exposure limits and monitoring sound levels within the facilities, employers can protect their workers from hearing loss and other long-term consequences of working in loud environments.
Implementing noise controls, requiring the use of hearing protection, and establishing comprehensive hearing conservation programs that include regular sound monitoring are three key ways to keep workers healthy and maintain a safe and productive workplace.
Frequently Asked Questions
What are the OSHA requirements for noise monitoring?
Under OSHA regulations, employers must institute a hearing conservation program when exposures register at or above 85 decibels on average over an 8-hour time-weighted average (TWA).
What is the OSHA noise conservation program?
A hearing loss program is designed to protect employees from dangerous noise exposure levels in the workplace through the use of engineering or administrative controls and personal protective equipment.
What is a reliable method to measure noise levels in the workplace?
The best way to take personal noise measurements is to use noise dosimeters. Employees should wear their dosimeters throughout their total exposure time.
Sound level meters provide accurate measurements of noises throughout the facility as a whole.