Common Laboratory Hazards – [Updated for 2023]
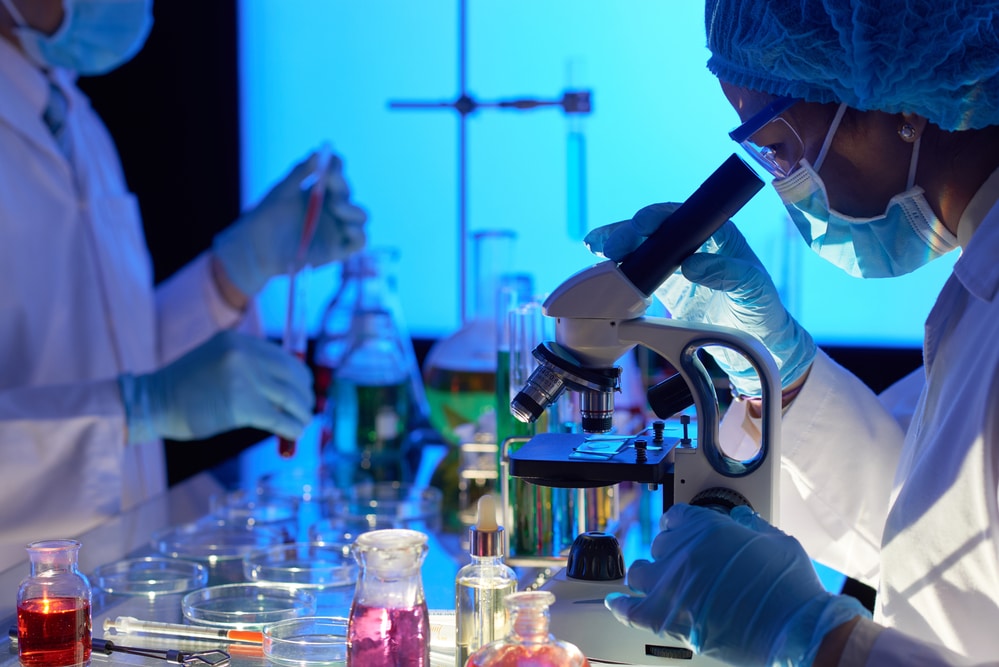
Conducting scientific research often involves working with hazardous materials and dangerous equipment. Workers may also be exposed to physical and electrical stressors and mechanical, thermal, and ergonomic hazards.
Identifying and controlling common hazards helps protect laboratory workers from immediate harm and long-term health problems.
Here are several of the most common safety hazards of working in a laboratory setting. If you want a full training course – we have a full set of laboratory safety courses available.
Chemical Hazards
Practicing chemical safety is paramount in all labs that handle hazardous chemicals. It’s also critical that all chemicals be labeled appropriately.
Chemical exposure can damage the sensitive mucous membranes in the nose and throat. Affected workers may experience long-term health effects that could lower their quality of life and even shorten their lifespans.
Chemical burns are often serious injuries requiring extensive treatment. Any worker handling toxic, corrosive, or otherwise dangerous chemicals must wear personal protective gear such as gloves, goggles, a laboratory coat, and closed-toed shoes or boots.
Many chemicals can pose significant threats to the workspace and the environment if improperly disposed of or mishandled. Explosive and flammable substances should be stored and handled with extreme caution. Never allow employees to pour toxic substances down drains, into toilets, or anywhere they could contaminate the local water supply.
