What is Covered by the HAZCOM Standard?
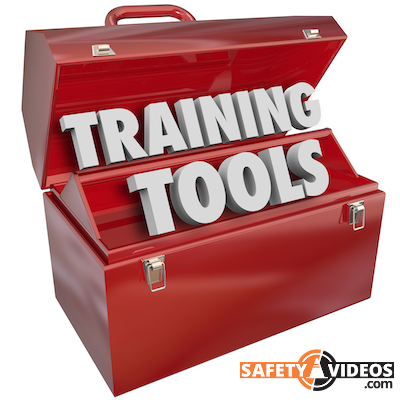
Any workplace that works with or around hazardous chemicals must follow OSHA’s Hazard Communication Standard often referred to as HazCom. Employers must understand the regulations and abide by them because hazardous materials present significant safety concerns for employees.
Similarly, employees who may be exposed to hazardous chemicals must understand the risks involved in chemical handling and receive thorough training relevant to chemical safety. A comprehensive grasp of the dangers of chemical exposure will place workers in a better position to avoid choices and behaviors that could increase the risk of an accident.
As the responsible party, the employer must implement the HazCom Standard for safely handling chemicals in the workplace. It includes a series of specific procedures, and relevant protective measures employees must follow to work safely with dangerous chemicals.
The HazCom Standard comprises five key elements: a thorough materials inventory and hazard information, material safety data sheets, how to prepare labels for containers of hazardous chemicals, training programs, and a written program outlining the HazCom Standard for safe work practices. We do offer a full-length HazCom Training video that will get you started on the right foot.
1. Taking Inventory of Hazardous Chemicals and Physical and Health Hazards
Employers must create a comprehensive list of all hazardous chemicals in the workplace. During the inventory process, verify that every hazardous material listed has appropriate labels and safety data sheets.
If no safety data sheet (SDS) is found, the employer should contact the chemical manufacturer or other responsible party for a replacement copy. Document every request made for each safety data sheet, including the date on which the new data sheet was received.
In addition to the materials inventory, all physical and health hazards posed by the chemicals in the workplace must be identified and listed.
Physical hazards of the chemicals may include flammability, explosive risks, corrosive properties, high compression, or an otherwise unstable nature. Such information should be provided via a detailed description in the materials inventory.
Health hazard categories include irritation, carcinogenicity, sensitization, and asphyxiant properties. Again, detailed information on the hazardous health effects of each specific chemical should be included in the inventory.
Other significant safety concerns in the workplace, such as dangerous equipment, may be identified during this process as well. Employees should be aware of all emergency protocols, including evacuation procedures. Signage and hazard lights should be deployed where appropriate.
2. Implementing a Process for Maintaining Safety Data Sheets
Safety data sheets include detailed information for every hazardous chemical in a workplace and should be sent by chemical manufacturers along with each delivery of hazardous chemicals. To create a universal method by which workplaces define hazards related to dangerous chemicals, all safety data sheets must contain the following information, including hazcom pictograms.
The properties of every chemical. This includes elements of the chemical’s expected visual appearance, such as color, odor, and consistency. It can also include flammability, the heat of combustion, boiling point, stability, and toxicity.
Each potential hazard afforded by the chemical. For instance, the chemical’s fumes are toxic when inhaled, or the substance will burn and corrode if it makes contact with bare skin.
Any environmental hazards the chemicals present. An example of an environmental hazard might be a substance that could pollute the water or soil if it leaches into the earth.
Protective measures to be taken for chemical safety. These measures include safe handling procedures, proper safety gear and protective equipment, and what to do in the event of a spill or exposure.
Safety precautions for transporting, storing, and handling all chemicals in the workplace. These precautions include the temperature at which chemicals should be stored, the type of vessel they may be stored in, and the level of pressure each substance can safely withstand.
Safety data sheets must be easily accessible and provide employees with detailed information regarding all hazardous materials present in the workplace.
While most data sheets contain sixteen sections, only twelve of them are considered mandatory. However, all sixteen sections must be present in order for the sheets to qualify as GHS compliant.
The first eight sections contain information relevant for people who will be handling the chemicals regularly, such as safe handling instructions. These sections are also relevant for emergency personnel responding to a catastrophe within the facility.
Sections nine through eleven cover scientific facts about the chemical, including reactivity and physical properties. Lab technicians and other persons who work closely with the substances are most likely to make use of these sections.
The final section comprises information about the data sheet itself, such as any revisions made and the date or dates of those revisions. This section should be updated each time new information about the chemical is discovered.
