Why Is Lab Safety Important?
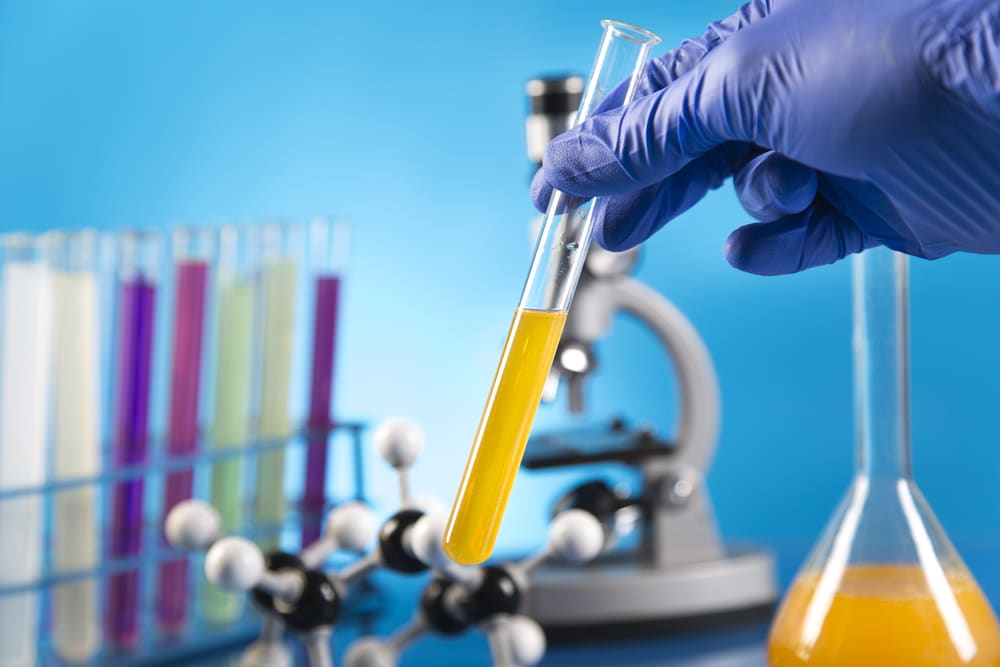
Occupational safety is a key aspect of every work environment. Laboratories have particularly stringent safety procedures due to potential hazards, such as dangerous chemicals, flammable solvents, and specialized electrical equipment.
Lab safety is the responsibility of everyone at the job site. There’s no room for negligence in a laboratory setting; workers must follow all lab safety rules to the letter, including wearing appropriate personal protective equipment and using the relevant lab safety equipment for their given jobs.
Let’s explore why all labs need to implement and prioritize lab safety rules. We’ll also cover some of the most important rules of basic laboratory safety and discuss the equipment all labs should have to keep their workers and communities safe. Also, if you want to check out some lab safety courses, we also have those available.
Reasons to Prioritize Lab Safety
Why is lab safety important? Because it saves lives, protects the environment, and avoids devastating losses in productivity and revenue.
Labs must implement and enforce guidelines to protect laboratory workers from all possible hazards present within the workplace. A well-regulated operation is a safe operation.
Detailed safety procedures are the key to running a lab that checks and controls hazardous conditions to the fullest extent possible, thereby minimizing risk to its employees and the broader community.
Providing some lab safety tips to your lab workers can help with laboratory safety. Here are a few benefits of educating and training laboratory employees on all aspects of lab safety relevant to their work and daily tasks.