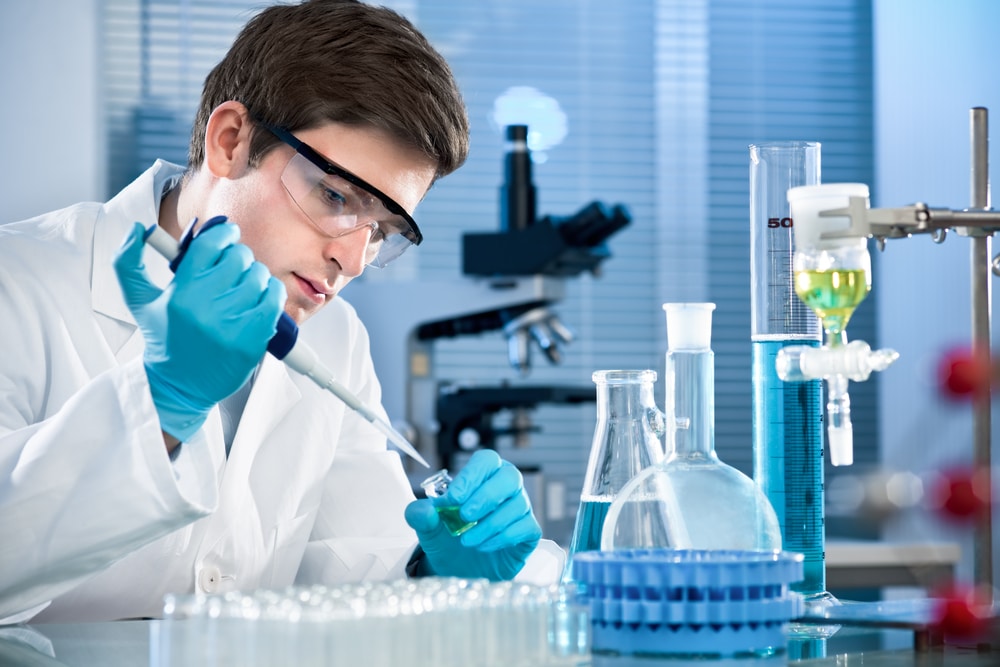
Classes of Hazardous Chemicals
The following are examples of chemical hazards associated with laboratory work:
- Flammable liquids (gasoline, acetone, alcohols)
- Radioactive materials (radium, uranium)
- Corrosive substances (acids, ammonia, bromine)
- Explosive substances (nitrocellulose, dry picric acid, dry benzoyl peroxide)
Physical Hazards
Physical injury is common in labs due to the long hours and demanding labor often involved in day-to-day operations.
Common physical safety hazards include:
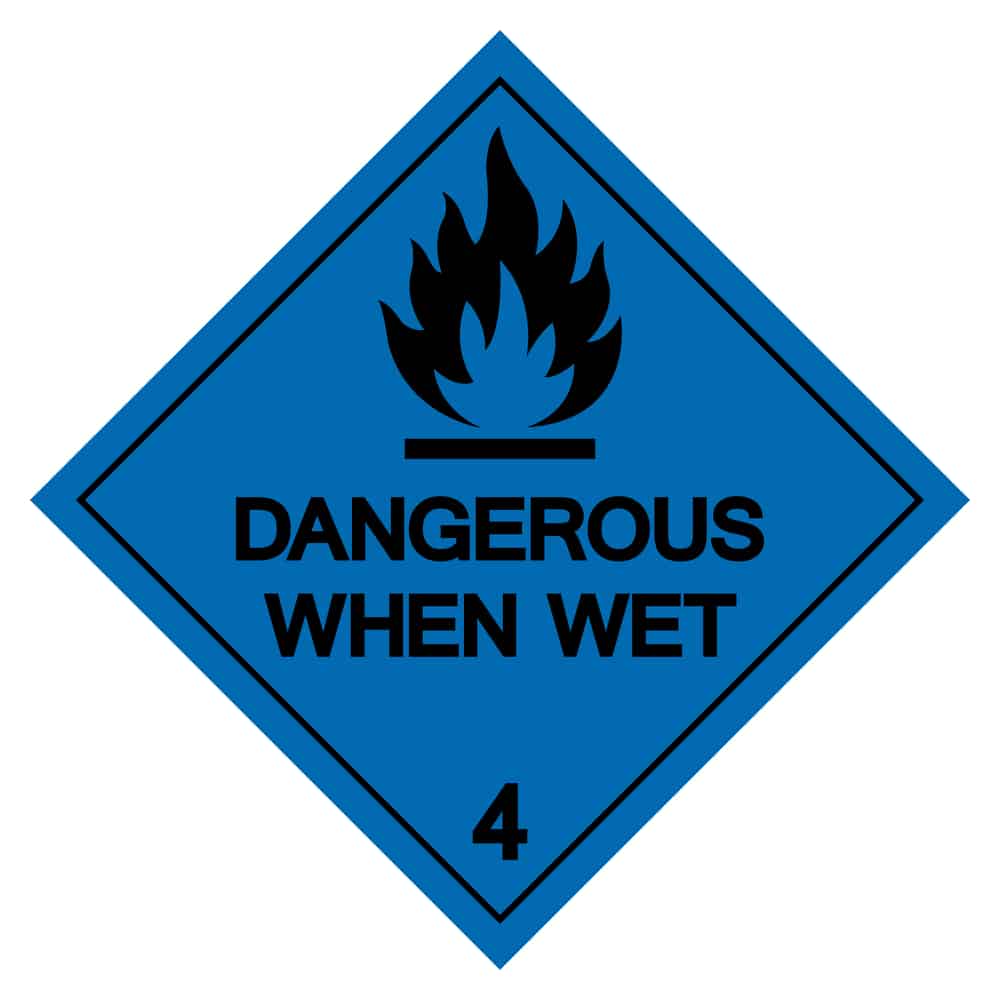
- Slips, trips, and falls due to spills or obstructions.
- Improperly stored sharps
- Broken glassware
- Musculoskeletal injuries from the improper lifting of heavy loads
- Eye strain due to improper lighting
- Back and shoulder pain from hunching over lab tables or working in confined spaces
Ensure all employees know where and how to dispose of sharp objects. Instruct workers on the proper methods for lifting heavy loads and make lifting equipment, such as dollies, readily available throughout the workspace.