3. Using the Globally Harmonized System for Classification and Labeling of Chemicals (GHS)
All hazardous chemicals must be stored in a labeled container with a detailed description of the chemical inside and any relevant hazard warnings. Chemical manufacturers are responsible for providing these labels; however, the employer becomes responsible for creating new labels each time chemicals are transferred to new containers.
Since 2012, OSHA has implemented the Globally Harmonized System for Classification and Labeling of Chemicals (GHS) as part of its HazCom standard. This system has specific criteria that must be included on every label.
First, the chemical’s name and other identifying information should be clearly marked. The chemical’s name must be accompanied by a relevant pictogram depicting crucial information about the chemical that can be viewed at a glance. The GHS has designed the following nine pictograms for chemicals:
Secondly, each hazard class must provide a detailed hazard statement, along with precautionary statements outlining the chemical hazards. Each precautionary statement should explain the appropriate handling of the chemical in question.
The chemical manufacturer should also include its address, telephone number, and other contact information. This will allow employers to follow up if any relevant information is missing from the label or safety data sheets cannot be located.
Finally, the label must include a harmonized signal word that corresponds to the level of chemical hazard inherent in working with that particular substance.
4. Establishing Training Programs
Before receiving their initial assignment, every employee who may be exposed to hazardous materials as a result of their work must receive rigorous training in the identification and protective measures associated with every hazardous chemical. This training is essential to minimize the risk of injury or calamity in the workplace.
Every employee should receive additional training every time new chemicals are introduced to the job site. OSHA’s HazCom Standard outlines several strategies employers should implement in their training programs.
All training sessions should start with a discussion about each of the hazardous chemicals present in the work area. The trainer should go over the safety data sheets for each specific chemical, explain what to do in the event of an accident or spill, and cover all safety measures for preventing hazards.
Training should also cover the proper personal protective equipment (PPE) employees must wear before handling hazardous materials. Depending on the workplace and the hazards involved, proper PPE may include overalls, gloves, footwear, aprons, face shields, respirators, and chemical-resistant goggles or glasses. Employees should have access to PPE at all times and should know how to check whether their gear is functioning correctly.
As outlined by the HazCom Standard, educational sessions should make use of interactive learning devices such as videos, reenactments, and audiovisual aids in order to make the lessons more interesting and helpful for employees.
Similarly, all training sessions should be conducted in such a way as to be comprehensible by all employees regardless of literacy level. This may include offering bilingual sessions or multiple sessions in different languages to ensure every employee can absorb the material fully and without confusion.
The person in charge of training should group all chemicals by type or by function rather than presenting each one individually. This will make the information easier to comprehend, and it will also streamline the training process. An overview into the Globally Harmonized System may be incorporated into this part of the training to ensure employees understand how to read the labels they encounter.
Finally, not every employee will encounter every chemical hazard during the course of a normal workday. To avoid information overload, training sessions should be broken up into categories according to the chemicals an employee is expected to use or encounter during the course of the workday, and each employee should attend the training session relevant to them.
In addition to the above, employees should know where they can access safety data sheets, as well as the name of the individual in charge of implementing the HazCom Standard at the company. Workers should also know where to access and make copies of the company’s written hazard communication program.
5. Developing a Written Hazard Communication Program
The final element of the HazCom Standard involves creating a written program outlining every aspect of producing, handling, and working with hazardous materials and chemicals. Two key elements of this plan include familiarizing employees with the risks involved in handling the various chemicals in the work area and ensuring everyone understands the labeling system and which symbols correspond to which chemicals.
The written program should be specific to the company. It must include sections on labeling chemicals, conducting a materials inventory, locating and interpreting safety data sheets, and running employee training sessions.
A company’s hazard communication program should be seen as a living document rather than a static one. It must be updated every time a new chemical is brought into the workplace, as well as every time new personal protective equipment is invented or introduced.
Employees should have access to the current hazard communication plan at all times, and should be updated every time anything is added to or changed about the program. They should also be permitted to make copies of the plan at any time.
In Conclusion
The HazCom Standard ensures employees are aware of all health and safety hazards related to working with dangerous chemicals, thereby lessening the risk of accidents and injuries resulting from exposure. Hopefully, this short guide on What the HAZCOM Standard Covers has helped.
Employers working in industries that use hazardous chemicals are responsible for educating their workers on the various hazards and implementing the five key elements of the HazCom Standard to their fullest ability.
Guided by the steps outlined in the HazCom Standard, employees have the tools and knowledge to protect themselves against health and safety hazards in the workplace. These practices go a long way toward ensuring a safer work environment for all.