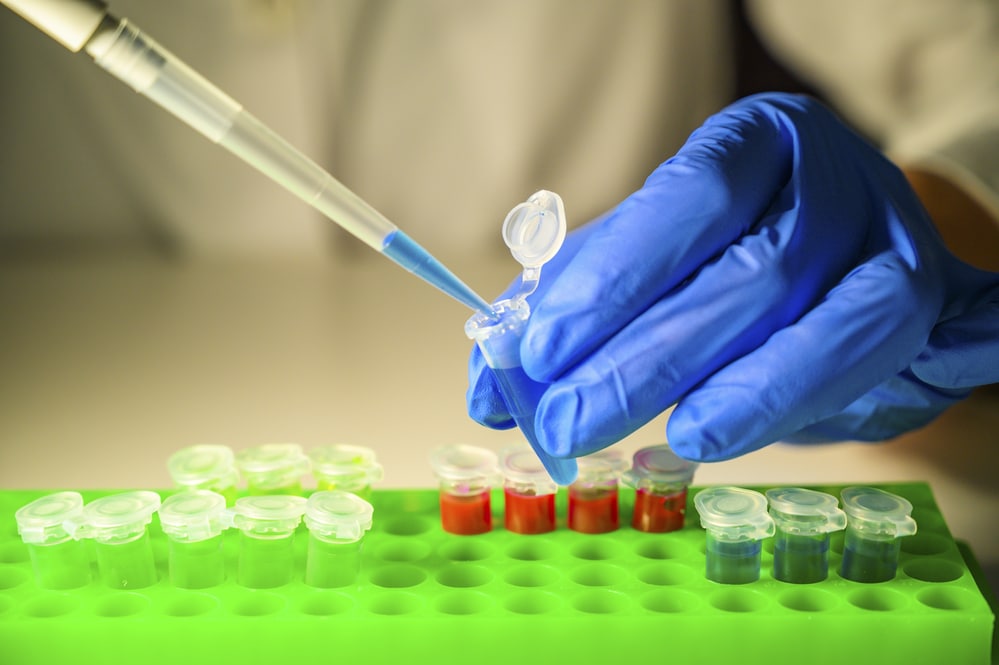
1. Prevents Accidents and Injuries
One of the foremost reasons for implementing laboratory safety protocols is to prevent employee injury. Another is to limit the chances of accidents that could harm environmental and community health, disrupt the workplace, or damage costly equipment.
2. Promotes Safe Handling of Hazardous Materials
Hazardous chemicals, flammable liquids, and other dangerous substances in a lab must be handled carefully to ensure safety. Chemical spills can cause debilitating burns and rashes; inhaling toxic fumes leads to respiratory issues and long-term health complications. This is why the labeling of chemical containers is so important.
Lab safety guidelines minimize these risks by ensuring that all employees working with hazardous materials are properly trained on and aware of all safe handling procedures relevant to the substances they are regularly exposed to.
3. Keeps Operations Running Smoothly
Safety breaches can cause serious downtime in laboratory operations, slowing the research process and potentially leading to severe losses.
Lab safety practices ensure that all activities within the workspace are executed with maximum efficiency at the least possible risk.
4. Ensures Proper Use of Laboratory Equipment
Laboratory workers must be rigorously trained to safely operate all laboratory equipment, such as Bunsen burners, crucibles, and any other tools involving high heat or hazardous substances.
Tools for handling lab chemicals are often delicate and require a steady hand to ensure they are used correctly and safely. Lab safety rules that explain the hazards and safe handling procedures associated with each piece of equipment help reduce the risk of employee injury and expensive damages to the equipment.
5. Ensures Workers Stay Safe in Hazardous Environments
Finally, lab safety helps employees stay abreast of the potential hazards present within the laboratory.
Lab safety rules remind employees to wear proper personal protective equipment, such as lab coats, eye protection, and gloves. They point out the lab’s location and proper usage of all safety equipment.
Having guidelines on protecting themselves and what to do in emergency arms lab workers against any laboratory hazards that could jeopardize their health and safety.