Keep all walkways, stairwells, exits, and workspaces clear and free from obstructions. Employees should have access to storage lockers where they can leave any personal belongings like backpacks, coats, and purses.
Biological Hazards
Any laboratory work involving potentially hazardous biological agents should be considered dangerous. Workers must exercise caution when working with biological hazards to prevent accidents that could cause detrimental health effects within the facility or in the greater community.
Biohazards that are often studied in labs include:
- Viruses
- Bacteria
- Molds and fungi
- Parasites
- Blood and body tissue
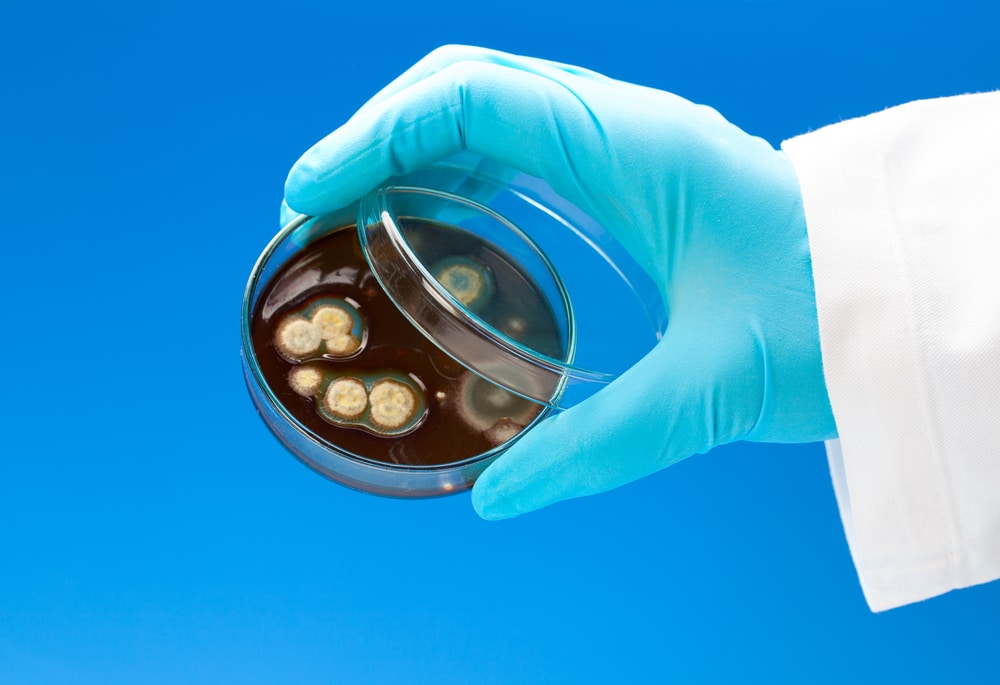
Containment facilities must be regularly inspected for malfunctions and signs of weakness. Anyone working directly with biohazards should wear a lab coat, goggles, face shields, gloves, and other PPE.
Clean rooms have particularly stringent requirements for preventing biohazards from breaching containment. These often include full-body suits and safety showers that decontaminate workers from head to toe at the beginning and end of each shift.
Electrical Hazards
Since most labs use electrified equipment, electrical hazard reduction is a key component of laboratory safety protocols.
Possible electrical hazards include:
- Electrical shock
- Second- and third-degree burns
- Fires
- Arc flash
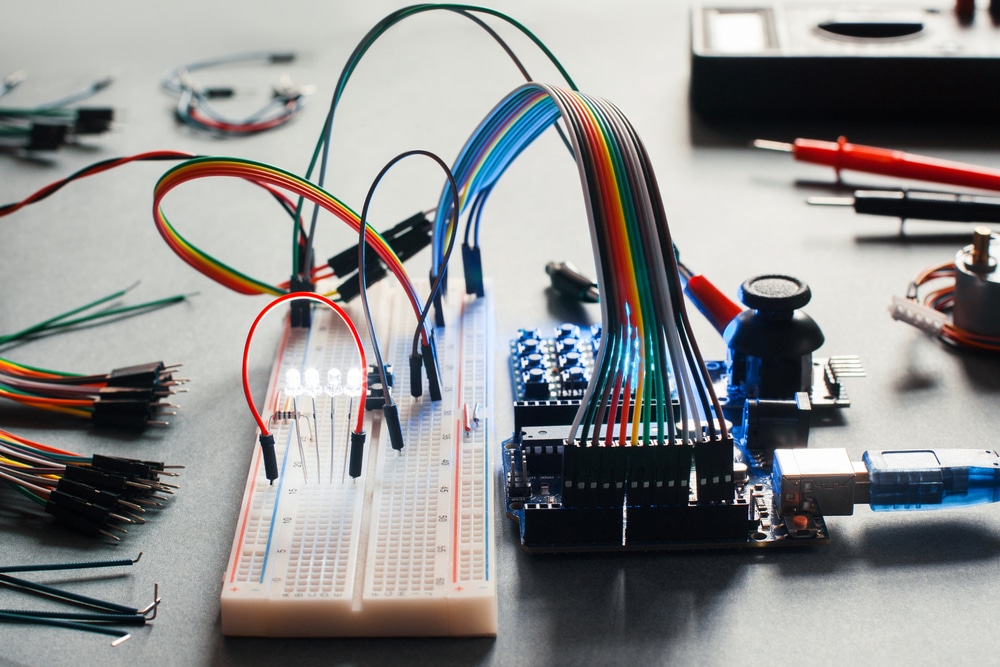
All electrical outlets, cords, and equipment should be inspected regularly. If possible, faulty machines and components should be removed from the workspace and labeled with appropriate signage.
Ensure electrical machines and cords are kept clear of encroaching water. Leaks must be isolated and repaired swiftly.
Ensure all lab workers follow proper protocols for working on de-energized electrical equipment, including lockout/tagout procedures and deploying signage to alert other lab workers of potential hazards in the area.
Only authorized employees and professionals should be allowed to service laboratory machines.
Mechanical Hazards
Many laboratory machines threaten worker health and safety if improperly used or poorly maintained.