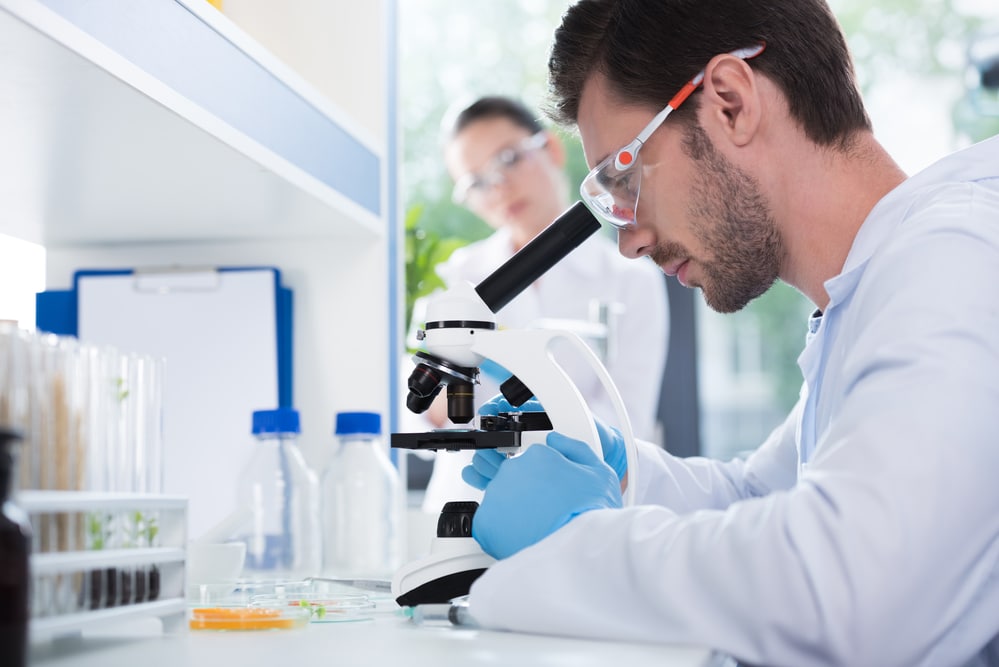
Common Lab Safety Rules
Lab safety protocols serve to prevent accidents and educate workers on creating and maintaining the safest possible work environment. Many labs implement OSHA’s laboratory safety guidelines to protect their workers from harm.
This is by no means an exhaustive list. Lab operators should assess their workplace’s specific needs and develop guidelines relevant to the lab’s daily tasks, dangerous chemicals, possible hazards, and safety equipment.
1. Be Aware of All Potential Hazards
Laboratory technicians must be aware of all potential dangers as they work, including any chemical, mechanical, electrical, and physical hazards present in the workplace.
Potential risks include corrosive and explosive chemicals, equipment that could break or malfunction, and sharp tools that could cause injury if used incorrectly.
All personal protective equipment, lab safety equipment, and laboratory machines should be inspected before each use. Machines must receive regular maintenance to ensure they remain in good working order.
2. Know the Location and Proper Use of Lab Safety Equipment
Workers should know where they can find lab safety equipment, such as eyewash stations, first aid kits, and fire extinguishers. They must also be fully trained on how to use this equipment in the event of an incident.
3. Handle Chemicals With Care
Employees should take steps to minimize chemical exposures to the fullest extent possible. Technicians should never sniff chemicals or combine unknown reagents without extensive planning and calculation.
All waste chemicals should be disposed of promptly and in the correct receptacles.
Hygiene and containment plans must be in place detailing what to do if an employee is exposed to a hazardous chemical or if dangerous substances are released into the wider community surrounding the lab.
4. Prevent Cross-Contamination
Lab workers must not eat or drink anything inside the laboratory. Hazardous substances in the workplace could contaminate the food, leading to illness and other health complications.
In maximum containment laboratory facilities, workers may be required to use disinfecting showers before entering and exiting the lab. These facilities often implement airlock entrances and exits to keep harmful pathogens from escaping control.
5. Keep the Environment Clean and Controlled
Employees should never apply cosmetics within the laboratory, especially in the vicinity of an open flame.
After eating, using the bathroom, or leaving the sterile area, all employees should wash and sanitize their hands thoroughly and carry out any other relevant decontamination procedures before returning to the lab.
Known or possible exposures must be monitored rigorously, including medical evaluations when necessary.
6. Wear Protective Gear
All lab workers must wear the necessary personal protective equipment to do their jobs safely. Protective gear may include safety glasses, lab coats, pressurized suits, and close-toed shoes.