The following are examples of risks that can come with using laboratory machines:
- Cuts and stab wounds from sharp edges
- Crushing and pinching injuries from moving parts
- Burns from hot surfaces
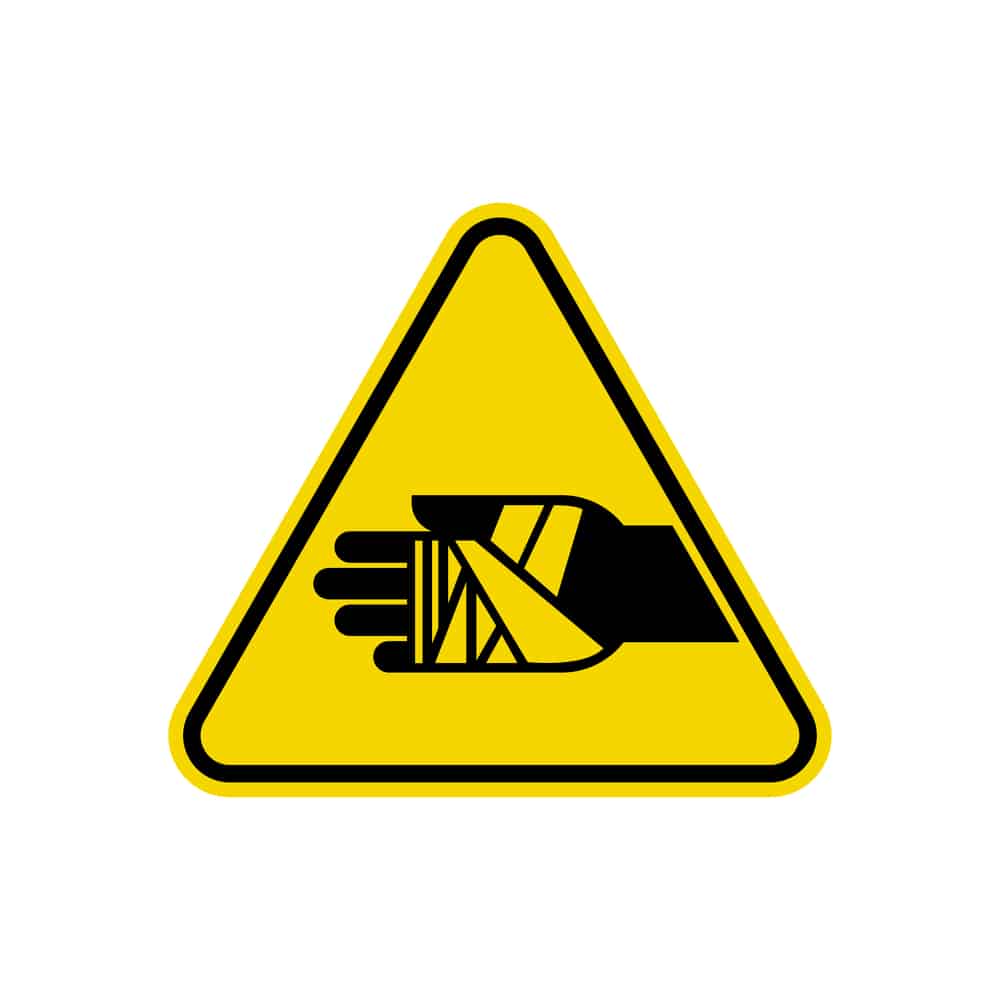
Regularly maintaining equipment is an essential aspect of laboratory safety. Workers must be educated on the proper precautions to take when working with machines in the lab, including how to tell when a machine isn’t functioning properly.
Most machines come with manufacturer-installed warning placards listing the dangers of that machine’s operation. Ensure these placards are visible, legible, and unobstructed at all times.
Employees should receive training every time a new machine is introduced to the workspace and after any accident or incident involving improper machine use. Never allow fatigued or distracted employees to operate dangerous machinery.
Thermal Hazards
A thermal hazard has the potential to alter a person’s body temperature harmfully. These can include heat and cold hazards.
Many laboratories work with flammable materials, including gasoline, turpentine, and flammable gases. Other heat hazards commonly seen in labs include open flames like Bunsen burners and heating implements like mantles and hot plates.
A fire extinguisher should be kept by any laboratory station where work involves heat sources.
Extremely cold substances and conditions can also present a thermal hazard. Dry ice and cryogenic liquids can cause burns if handled without proper PPE.
Many laboratories store their specimens at cold or freezing temperatures to preserve them, and workers may suffer health issues such as hypothermia and frostbite if exposed to these conditions over even a short period of time without proper gear.
Instruct employees on any temperature-related dangers involved in their workspace and ensure everyone has access to a comfortable break room and the proper protective gear to protect them from extreme temperatures.
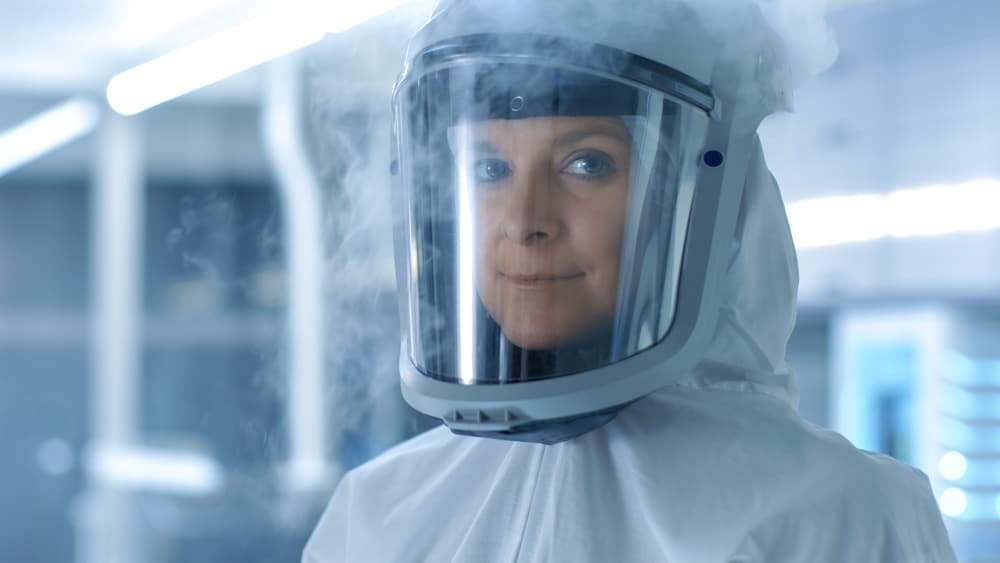
Other Health Hazards
Other hazards associated with working in labs include ergonomic stressors, noise, and allergens.
Ergonomic hazards seriously threaten workers’ long-term health and can cause serious strain and injury over time. Common ergonomic hazards in a laboratory setting include:
- Strains and other injuries from conducting repetitive tasks
- Injuries due to awkward posture or remaining for long periods in a stationary position
- Long-term exposure to intense vibration
Encourage workers to take regular breaks to avoid fatigue and muscle strain.
Noise is another laboratory hazard that many research labs overlook. Exposure to excessive noise for extended periods can cause severe hearing damage and is also associated with high blood pressure and stress levels. Identify intolerably loud areas within the lab and implement administrative controls to regulate the noise.
Many materials, fragrances, and foods can trigger dangerous allergic reactions. Encourage employees to report known allergies and consider banning common allergens from the break room and common areas. Workers should never eat or wear perfumes or cosmetics while working in the laboratory.
Combating Potential Hazards: Appropriate Safety Measures
Most common lab hazards can be prevented from spiraling into emergencies by implementing strict practices and protocols that instruct employees how to keep themselves and their colleagues safe while at work.
Personal Protective Equipment
It’s vital to wear appropriate PPE when working in a facility with biological, physical, and chemical hazards. Protective gear helps prevent skin contact with harmful substances.
Ensure lab staff has access to the following PPE at all times:
- Lab coats
- Protective eyewear such as goggles, face shields, and safety glasses
- Gloves
- Closed-toed shoes
Some lab work may require specialized gear such as hazmat suits or thermal protection. Refer to the U.S. Department of Health and Human Services or the National Institutes of Health for guidelines relevant to your specific type of research facility.