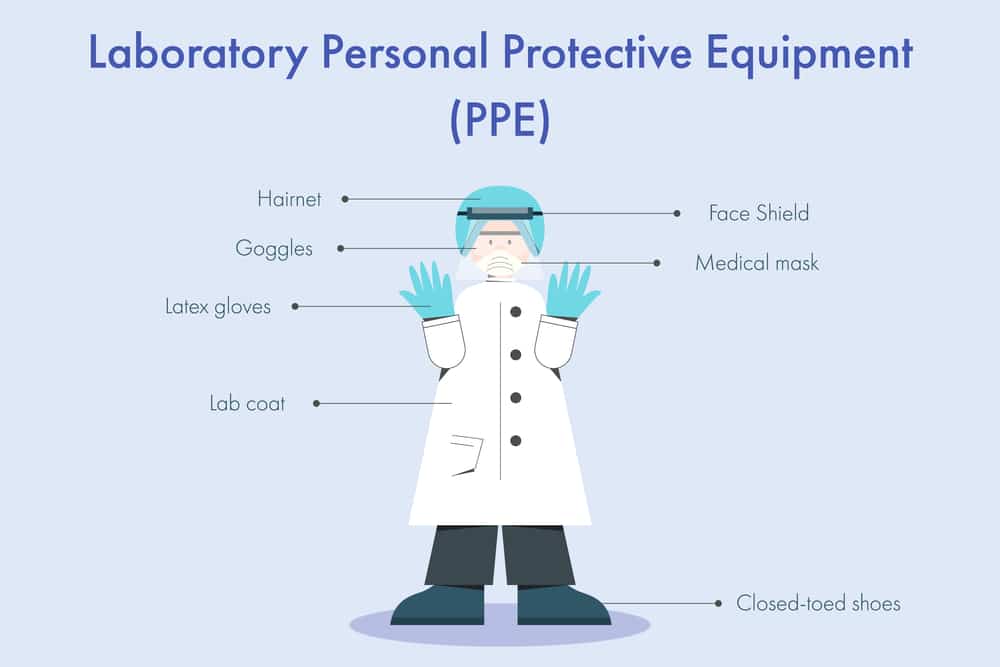
7. Have Emergency Phone Numbers Posted in Plain Sight
In an emergency situation, having the contact information for local emergency services displayed in a central location could save lives. All lab employees should know how to contact the nearest fire department and emergency medical professionals.
If a spill, explosion, leak, or other dangerous event occurs, workers should be offered medical consultations to determine whether further examinations or treatments are needed. The attending physician must be informed of any chemicals within the workplace that the employee may have been exposed to.
Lab Safety Equipment
Stocking and maintaining proper laboratory safety equipment comprises a crucial chunk of creating a safe and high-functioning workspace.
Personal Protective Equipment
No technician should show up for work without the appropriate personal protective equipment (PPE). Employers should always make sure their workers have the gear they need to do their jobs safely and efficiently.
Appropriate PPE is the last line of defense against most workplace hazards. If a spill or explosion occurs, PPE can shield workers from the worst effects, potentially saving their lives and preserving their long-term health.
Here are a few of the most common pieces of gear lab technicians will need in order to handle chemicals safely.
LAB COATS
To be considered properly protective, a lab coat must fit correctly and remain closed at all times while working in the lab. It should be stored apart from the worker’s regular clothes when not being worn.
EYE PROTECTION
Laboratory eye protection can include the following:
- Safety glasses. These are best suited for lower-risk environments. They can protect workers’ eyes from flying objects but lack the proper coverage or a protective seal to keep out splashes, fumes, and toxic vapors.
- Safety goggles. When properly fitted, goggles provide the best possible defense against chemical exposure and airborne particles because they create a tight seal around the eyes.
- Face shields. Face shields are often used in conjunction with goggles and/or glasses to add a layer of splash protection across the worker’s entire face.
GLOVES
Since lab technicians’ hands frequently come into contact with chemicals, gloves are among the most common and essential personal protective gear in laboratory settings.
Gloves protect hands and fingers from laboratory mishaps such as chemical spills, cuts, and burns.
LONG PANTS
In most lab settings, exposed skin is a significant safety hazard, especially when corrosive, flammable, or otherwise dangerous chemicals are involved. Lab workers should always wear long pants that reach all the way to their closed-toed shoes or boots, covering their ankles.
FULL-BODY SUITS
In some laboratories, a lab coat isn’t sufficient for protecting workers from the hazards that may be present.
A full-body suit – also called a positive pressure personnel suit – is a highly specialized protection garment that completely encapsulates the entire head and body. These suits are used in maximum containment and biocontainment laboratory facilities that research dangerous pathogens.