All protective gear should be inspected for holes, tears, and other signs of damage before each shift. Any faulty gear or safety equipment must be labeled and removed from the work site to avoid accidental use.

Proper Training
Rigorous employee training is the best way to teach workers how to identify hazards in the laboratory. Training should also cover the proper handling of laboratory equipment and hazardous chemicals.
Lab safety training programs vary from facility to facility. A comprehensive training program may include the following:
- Inspecting PPE, laboratory glassware, and other equipment before use
- Keeping long hair tied back at all times
- Safe operation and use of all tools, machines, and equipment in the workspace
- Knowing who is authorized to work in which areas
- What not to do in the workspace (e.g. eat, apply cosmetics or perfume, play distracting music)
Training should be mandatory for all new employees and anyone found violating any laboratory safety protocol or operating procedure.
Detailed Laboratory Safety Protocols
All laboratories should have a clear set of safety protocols outlining standard operating procedures for the workspace.
These protocols should cover any physical, thermal, biological, or chemical hazards present in the lab. They should outline the steps for working with any dangerous materials or substances employees might encounter as part of their daily tasks.
Protocols should explain how to check whether a workspace has proper ventilation before working with any substance that may emit fumes.
In labs where chemicals are used, the protocols should outline where to locate safety data sheets for each substance and how to fill out new data sheets for any additional chemicals brought into the lab.
List the machines and electrical equipment within the lab. Include the names of the employees who are authorized to work with those machines and the ones who are authorized to perform maintenance. Ensure workers who do not have proper authorization know they are not to use that equipment at any time.
Explain the rules for your facility, including where and how frequently employees should take breaks. Ensure everyone knows not to eat in the workspace.
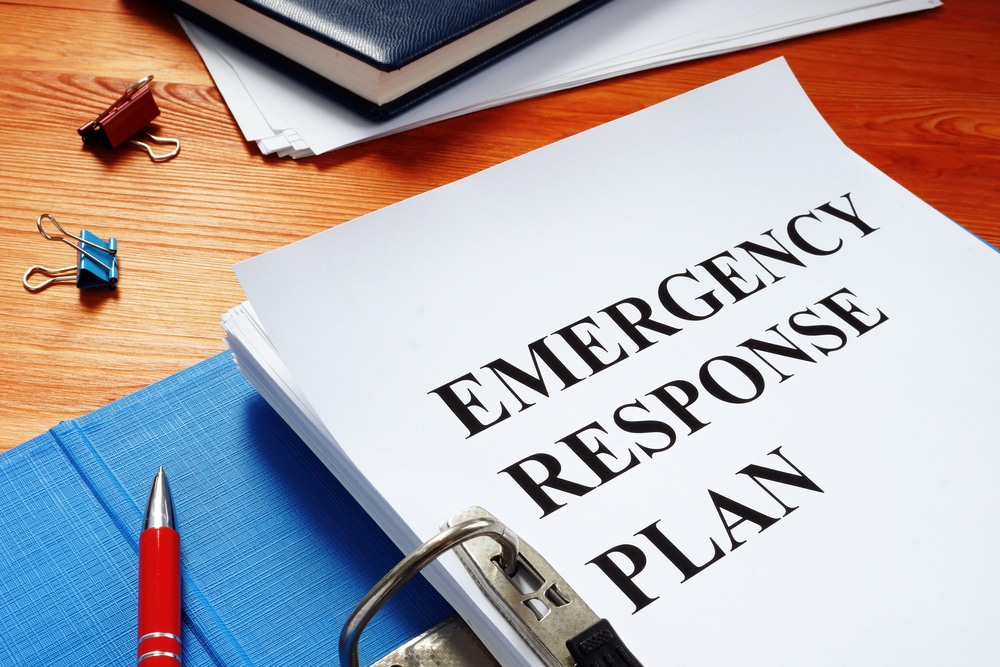
Emergency Response Plans
Every lab should have an emergency response plan that instructs workers how to act in the event of an emergency.
Depending on the hazards in that particular workspace, these plans vary from facility to facility. An effective plan might:
- Establish an inventory of every dangerous substance in the facility, including inflammable liquids, radioactive materials, biological materials, and compressed gases. Include the location, quantity, and properties of each substance.
- List the authorized personnel responsible for contacting the fire department, first responders, or other emergency response professionals.
- Provide instructions for personnel to follow if the fire alarm is triggered.
- List the location of all emergency equipment in the facility, including safety showers, eyewash stations, spill kits, and fire extinguishers.
- Describe the procedure for extinguishing fires on hair and clothing.
- Explain how to evacuate the building and where to gather once outside.
- Explain the protocols for ensuring all workers are accounted for during an evacuation.
- Instruct workers not to return to the lab until emergency personnel have declared it safe to do so.
Cover the emergency response plan in training and post a copy in a central area within the lab.
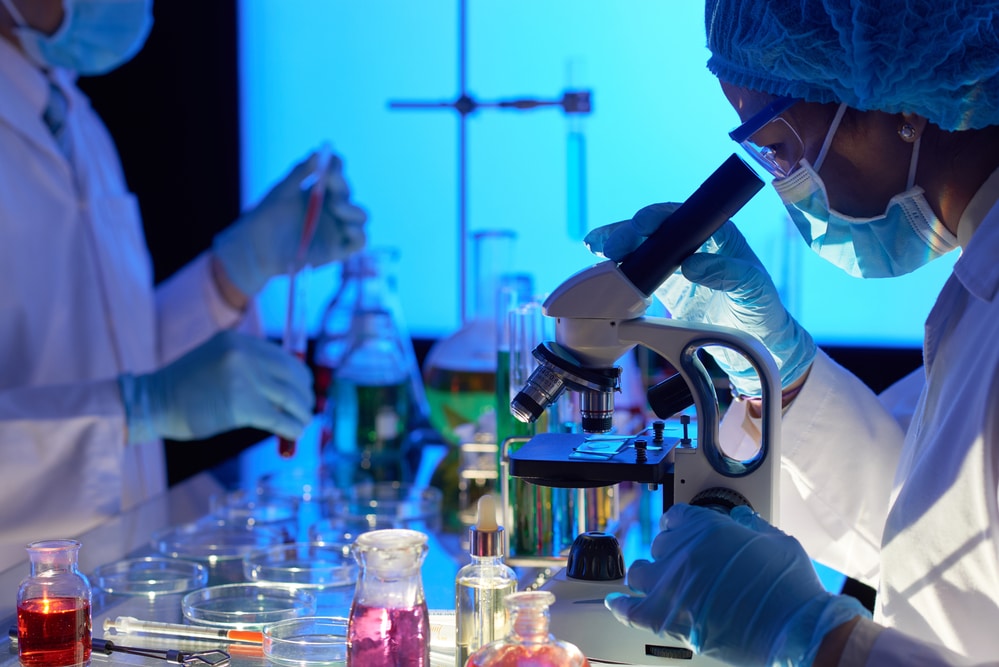
Final Thoughts
In conclusion, laboratory hazards – including physical, biological, and chemical hazards, among others – constantly exist in every research facility and lab setting.
Workers must be well-informed of all potential dangers involved in their work and have access to the protective gear and tools they need to do their jobs safely.
The biggest hazard in any work environment is ignorance. Ensuring everyone is on the same page about any hazards present in the workspace is the most important step toward preventing workplace accidents and injuries.
Frequently Asked Questions
The most common laboratory hazards include:
– Chemical burns
– Thermal burns
– Cuts from broken glassware
– Eye injuries
– Inhaling toxic fumes
Different facilities present different physical hazards depending on their specific layouts and the type of work or research conducted there.
Some hazards common to most labs include:
– Tripping over obstructions in walkways and stairwells
– Slipping and falling
– Puncture wounds and gashes from improperly handled sharps
– Ergonomic stressors like poor posture, repetitive tasks, and heavy lifting without proper assistance
1) Prolonged exposure to hazardous chemicals
2) Tired or inattentive laboratory workers
3) Not wearing appropriate PPE