Lab Equipment for Safety
Aside from PPE, there are many pieces of laboratory safety equipment workers should be aware of and know how to use in order to protect themselves and their communities.
FUME HOODS
A fume hood protects the rest of the lab while technicians work with explosive, flammable, or otherwise unstable chemicals. Operators should ensure the hood sash is at the correct height and that the air gauge, exhaust fan, and air filters are all clean and functional before using the fume hood.
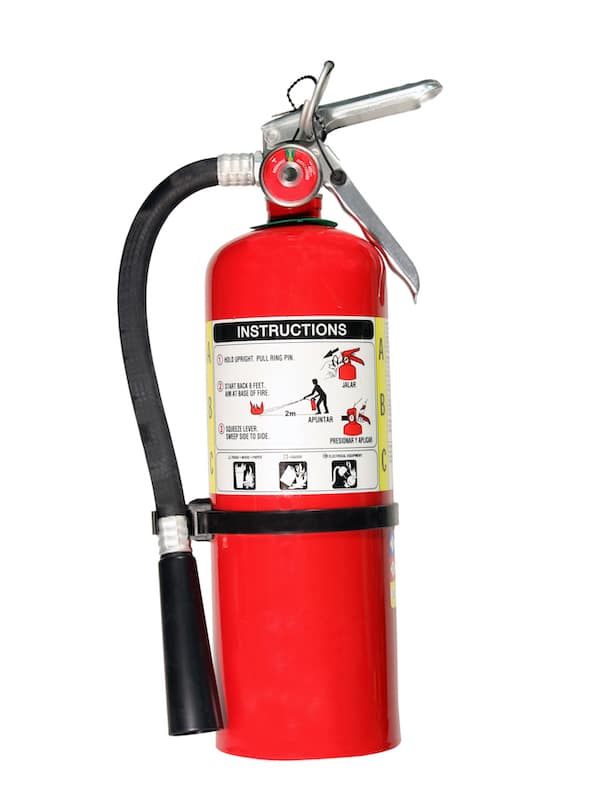
FIRE EXTINGUISHERS
In all laboratories – but especially those working with combustible materials – fire extinguishers should be stationed at convenient access points throughout the workspace.
All fire extinguishers should be inspected regularly to ensure they remain up-to-date and in good working condition.
SAFETY SHOWERS
Safety showers are often present in workplaces with a decontamination zone at the entrance and/or exit. They disinfect workers’ full-body suits, ensuring no harmful pathogens escape the controlled zone.
FIRST AID KITS
First aid kits are essential for treating minor injuries during the workday, such as small cuts and insignificant burns. They can also buy time until emergency services arrive in the event of a more serious incident.
Frequently Asked Questions About Laboratory Safety
Now that we’ve tackled “Why is lab safety important?”, here are a few additional questions people often have related to lab safety practices.
There are many more than two reasons – however, here are the two most commonly cited:
1) To reduce the risk of accidents and injuries to laboratory employees.
2) To reduce any risk to the wider community, including devastating environmental impacts and releasing hazardous substances into local water sources.
OSHA’s Laboratory Safety Guidance Standard includes the following five main elements:
1) Identifying hazards
2) Creating a chemical hygiene plan
3) Training and educating employees
4) Keeping track of any exposures
5) Providing medical consultations and exams
Hazard inspectors list the following as some of the most common safety violations observed in laboratory settings:
– Keeping flammable and combustible materials close to the ceiling (too close for optimal sprinkler range)
– Storing dangerous chemicals at or above eye level
– Improper labeling of disposals or containers meant for liquid waste
– Containers with illegible or fading labels or with the label peeling off
– Chemical containers that have degraded over time and are at risk of breaking suddenly
Insufficient or improperly worn protective equipment
Why Is Lab Safety Important? – Final Thoughts
Research in laboratories often involves dangerous chemicals, complex equipment, and harmful pathogens. These elements can present severe personal and environmental health hazards if not properly handled or controlled.
Laboratories must outline and implement stringent safety protocols to prevent accidents and lower the risk of uncontrolled encounters with hazardous substances. Failure to do so can result in more than just a hefty fine; it could lead to devastating environmental impacts, serious injury, and even death.
Keeping their workers and community safe should be the number one priority for all employers.